filmov
tv
We Created a Thread With a Thread Drill on Manual Lathe / watch full video and learn amazing process
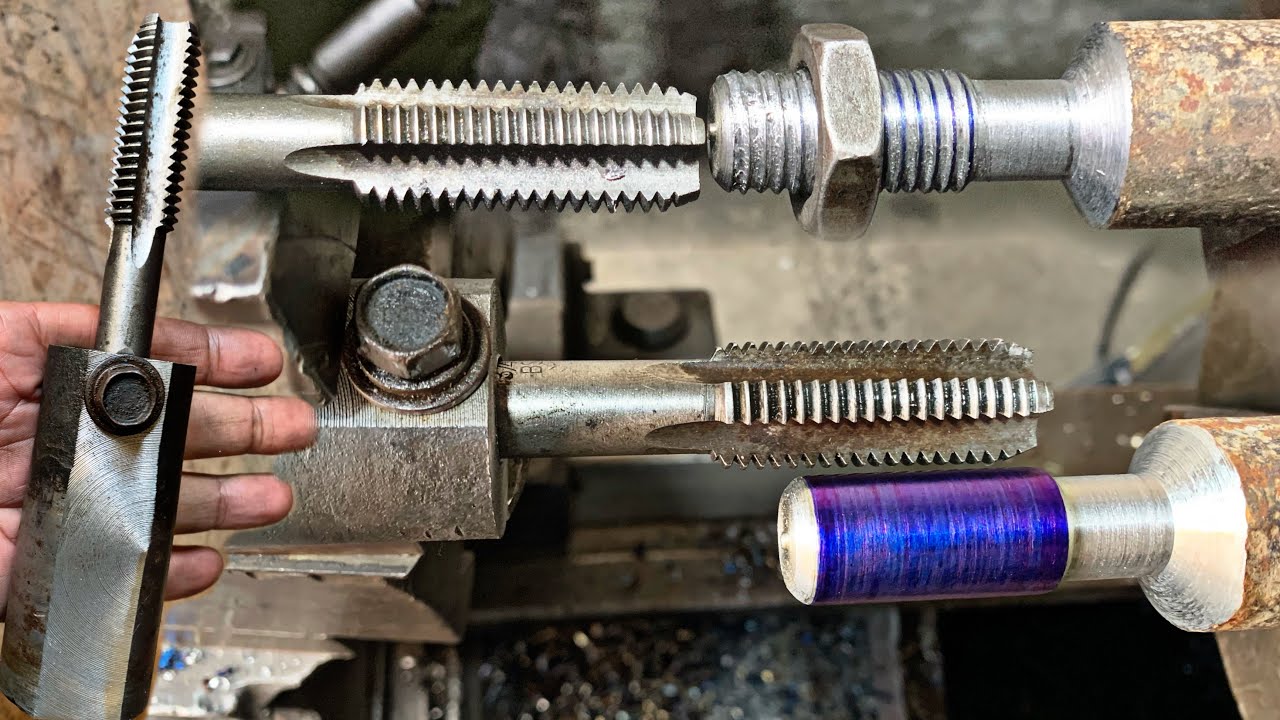
Показать описание
We Created a Thread With a Thread Drill on Manual Lathe / watch full video and learn amazing process
#threadcreating
#makingthreadwithdrill
#pkprocess
#threadcreating
#makingthreadwithdrill
#pkprocess
We Created a Thread With a Thread Drill on Manual Lathe #sticwelder
We Created a Thread With a Thread Drill on Manual Lathe / watch full video and learn amazing process
How to thread facial hair at home | Upper lip mustache hair removal DIY
FANG Interview Question | Process vs Thread
Ultra Close up - Needle and thread
Teaching you how to thread your own upper lip!
FOUNDATIONS MADE FOR DARK SKIN?! Ft. Thread Beauty #makeup #beauty
Thread Painting 😱🥰#diy #shorts #viralvideo #craftwithsunshine #ytshorts #threadpainting
Thread Sample Question 01 using Java
Why we need threads?
How to tie elastic thread bracelet / bileklik nasıl bağlanır. #bracelet #connect
amazing thread latkan making tutorial #heenadholakiya #handembroiderydesigns
3d shapes using thread🧵| Made by-Tanvi.
Get return value from a thread (pthread_join)
Difference Between Implementing Runnable Interface and Extending Thread Class | Runnable vs Thread
Woollen thread weaving begins
Creating a Thread by Extending Thread class
#/Thread Painting/#🎨🖌️ #shorts #drawing #trending #art
THREAD TOOL Tutorial - Autodesk Fusion 360 Tool Tutorial
We created a coral reef and the results are fascinating!
Thread Creation in Java | What is Thread in Java | How to create a thread in java | Java Programming
How To - Replicate any thread with Tinkercad!
beginner thread bracelet tutorial! 🎀🤍
Satisfying! Making Threads NEW Again. Thread Chaser
Комментарии