filmov
tv
Micronics SLS nylon 3D printer makes electronic circuits
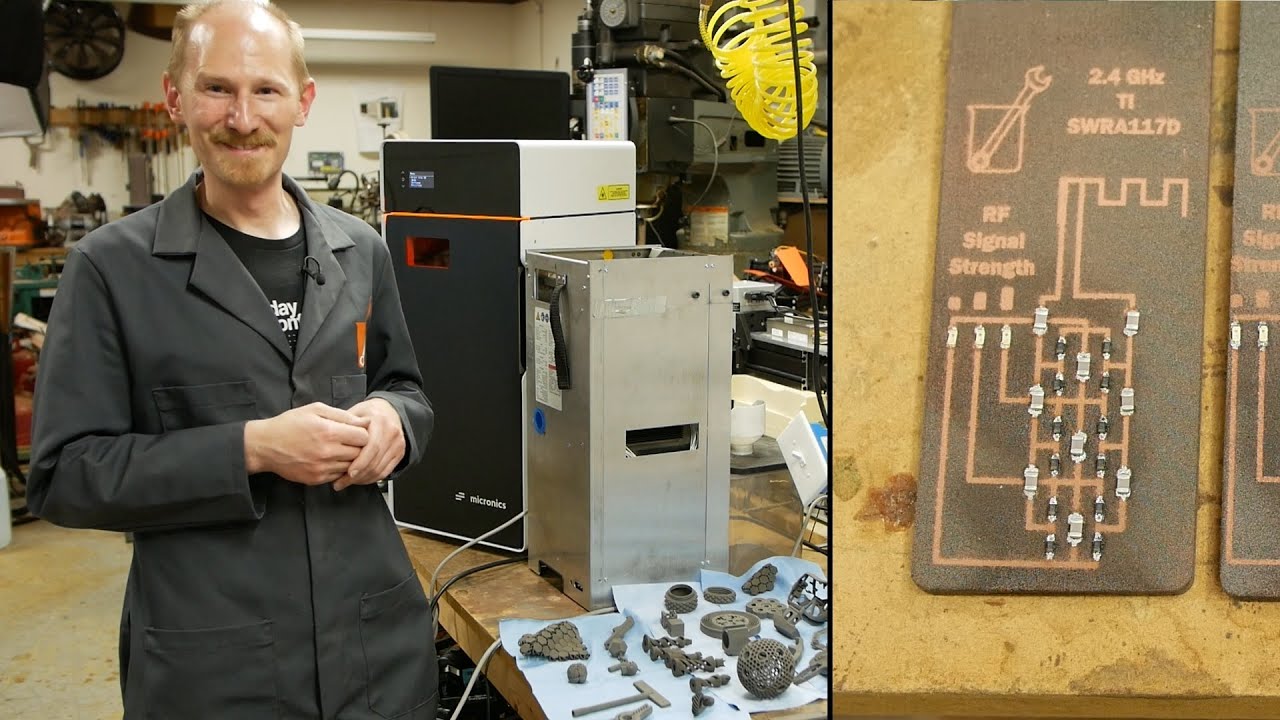
Показать описание
Favorite copper plating bath recipe:
Heat 250ml deionized water to 60*C in a 300ml beaker, stirring at 350 RPM
Add 2.5g CuSO4*5H2O, wait until dissolved
Add 4.6g EDTA disodium dihydrate, wait until dissolved
Add 0.84ml of 1% Triton-X 100 solution in water
Dissolve 5.8g NaOH in 30ml DI water, stir until clear, then add to bath
Add 4ml Formaldehyde (37% HCHO)
Lower stirring to 100 RPM and begin filtration with 0.5 micron syringe filter and peristaltic pump. No intentional oxygenation or bubbling. Filter return is below surface for minimal splashing.
I experimented a little with PEG and 2 2' Bipyridine, but didn't find them impactful enough to discuss in this video.
LED rectenna designs:
Electroless copper references:
Copper chromite catalyst:
Open Sauce 2024:
Support Applied Science on Patreon:
NOW WHAT?! Micronics Micron SLS 3D Printer
We've Never Unboxed a 3D Printer Like THIS before! - Micronics SLS 3D Printer
Micronics SLS nylon 3D printer makes electronic circuits
SLS Powders Explained
Affordable SLS 3D Printing! Is Micronics Machine for You?
SLS 3D Printing AT HOME?
3D Printing Comparison: Multi Jet Fusion vs Selective Laser Sintering Nylon | Fictiv
I wanted to love this revolutionary 3d printer - Micronics SLS Review
Formlabs and Micronics: A Shared Vision for the Future of SLS 3D Printing
How we BUILT a 3D printer that can print ANYTHING!
AQL-180 on our Fuse 1 SLS 3D printer
3D printing the world's longest SLS Chain! ⛓
Fuse Depowdering Kit: The Key to Affordable, Industrial SLS 3D Printing
Have you ever seen this 3D printing technology?! #3dprinting
Sinterit Lisa X vs Formlabs Fuse 1+: Best Sub-$30k SLS 3D Printers | Office SLS Comparison 2023
UNBOXING the Micron SLS 3D Printer & FIRST PRINT!
Powder 3D printing is pure Magic! ✨
Affordable Industrial SLS 3D Printer?! // Formlabs Fuse 1 Honest Review
SLS vs. FDM - Which technology wins? | Test of a Hyperbolic planetary gearset
sls printed electronic tool
Meet the ALLshape Base1 SLS 3D printer
Did I Buy a $1,000,000 3D Printer?!
EXTREMTEST!!! 3D-Drucker 'Formlabs Fuse1' am LIMIT | Das ist mit 'SLS Pulverdruck&apo...
CARCASA A COLOR impresa en Nylon PA 12 en tecnología SLS FUSE 1+ de Formlabs #Shorts #Impresión3D
Комментарии