filmov
tv
The HOLY GRAIL of Precision Machining | SIP Hydroptic 6 Jig Borer
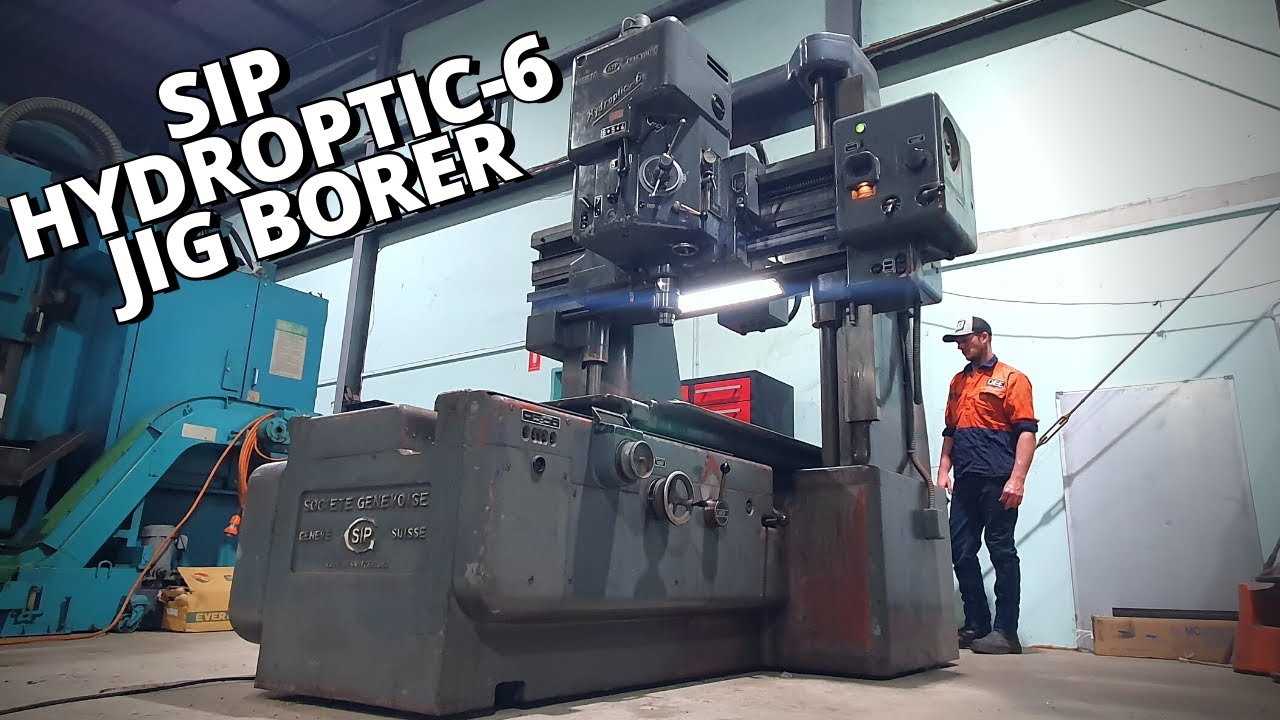
Показать описание
We are finally revealing our 1950s SIP Hydroptic-6 Jig Borer! The SIP Jig borers have a signature optical measuring system and hold tolerances up to 1 micron (0.001mm), so it's no wonder the Switzerland made machines are often considered the holy grail of precision machining. In today's era this vintage 1950s jig borer can even out perform machines of the modern world. In the video we share what a jig borer is, how it works and all the special tooling & accessories we received with it. We hope you enjoy this walk-around and tour of our amazing SIP Hydroptic-6 Jig Borer.
Join our channel:
To see more follow us on online here:
Check out our AMAZON store and explore our favourite finds that we use in the workshop:
About Us:
Our channel is all about showing you real life machining work from our workshop on the Gold Coast Australia. We specialize in manual machining, hydraulic repairs and heavy fabrication for the earth moving, mining and civil construction industries. So if you're a machinist that wants to see some big gear in action be sure to subscribe to our channel right now. We upload new videos every week that show lathe machining, milling, welding and all the good stuff that comes from a machining workshop. If that sounds like something that you would enjoy seeing, then make sure to join us by subscribing!
#australianmachinist #machineshop #machinist
Join our channel:
To see more follow us on online here:
Check out our AMAZON store and explore our favourite finds that we use in the workshop:
About Us:
Our channel is all about showing you real life machining work from our workshop on the Gold Coast Australia. We specialize in manual machining, hydraulic repairs and heavy fabrication for the earth moving, mining and civil construction industries. So if you're a machinist that wants to see some big gear in action be sure to subscribe to our channel right now. We upload new videos every week that show lathe machining, milling, welding and all the good stuff that comes from a machining workshop. If that sounds like something that you would enjoy seeing, then make sure to join us by subscribing!
#australianmachinist #machineshop #machinist
Комментарии