filmov
tv
DIY Brass Branding Iron - CNC Project #74
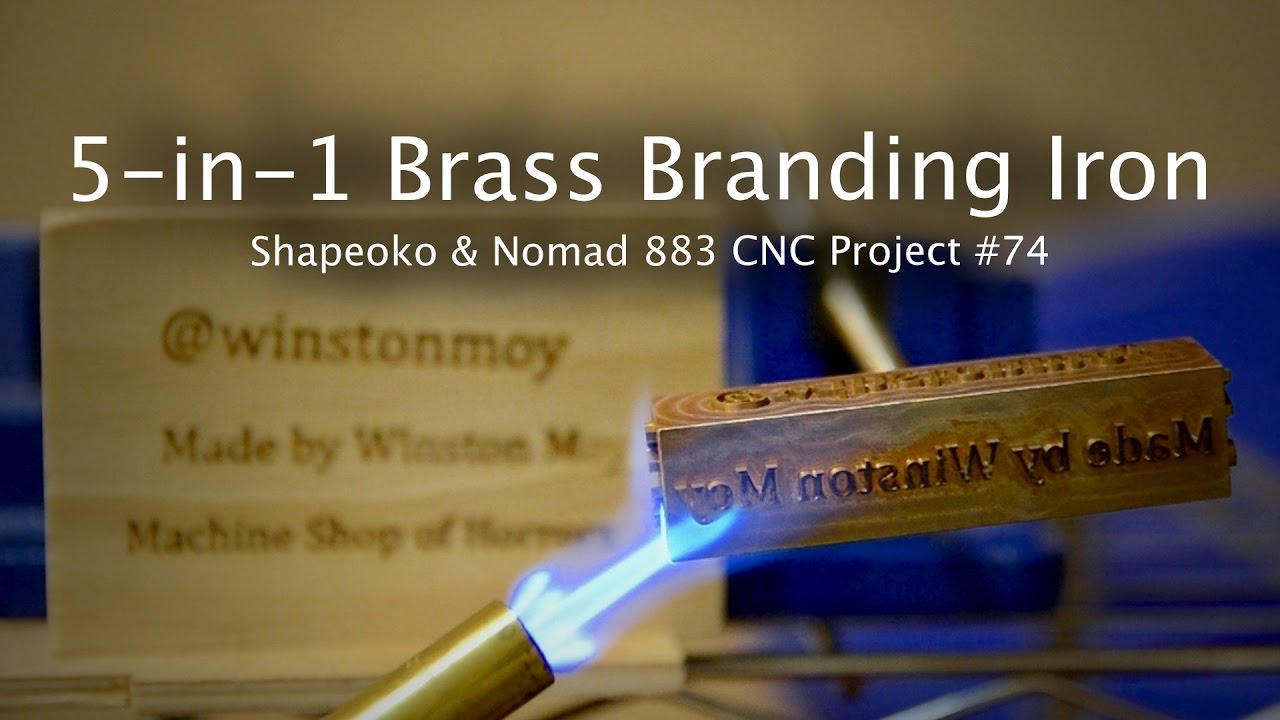
Показать описание
I made a 5-in-1 branding iron out of 360 brass to personalize my future projects with. Designed with Fusion360, machined on my Shapeoko and Nomad Pro CNC's using uncoated carbide endmills.
Endmills Used:
Endmills Used:
Custom Electric 300 watt Brass Branding Iron - Made in Canada #woodworking
DIY Brass Branding Iron - CNC Project #74
EP. 25 Onefinity CNC - Make Your Own Brass Branding Iron!
Making a Custom Brass Branding Iron
How to Make a Branding Iron For Woodworking
Branding with an actual Iron! Easiest Solution!
Branding Iron With Brass Casting
Making a Branding Iron from a Brass Fitting
DIY, Branding Iron and what I learned.
Which Branding Iron is Better? 🔥Fire-heated🔥 vs ⚡Electric Branding Irons⚡
How to Make a Branding Iron
CNC Custom Brass Brand & Embossing Stamp
DIY CNC ATC - Branding iron out of Brass
Make a Wax seal / Leather Branding Iron Out Of Brass Plumbing Fittings
How to make: Branding Iron
DIY Aluminum Branding Iron
Making a Wood & Leather Branding Iron
(S-1 Ep-16) Make a Branding Iron With Your Logo
DiResta: Making a Wood & Leather Branding Iron
DIY Woodworking brand for initials from sheet brass
DIY CNC brass branding iron #shorts#cnc #machining #cncmachining
How to mark your work - 4 DIY branding techniques!
Brass Branding Iron
4 Branding Iron Tips
Комментарии