filmov
tv
Ansys Fluent Meshing using Watertight Geometry Guided Workflow | Ansys Virtual Academy
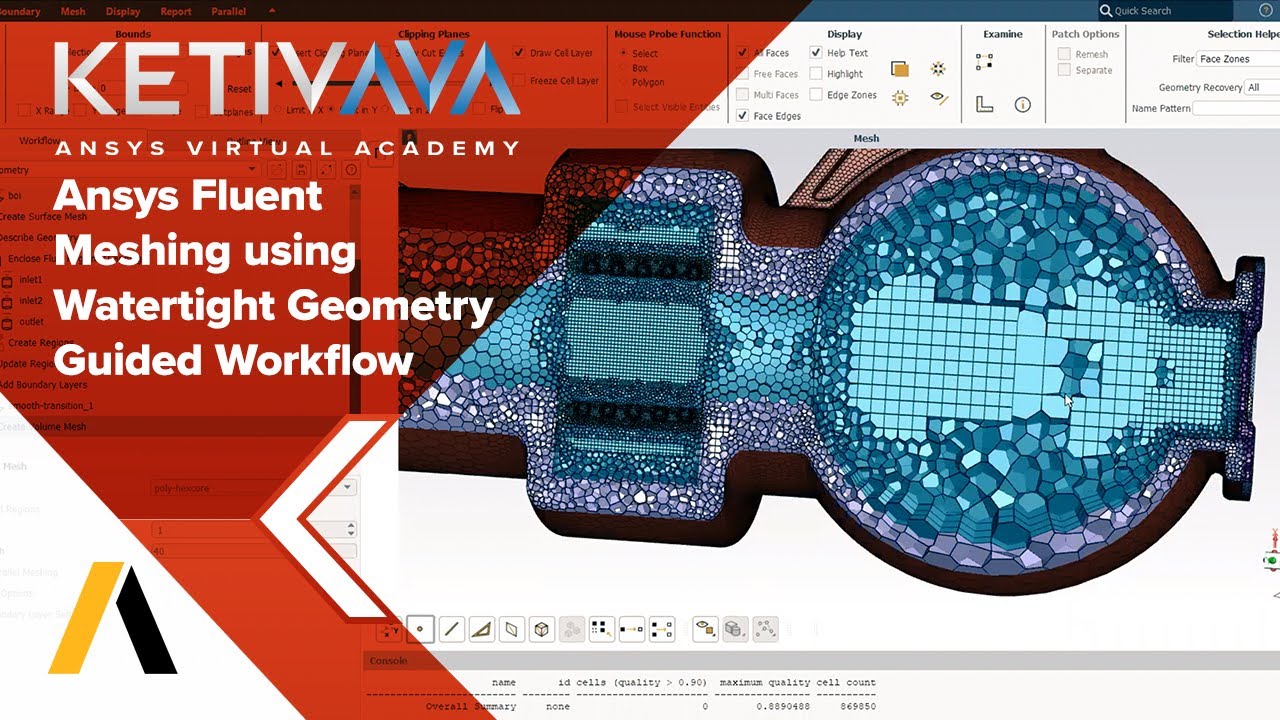
Показать описание
In this session, join KETIV Application Engineer, Snigdha Sarkar as she goes over the guided meshing workflow for Watertight Geometry with clean CAD in Ansys Fluent Meshing. This session follows the easy and intuitive steps in the guided workflow to auto-generate a high quality CFD mesh in Fluent meshing. Some of the important steps that are covered include:
-Introduction to the watertight geometry workflow GUI and features
-Surface meshing using guided workflow
-Volume meshing using guided workflow
This session is highly recommended for CFD analysts who are looking to reduce their simulation pre-processing time, and simplify their CFD workflow by taking advantage of Fluent’s single window workflow from geometry import to meshing, solving and post-processing.
Follow us:
#KETIV #AnsysVirtualAcademy #Ansys
Ansys Fluent Meshing using Watertight Geometry Guided Workflow | Ansys Virtual Academy
How to Mesh with Watertight Geometry Workflow – User Interface – Ansys Fluent Meshing
An introduction to Fluent Meshing - Watertight Geometry WorkFlow - ANSYS 2020 R1
How to Use BOIs and FOIs – Add Local Sizing – Ansys Fluent Meshing Watertight Geometry Workflow
Swept Mesh Using MultiZone Controls in Ansys Fluent Meshing
Mesh Generation using Ansys Fluent Watertight Workflow — Course Overview
Using ANSYS Fluent Meshing for CFD Simulation
How to Use Global and Local Size Functions in Ansys Fluent Meshing’s Watertight Geometry Workflow
Fluent Meshing (Mosaic Meshing) Course (#14: Refine ready mesh file with adding Body of Influence)
How to Improve Surface Mesh Quality in Ansys Fluent Meshing’s Watertight Geometry Workflow
High-speed Train Tutorial Using Ansys Fluent Meshing Watertight Geometry Workflow
How to Improve the Volume Mesh in Ansys Fluent Meshing’s Watertight Geometry Workflow
Turbine Blade Cooling Tutorial Using Ansys Fluent Meshing Watertight Geometry Workflow
Mixing Tank Tutorial Using Ansys Fluent Meshing Watertight Geometry Workflow
How to Use Fill With Methods in Ansys Fluent Watertight Workflow, Part 1: Tetrahedral and Polyhedra
Methods used for Boundary Layer Mesh Generation in Ansys Fluent Meshing Watertight Geometry Workflow
ANSYS Fluent: Watertight Geometry Meshing Workflow
Tutorial - Mesh Generation using Ansys Fluent Watertight Workflow — Lesson 7
How to Use Edge, Face, and Body Local Sizing Controls – Add Local Sizing – Ansys Fluent Meshing
Intro to Describe Geometry Task in Ansys Fluent Meshing Watertight Geometry Workflow – Lesson 1
Complete course on ANSYS Fluent Meshing 2024 R2 (Watertight Workflow)
How to Perform Share Topology in Ansys Fluent, Part 1: Join-Intersect Method – Lesson 4
Battery Module Tutorial Using Ansys Fluent Meshing Watertight Geometry Workflow
How to Calculate Lift and Drag in ANSYS Fluent Tutorial I Flow Analysis | Fluent with Fluent Meshing
Комментарии