filmov
tv
Easy To Remove Supports In Creality Print
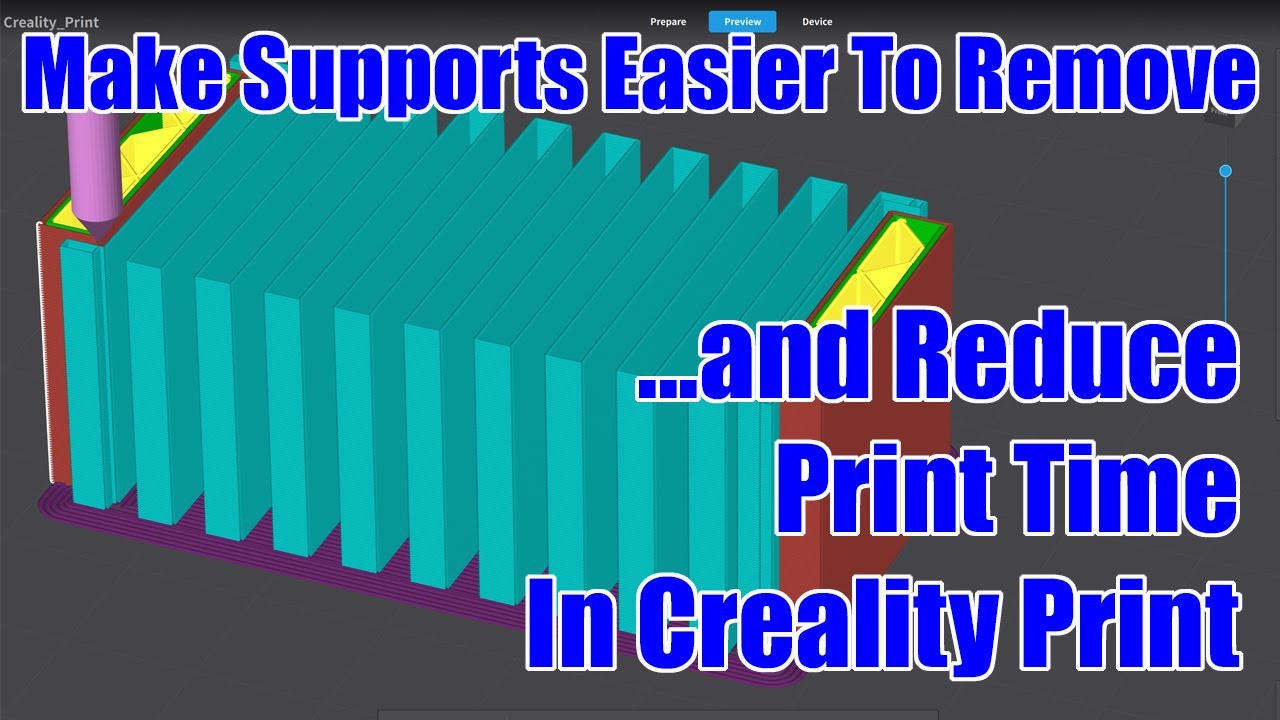
Показать описание
Easy To Remove Supports In Cura
Easy To Remove Supports For Your 3D Prints: Tips and Tricks
My Settings for EASY TO REMOVE Supports PLUS Tools I Use to Remove 3D Printed Supports
3d print supports removal (My simple process to remove supports)
Easy To Remove Supports In Creality Print
Prusaslicer remove supports EASY!!!!!#3dprinting #ender3s1 #ender3pro #ender5 #crealitycr10
Easy Method To Remove Supports on 3D Prints
3D Printed Supports Made Easy To Remove
Advanced Drawing App | LIVE JavaScript Coding | Part 8
Easy To Remove Simplify3D Generated Supports
[FDM friendly modeling] Make the supports easy to remove in blender.
easy to remove support in RAISE3d pro2 #3dprinting #raise3d
Easy to Remove Ultimaker Cura Support Settings 3DPrint Quality Layer Above Support
I need easy to remove supports like this every time! #3dprinting #shorts #3dprinter #youtubeshorts
BAMBU LAB SLICER | EASY TO REMOVE SUPPORT | ONE FILAMENT
Raise3D models and how easy it is to remove support
Learn how to get clean and easy to remove support for your 3D prints #shorts #3dprinting
Ramen Support- Easy to remove 3D Printed Supports
Cura support easy remove
from hard to remove supports to easy coming off supports with one Cura setting #Shorts
Best Support Easy to Remove - PLA CURA Settings - 3D print timelapse - Ep.28 [D4thDimension]
How to Remove supports from 3d printed miniatures. Simple tricks for FTM 3d printed miniatures
easy to remove supports (#2) - 3d printing #shorts
IEMAI 3D Easy Remove Support 3D Printing Materials For Carbon Fiber PA12
Комментарии