filmov
tv
Design Custom Electrical Enclosures for Mass Production 3D Printing
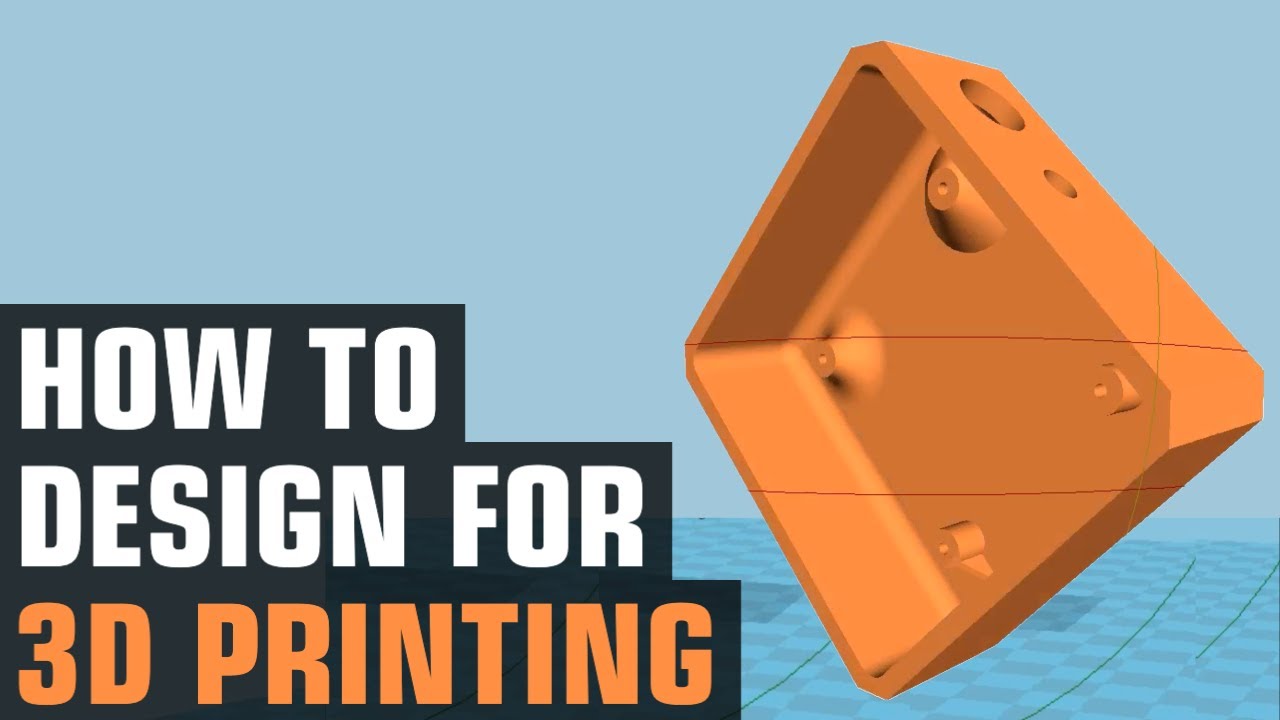
Показать описание
Discover how to design a custom 3D printed electrical enclosure in our latest Beginners Guide to Designing 3D Printed Parts for Mass Production 3D Printing. We cover the key features and design considerations for creating a 3D printable electronics enclosure that's both custom-fitted and ESD safe. Learn how to create standoffs, add chamfers, and optimize your design for print orientation to ensure a high-quality results and manufacturability. Plus, we share tips on incorporating ribs and custom insets for added support and durability.
Don't forget to LIKE the video and SUBSCRIBE to the Slant 3D YouTube channel for more mass production 3D printing tips!
#designtutorial #fusion360tutorial #3dprinting
Check out our 🔗 IMPORTANT LINKS 🔗
About Slant 3D
🏭 High-Volume 3D Printing: Scalability Meets Flexibility
Slant 3D's Large-Scale 3D Print Farms utilize 1000's of FDM 3D printers working 24/7 to offer limitless scalability and unparalleled flexibility. Whether it's 100 or 100,000 parts, our system can handle it reliably, while still allowing for real-time design updates, ensuring products evolve with the times. This adaptability is key in today's fast-paced world.
🌿 Sustainable Manufacturing: Eco-Friendly Efficiency
Embrace a system that drastically reduces carbon emissions by eliminating carbon-intensive steps in the supply chain, such as global shipping and warehousing. Our approach minimizes this footprint, offering a more sustainable manufacturing option.
⚙️ Digital Warehouses: Parts On-Demand
Think of print farms as a "Digital Warehouse", meaning we can store your parts digitally on a server rather than physically on a shelf. parts are available on-demand, reducing the need for extensive physical inventory.
Produced by Slant Media
*As an Amazon Associate, I earn commission from qualifying purchases.*
Don't forget to LIKE the video and SUBSCRIBE to the Slant 3D YouTube channel for more mass production 3D printing tips!
#designtutorial #fusion360tutorial #3dprinting
Check out our 🔗 IMPORTANT LINKS 🔗
About Slant 3D
🏭 High-Volume 3D Printing: Scalability Meets Flexibility
Slant 3D's Large-Scale 3D Print Farms utilize 1000's of FDM 3D printers working 24/7 to offer limitless scalability and unparalleled flexibility. Whether it's 100 or 100,000 parts, our system can handle it reliably, while still allowing for real-time design updates, ensuring products evolve with the times. This adaptability is key in today's fast-paced world.
🌿 Sustainable Manufacturing: Eco-Friendly Efficiency
Embrace a system that drastically reduces carbon emissions by eliminating carbon-intensive steps in the supply chain, such as global shipping and warehousing. Our approach minimizes this footprint, offering a more sustainable manufacturing option.
⚙️ Digital Warehouses: Parts On-Demand
Think of print farms as a "Digital Warehouse", meaning we can store your parts digitally on a server rather than physically on a shelf. parts are available on-demand, reducing the need for extensive physical inventory.
Produced by Slant Media
*As an Amazon Associate, I earn commission from qualifying purchases.*
Комментарии