filmov
tv
Intake Manifold CFD Modeling for Power - Plenum and Inlet Radius Design
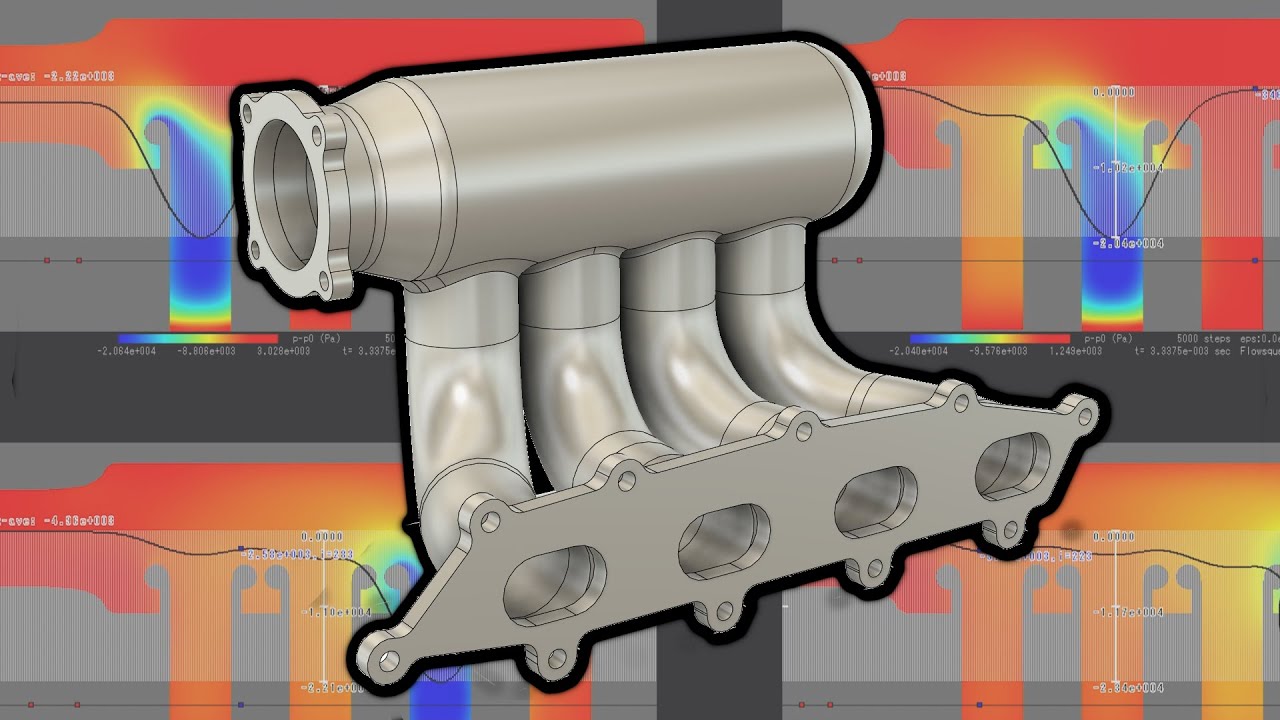
Показать описание
I want to thank Yuki Minamoto for developing the excellent, easy to use, software: FlowSquare
I’m glad to hear any thoughts or criticisms. So please comment below. Also, if you have any ideas for CFD tests you’d like to see, comment that too!
I’m glad to hear any thoughts or criticisms. So please comment below. Also, if you have any ideas for CFD tests you’d like to see, comment that too!
Intake Manifold CFD Modeling for Power - Plenum and Inlet Radius Design
CFD Simulation of Engine Inlet Manifold
Inlet Manifold Modeling (Watch updated video!)
Das Beast E30 turbo intake manifold high res flow simulation
CFD Simulation of Engine Inlet Manifold with Perforated Plates
Dual plenum 2-side final model CFD
Manifold CFD Analysis Visualization
CFD of Formula SAE Air Intake Manifold using Solidworks (Part 1) | FSAE | DP DESIGN
CFD analysis of Engine intake manifold
Fluid Flow Analysis through Air Manifold Inlet
Flow simulation soldwork | intake manifold
Intake Manifold CFD Simulation by ANSYS
Intake Manifold Flow Simulation
C.F.D. análysis of a lima engine intake manifold
Transient Flow Development Inside Intake Manifold
3D CFD simulation of engine intake system - Velociy contour at 8000 rpm
SolidWorks Education SAE Intake Internal Flow
Why we do CFD test for all the intake manifold that we design?
CFD analysis of flow in exhaust manifold
CFD analysis in Inlet manifold by using Acusolve
CFD Analysis using solidworks for air manifolds
Intake Manifold Explained
FSAE-IITM Intake Manifold Preliminary Flow Analysis
Exhaust Port CFD Analysis
Комментарии