filmov
tv
Using the Wrong Tool to Balance a Grinding Wheel
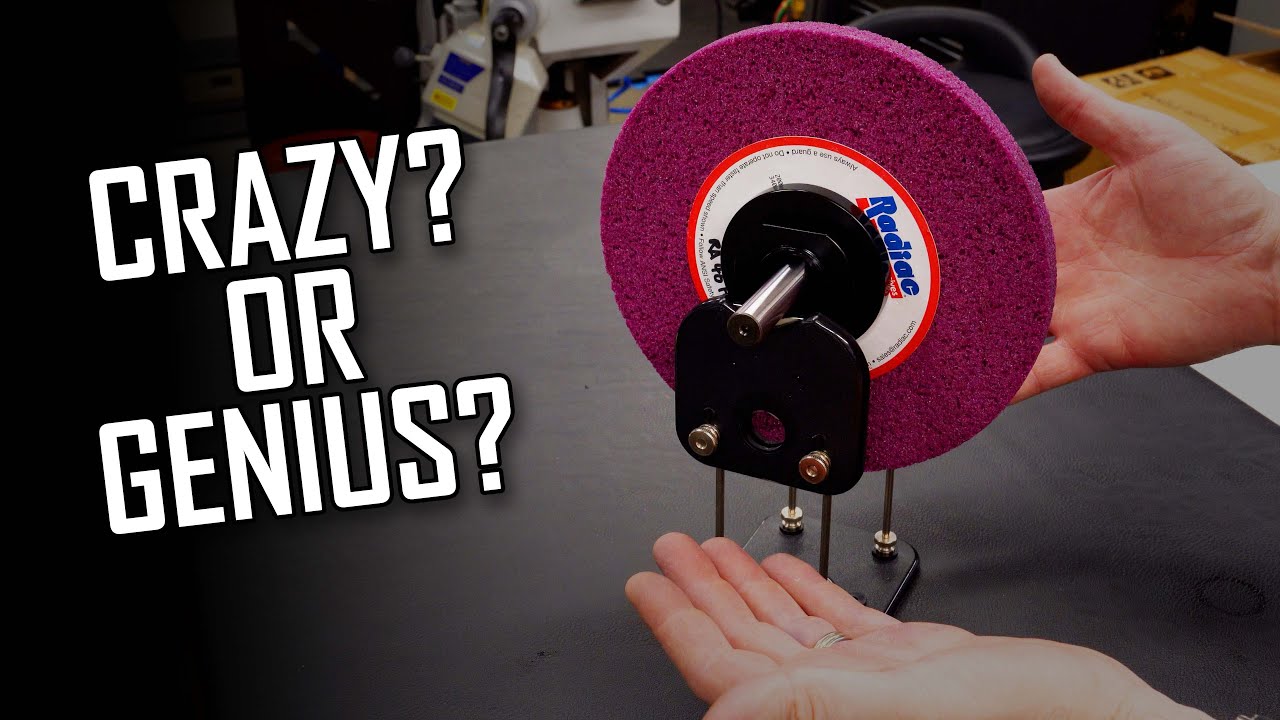
Показать описание
Today we're balancing a wheel for the surface grinder using an RC prop balancer. It's definitely the wrong tool for the job, but it might work anyway.
Tools used in this video:
*This site contains affiliate links for which I may be compensated
Licensed under Creative Commons: By Attribution 3.0 License
00:00 Intro
00:50 Balancing hardware
04:38 Shopping for balancers
07:52 Prop balancer as a design pattern
12:10 Or maybe the prop balancer will work?
15:47 Test grind!
20:27 Inspecting the result
21:48 Wrap
Using the Wrong Tool to Balance a Grinding Wheel
How to Know if You're Using the Wrong Tool
Using the Wrong Tool for the Job?
You've Been Using The Wrong Tool To Flip Eggs, Try This Instead (& Other Egg Mistakes To St...
Have You Been Using The Wrong Tool The Whole Time? RBRT Guy Explains The Difference, And A Solution!
Get BANNED for Using the WRONG TOOL?! #Shorts
UNBELIEVABLY WRONG TOOL USE #shorts #youtubeshorts #autorepair
This guy has no clue! Farming basics with the wrong tool again!
Woodworking Fail / Using the Wrong Tool for the Job #SHORTS
When you use a wrong tool to cut the grass
You’re Using The Wrong Tool!!! #dewalttough #impactdriver #impactwrench #hammerdrill
Using the wrong tool on Minecraft. #minecraft #minecraftshorts #gaming
Wrong tool for job
Using the wrong tool or a faulty one can lead to accidents.
The wrong tool: Using modular synths to create D&D characters
You've Been Using Your Angle Grinder Wrong All Along!
Using the wrong tool to dehusk a coconut
Stop Using the Wrong Tool! Dennis Gage Garage Segment with Dustless Blasting
How To Get Slow Results?(Using The wrong tool)
You're Using the Wrong Tool! Milwaukee vs Flex #milwaukee #flextools #impactvsdrill #howto #diy...
STOP Using the Wrong Tool for 3D Art and Try Palette Knife Instead! #art #acrylicpainting
Using The Wrong Tool
Stop using the wrong tool to cut and strip Copper Wire and start using the PA1123 from Paladin
Tool Tip: The wrong and right way to use a nail gun.
Комментарии