filmov
tv
DIY Engine Adapter Plate (Mate any Engine to any Transmission)
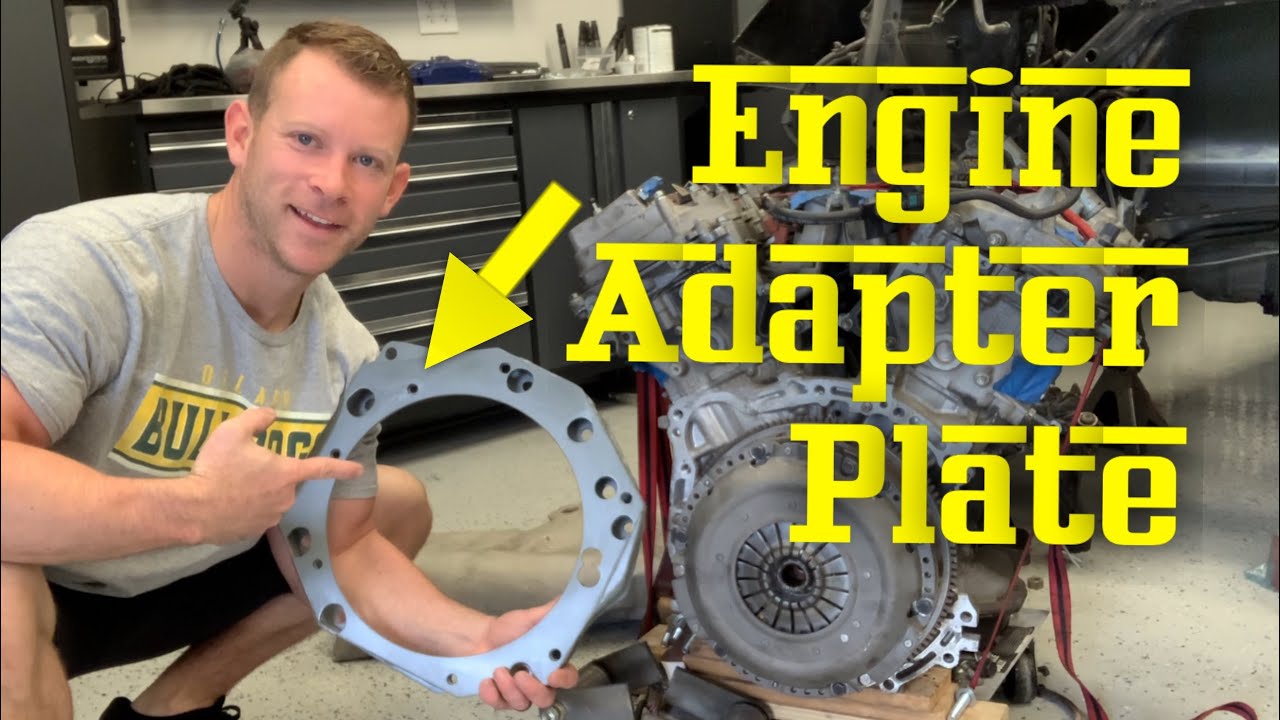
Показать описание
This was a huge project and something I have always wanted to try. In dreaming of swapping bigger engines into a vehicle, you are always limited to engine and transmission compatibility. But not now! This opens the door for so many other engine swap options. I am already re-thinking my LS swapped MR2 for the Toyota 1muz v8 which would have been less blasphemous. Either way, this shows if you can put some time into it, you can do this at the DIY level.
Please let me know what you think and leave a LIKE if this vid helped you out at all. Please comment below with any questions you may have.
Follow me on Facebook and Instagram for more updates
Instagram : Scantrons_Garage
Facebook: Turk Turkleton (not my real name obviously)
––––––––––––––––––––––––––––––
Track: Freedom — tubebackr [Audio Library Release]
Music provided by Audio Library Plus
–––––––––––––––––––––––––––––
––––––––––––––––––––––––––––––
Track: Feel — Land of Fire [Audio Library Release]
Music provided by Audio Library Plus
––––––––––––––––––––––––––––––
––––––––––––––––––––––––––––––
Creative Commons — Attribution-ShareAlike 3.0 Unported — CC BY-SA 3.0
––––––––––––––––––––––––––––––#engine #transmission #streetcar #fabrication #metalfabrication
Please let me know what you think and leave a LIKE if this vid helped you out at all. Please comment below with any questions you may have.
Follow me on Facebook and Instagram for more updates
Instagram : Scantrons_Garage
Facebook: Turk Turkleton (not my real name obviously)
––––––––––––––––––––––––––––––
Track: Freedom — tubebackr [Audio Library Release]
Music provided by Audio Library Plus
–––––––––––––––––––––––––––––
––––––––––––––––––––––––––––––
Track: Feel — Land of Fire [Audio Library Release]
Music provided by Audio Library Plus
––––––––––––––––––––––––––––––
––––––––––––––––––––––––––––––
Creative Commons — Attribution-ShareAlike 3.0 Unported — CC BY-SA 3.0
––––––––––––––––––––––––––––––#engine #transmission #streetcar #fabrication #metalfabrication
Комментарии