filmov
tv
A complete grounding rod production process
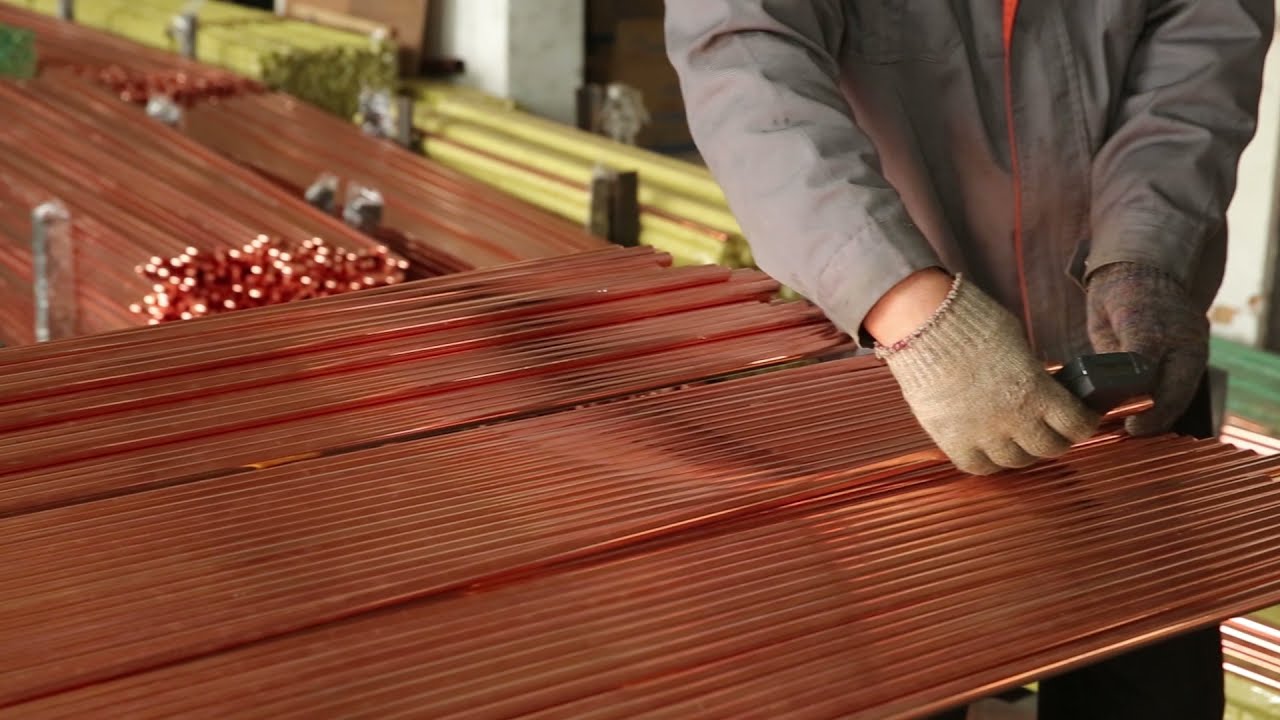
Показать описание
Copper-clad steel grounding materials are roughly divided into two categories: grounding poles (rods), grounding wires, and grounding clamps, and copper-clad grounding materials are called in many ways, such as copper-clad steel, copper plating, copper-clad steel, etc., In fact, this represents the three main processes of copper-clad steel ground rods and ground wires. Let us compare the differences between these three processes.
1. Electroplating process (also known as copper plating):
Advantages: lower one-time purchase cost
Disadvantages: The cold plating process was originally used for cyanide plating. Because the cyanide is toxic, the environmental assessment is also unacceptable; now more nickel and copper plating processes are used, otherwise, the same steel will not be plated without affinity. This process results in:
(1) The copper layer is relatively thin, generally ≤0.3mm;
(2) The residual electrolyte, after annealing and reduction, the copper layer on the surface will swell;
(3) A galvanic cell reaction will form, leading to electrochemical corrosion inside the copper-clad steel material;
(4) Great pollution to the environment.
2. Cold drawing process (also called casing coating process):
Advantages: simple process, copper layer thickness can be controlled, no pollution, low processing cost
Disadvantages:
(1) The bonding force is poor, and the copper layer is easy to peel;
(2) The presence of emulsifiers between copper and steel will cause electrochemical corrosion, which is easy to form a galvanic effect;
(3) Products that cannot be produced in large lengths (limited by the length of the outer copper sleeve).
3. Continuous casting process:
advantage:
(1) Achieve metallurgical bonding between copper and steel;
(2) The thickness of the copper layer is arbitrarily controlled, and there are many product varieties;
(3) Large length and large diameter copper can be realized;
(4) No pollution;
(5) No electrochemical corrosion and primary battery effect;
(6) Full life, maintenance free,
Disadvantages: The process is complex and the cost of processing is relatively high, but with the further improvement of the process, the processing cost is gradually decreasing.
Комментарии