filmov
tv
GAME OVER For Hotend/Extruder Design? - The Biqu H2 Direct Drive Hemera Alternative
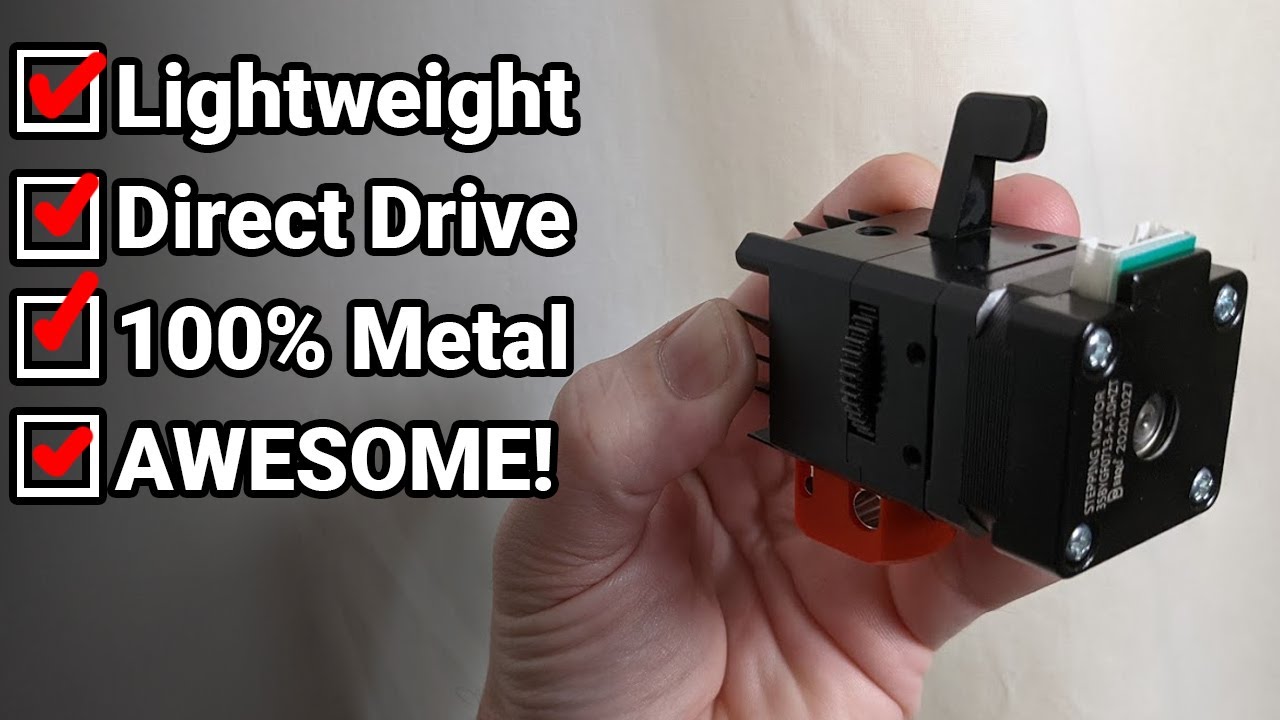
Показать описание
Direct drive extruders make superior quality 3D prints, but you pay a major price for that quality. They are slow! By reducing the weight you can speed up the printing. This hotend and extruder combination (The Biqu H2) is the lightest such design out there which is also 100% metal construction. Therefore you can put it in an enclosure and it will stay dimensionally stable. So what's the catch? What's wrong with it?
GAME OVER For Hotend/Extruder Design? - The Biqu H2 Direct Drive Hemera Alternative
3D Printed Pin Support Challenge 😱
printed WITHOUT support #shorts
The ONE GAME-CHANGING Slicer SETTING... (Huge 3D Print Quality BOOST)
Extruder test pattern
hotend prototype
Bambu Lab P1P NASA fabric (TurboDork)
Revolutionizing 3D Printing: Prusa's Game-Changing Nextruder
3D Printing is SLOW?| FLSUN V400
My Genshin sword took 150h to 3D print! ⚔️ #diycrafts #cosplay
The fantastic* BIQU H2 extruder/hot end - (*IF you get a good one)
I built a working Hotend out of a CPU cooler!
I tried to find the Strongest Filament Extruder.
Is this the right way to find out? - Ultimate HotEnd Testing - Episode #2
Who says one nozzle is enough!? 3D printing with different nozzle sizes
Water Cooled 3D Printer Test Print: Benchy Boat
3D Printer Problem: do you know How to Fix Z-Wobble?
Flame Retardant 3D Benchy!
Mechanical Tool Swap system for the Creality Ender 3, it ROCKS!🤘
Game Changer For Multi Color 3d Printing (AMS)
Dragon hotend for 3d printer. 4k video
Arc Overhangs make Supports Obsolete!
The 3D Printer I'd buy if I started over
Choosing a Hotend
Комментарии