filmov
tv
How to keep your oil pan and timing cover gaskets from leaking. Always do this trick.
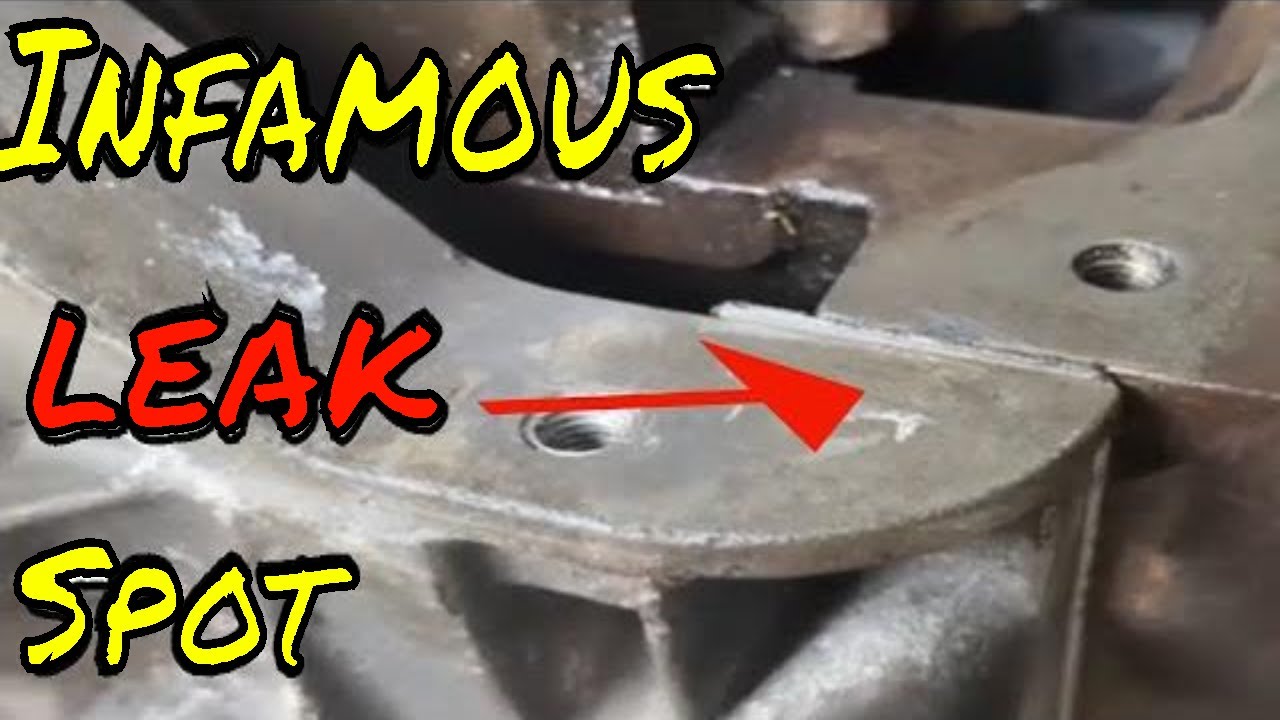
Показать описание
After working on a lot of engines I want to bring some tips t my veiwers. This is extremely important because not following these tips will have your gaskets leak.
Thank you for visiting my channel, Disturbing Kreationz Auto. If you have any questions please leave them below in the comment section and someone will get back to you promptly.
Links for the email and other channels are listed at the bottom of the description.
I want to thank everyone in advance for all the love and support by hitting the LIKE, SUBSCRIBE, and SHARE because it helps the channel which means I can make better content for you.
If you have a video suggestion or some helpful advice put it in the comment section or you can email me directly using the Email link below.
Thanks for the visit and support. God bless all of you and have a great day.
If you are local and want to make an appointment use the link for the Facebook (Meta) Business Page. Special videos will now be published for our members of this Youtube channel.
Disturbing Kreationz Auto:
Disturbing Kreationz Construction:
Disturbing Kreationz Business:
Thank you for visiting my channel, Disturbing Kreationz Auto. If you have any questions please leave them below in the comment section and someone will get back to you promptly.
Links for the email and other channels are listed at the bottom of the description.
I want to thank everyone in advance for all the love and support by hitting the LIKE, SUBSCRIBE, and SHARE because it helps the channel which means I can make better content for you.
If you have a video suggestion or some helpful advice put it in the comment section or you can email me directly using the Email link below.
Thanks for the visit and support. God bless all of you and have a great day.
If you are local and want to make an appointment use the link for the Facebook (Meta) Business Page. Special videos will now be published for our members of this Youtube channel.
Disturbing Kreationz Auto:
Disturbing Kreationz Construction:
Disturbing Kreationz Business:
A Simple Trick To Keep Your Oil From Bubbling Over When Frying Pastries
How to Quickly Filter and Store Fryer Oil After Deep Frying to Save and Reuse
100% This Trick will keep your hands clean while changing oil
Butter vs. Oil: Which One Is The Better Choice to Keep Your Eggs from Sticking? 🥚🍳
Keep your Machinery safe By Using Oil15W-40/CK Oil
DIRTY ENGINE OIL, HOW TO KEEP YOUR ENGINE HEALTHY AND AVOID ENGINE SLUDGE BUILD UP
Pours In Gold, Drains Out Black? Engine Oil Basics To Keep Your Car Healthy
Store Cooking Oil Properly for Maximum Longevity | Problem Solved
STOP Hair Fall & Regrow Hair FAST! (Doctor Approved)
How to Keep Your Car Engine Efficient: Importance of Regular Oil Changes.
How to Keep Your Oil Paint and Brushes From Drying Out
DIY Skincare Oil: A Super Easy Way To Keep Your Skin Glowing Every Day | Skincare Routine
Preventing Oil Buildup: How Valve Seals Keep Your Engine Running Smoothly
Keep These Oils OUT of Your Kitchen Pantry! | Cooking Oil Tier List
How to store your oil paints so they don’t dry out
How to keep your oil PAN gasket? In place trick. #337 #mechanicslife #automobile
How To Keep Your Porsche Engine Running Right: Oils, Fuel, and Oil Analysis | Tech Tactics Live
How I grow my hair and keep my scalp moisturized- Batana oil! #batanaoil #hairgrowth #naturalhair
Quick tip on a simple way to keep your engine oil temperature warm during cold weather conditions.
How long Should You Keep Oil in your Hair✅ #shortsindia #haircare #hairoil
Keep Your Arteries Clean With Olive Oil | Dr. Mandell
Ran Out Of Heating Oil? Don’t just keep hitting the reset! #diy #handyman #hvac #plumbing #heater
How to Use Castor Oil to Keep Your Eyes Moist
How to use olive oil to keep your ears clean
Комментарии