filmov
tv
What is a CAPA?
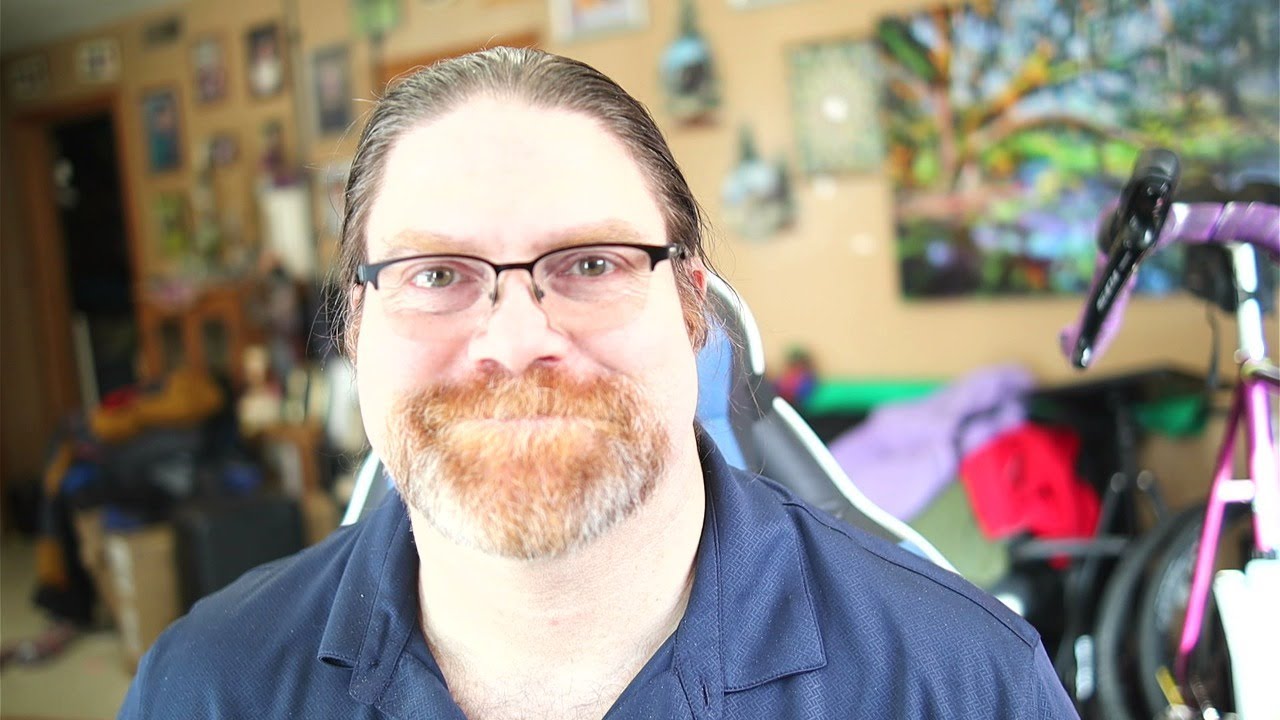
Показать описание
"CAPA" is the acronym for corrective action and preventive action. It's a systematic process for identifying the root cause of a quality problems, identifying actions for containment, correction, and corrective action. In the special case of preventive actions, the actions taken prevent quality problems from ever happening, while the corrective actions prevent quality problems from happening again. A CAPA procedure is required by the US FDA, and it is the most common reason for FDA 483 inspection observations and warning letters.
You can purchase Medical Device Academy's procedure on the following webpage:
When I teach courses on the CAPA process, 100% of the people can tell me what the acronym CAPA stands for. If everyone understands what a CAPA is, why is the CAPA process the most common source of FDA 483 inspection observations and auditor nonconformities?
When an FDA inspector reviews your CAPA process, the inspector uses a four-step process starting with your procedure. Then the inspector requests your CAPA log. Next, the inspector samples CAPA records, and finally, the inspector will request training records. Most of the 483 inspection observations identify one of the following seven problems:
➤ the procedure is inadequate
➤ records are incomplete
➤ actions planned did not include corrections
➤ actions planned did not include corrective actions
➤ actions planned were not taken or delayed
➤ training is inadequate
➤ actions taken were not effective
Auditors using the process approach request documents beyond the four items that the FDA inspectors review:
➤ inputs to the CAPA process
➤ computer resources used to manage the CAPA process
➤ the effectiveness of training and competency
➤ metrics for the CAPA process
Even though auditors use a more comprehensive process for evaluating the CAPA process, the same seven nonconformities are identified by auditors and inspectors.
If we know exactly what auditors and inspectors will look at, why do so many companies have problems with CAPAs?
People assigned to CAPAs need better training.
If you are interested in other training from Medical Device Academy, we have a few free training videos on our YouTube Video:
You can purchase Medical Device Academy's procedure on the following webpage:
When I teach courses on the CAPA process, 100% of the people can tell me what the acronym CAPA stands for. If everyone understands what a CAPA is, why is the CAPA process the most common source of FDA 483 inspection observations and auditor nonconformities?
When an FDA inspector reviews your CAPA process, the inspector uses a four-step process starting with your procedure. Then the inspector requests your CAPA log. Next, the inspector samples CAPA records, and finally, the inspector will request training records. Most of the 483 inspection observations identify one of the following seven problems:
➤ the procedure is inadequate
➤ records are incomplete
➤ actions planned did not include corrections
➤ actions planned did not include corrective actions
➤ actions planned were not taken or delayed
➤ training is inadequate
➤ actions taken were not effective
Auditors using the process approach request documents beyond the four items that the FDA inspectors review:
➤ inputs to the CAPA process
➤ computer resources used to manage the CAPA process
➤ the effectiveness of training and competency
➤ metrics for the CAPA process
Even though auditors use a more comprehensive process for evaluating the CAPA process, the same seven nonconformities are identified by auditors and inspectors.
If we know exactly what auditors and inspectors will look at, why do so many companies have problems with CAPAs?
People assigned to CAPAs need better training.
If you are interested in other training from Medical Device Academy, we have a few free training videos on our YouTube Video:
Комментарии