filmov
tv
Customizing Waterproof Wire Connectors for Motor Applications: A Comprehensive Guide #connector
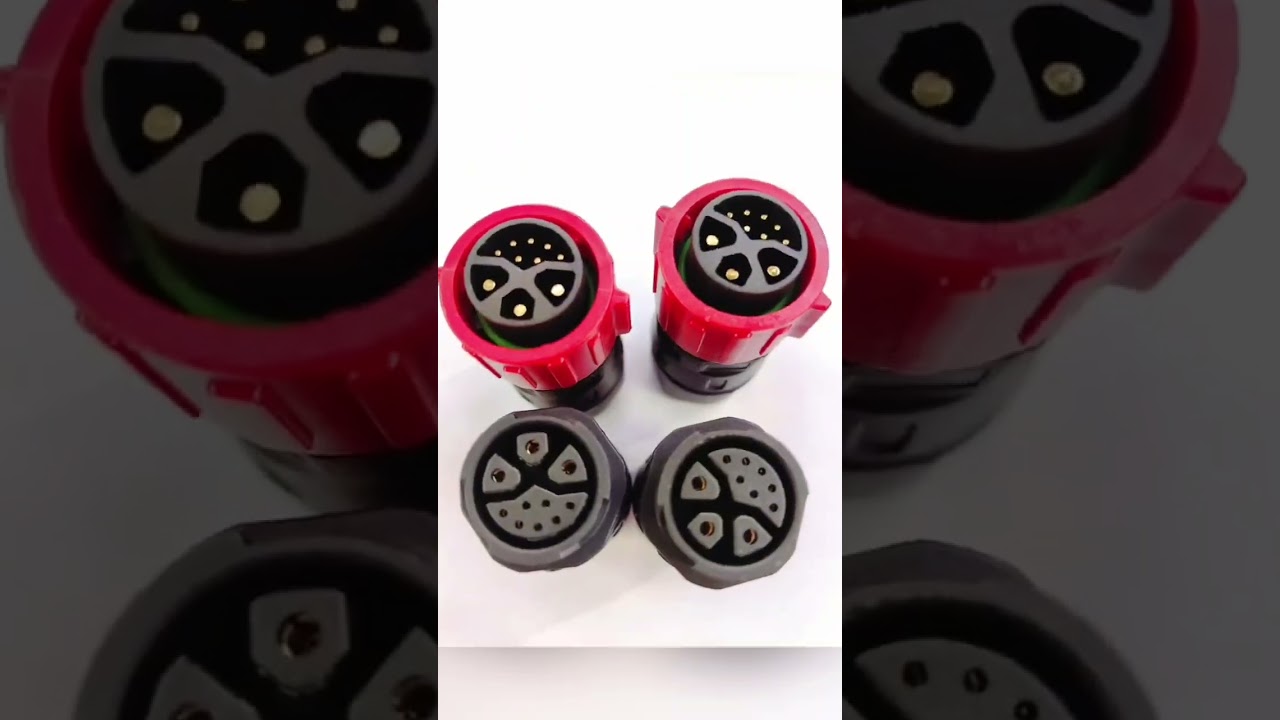
Показать описание
Waterproof wire connectors are essential components in numerous industries where the reliable and safe transmission of electrical power is crucial. One such application is in motors, where the protection of electrical connections from moisture and environmental factors is critical for efficient and uninterrupted operation. In this article, we will explore the importance of waterproof wire connectors for motors and discuss the customization options available for 3+7pin waterproof connectors.
Importance of Waterproof Wire Connectors for Motors:
Motors are commonly used in various environments, including industrial, automotive, marine, and outdoor settings. These environments can expose motors to moisture, dirt, dust, and other contaminants that can potentially compromise their performance and lifespan. By utilizing waterproof wire connectors, the electrical connections within the motor can be effectively protected, ensuring a reliable and durable power supply. Waterproof connectors for motors offer excellent sealing performance, resistance to vibration and shock, and corrosion resistance, making them ideal for demanding applications.
Customization Options for 3+7pin Waterproof Connectors:
Pin Configuration:
The 3+7pin configuration refers to three power pins and seven signal pins. Depending on the specific motor application, the pin configuration can be tailored to meet the requirements. The number of power and signal pins can be adjusted, allowing for a customized solution that matches the motor's electrical needs.
Connector Material:
Choosing the appropriate connector material is essential for achieving superior waterproofing and durability. Common materials used for waterproof connectors include thermoplastic, thermoset, and metal. Each material has its unique properties, such as temperature resistance, chemical resistance, and mechanical strength. By selecting the most suitable material, the connector can withstand the environmental conditions it will be exposed to.
Sealing Methods:
Waterproof connectors employ various sealing methods to prevent moisture ingress. These can include interfacial seals, gaskets, O-rings, or a combination of these. Customization allows for the selection of the most effective sealing method based on the specific conditions the motor will be operating in.
Cable Harness:
To ensure a secure and reliable connection, the waterproof wire connector must be compatible with the motor's cables. Customization allows for the selection of cable types, lengths, and wire gauges. Depending on the application, the cables can be armored, shielded, or reinforced for added protection against external factors.
Benefits of Customizing Waterproof Wire Connectors:
Enhanced Reliability: Customized waterproof wire connectors are designed to meet the specific needs and requirements of the motor application. This customization ensures a reliable and uninterrupted power supply, reducing the risk of electrical failures and costly downtime.
Improved Safety: With a properly customized waterproof wire connector, the risk of electrical hazards due to moisture or contamination is significantly reduced. This enhances the overall safety of the motor and the surrounding environment.
Optimal Performance: Customization allows for the selection of materials and designs that optimize the performance of the waterproof wire connector, minimizing electrical losses and maximizing efficiency.
Versatility: Customized waterproof wire connectors can be designed to fit various motor sizes and types, including different voltages and current ratings. This versatility ensures that the connector can be used across a range of applications.
Conclusion:
Customizing waterproof wire connectors for motor applications is paramount for ensuring a safe, reliable, and efficient power supply. The ability to tailor connector configurations, materials, sealing methods, and cable harnesses provides an optimal solution that meets the specific needs of each motor application. By investing in customized waterproof wire connectors, you can effectively safeguard your motors from moisture and environmental factors, extending their and minimizing maintenance costs.
Importance of Waterproof Wire Connectors for Motors:
Motors are commonly used in various environments, including industrial, automotive, marine, and outdoor settings. These environments can expose motors to moisture, dirt, dust, and other contaminants that can potentially compromise their performance and lifespan. By utilizing waterproof wire connectors, the electrical connections within the motor can be effectively protected, ensuring a reliable and durable power supply. Waterproof connectors for motors offer excellent sealing performance, resistance to vibration and shock, and corrosion resistance, making them ideal for demanding applications.
Customization Options for 3+7pin Waterproof Connectors:
Pin Configuration:
The 3+7pin configuration refers to three power pins and seven signal pins. Depending on the specific motor application, the pin configuration can be tailored to meet the requirements. The number of power and signal pins can be adjusted, allowing for a customized solution that matches the motor's electrical needs.
Connector Material:
Choosing the appropriate connector material is essential for achieving superior waterproofing and durability. Common materials used for waterproof connectors include thermoplastic, thermoset, and metal. Each material has its unique properties, such as temperature resistance, chemical resistance, and mechanical strength. By selecting the most suitable material, the connector can withstand the environmental conditions it will be exposed to.
Sealing Methods:
Waterproof connectors employ various sealing methods to prevent moisture ingress. These can include interfacial seals, gaskets, O-rings, or a combination of these. Customization allows for the selection of the most effective sealing method based on the specific conditions the motor will be operating in.
Cable Harness:
To ensure a secure and reliable connection, the waterproof wire connector must be compatible with the motor's cables. Customization allows for the selection of cable types, lengths, and wire gauges. Depending on the application, the cables can be armored, shielded, or reinforced for added protection against external factors.
Benefits of Customizing Waterproof Wire Connectors:
Enhanced Reliability: Customized waterproof wire connectors are designed to meet the specific needs and requirements of the motor application. This customization ensures a reliable and uninterrupted power supply, reducing the risk of electrical failures and costly downtime.
Improved Safety: With a properly customized waterproof wire connector, the risk of electrical hazards due to moisture or contamination is significantly reduced. This enhances the overall safety of the motor and the surrounding environment.
Optimal Performance: Customization allows for the selection of materials and designs that optimize the performance of the waterproof wire connector, minimizing electrical losses and maximizing efficiency.
Versatility: Customized waterproof wire connectors can be designed to fit various motor sizes and types, including different voltages and current ratings. This versatility ensures that the connector can be used across a range of applications.
Conclusion:
Customizing waterproof wire connectors for motor applications is paramount for ensuring a safe, reliable, and efficient power supply. The ability to tailor connector configurations, materials, sealing methods, and cable harnesses provides an optimal solution that meets the specific needs of each motor application. By investing in customized waterproof wire connectors, you can effectively safeguard your motors from moisture and environmental factors, extending their and minimizing maintenance costs.