filmov
tv
Gear cutting on a Shaper (making the tool)
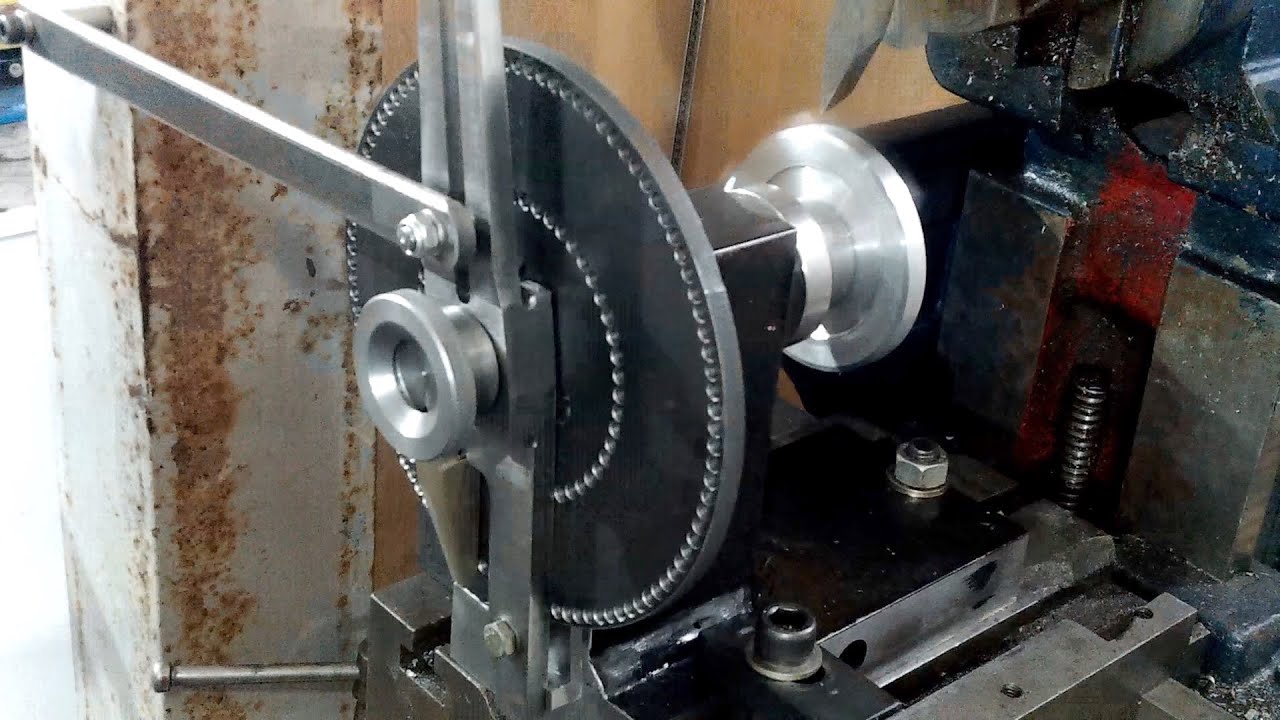
Показать описание
Cutting Gears on a Shaper (making the tool). (Go to 21min 55sec to see the less detailed bit) This tool/device is designed to make any gear size from 46mm to 160mm diameter, and any number of teeth from 10 to 100.
By using sleeves and collars any variation of gear blank bore can be fitted. The one caviat is that keyways must be used. This video shows how I made the tool/device for the shaper and shows you how I use it. The gear making tool works well, and made an aluminium gear that meshed very nicely with the gear I copied it from. I’m also surpised how quickly the shaper made the gear, each tooth in the video, was formed in less than two minutes each, that wasn’t any where near the speed it could have completed the task. The only problem with this project is the huge quantity of index holes that are required to achieve the target number of gear sizes.
I am leaving the project open for anyone to modify and improve. enjoy.
I'd like to say thanks to Geoffrey Croker for inspiring me to make this project.
I would like to thank 'This old tony’ and ‘Mrpete222’ for their role in helping me understand the art of gear making.
By using sleeves and collars any variation of gear blank bore can be fitted. The one caviat is that keyways must be used. This video shows how I made the tool/device for the shaper and shows you how I use it. The gear making tool works well, and made an aluminium gear that meshed very nicely with the gear I copied it from. I’m also surpised how quickly the shaper made the gear, each tooth in the video, was formed in less than two minutes each, that wasn’t any where near the speed it could have completed the task. The only problem with this project is the huge quantity of index holes that are required to achieve the target number of gear sizes.
I am leaving the project open for anyone to modify and improve. enjoy.
I'd like to say thanks to Geoffrey Croker for inspiring me to make this project.
I would like to thank 'This old tony’ and ‘Mrpete222’ for their role in helping me understand the art of gear making.
Комментарии