filmov
tv
Prototyping on the METAL LATHE | Turning Tuesday #12
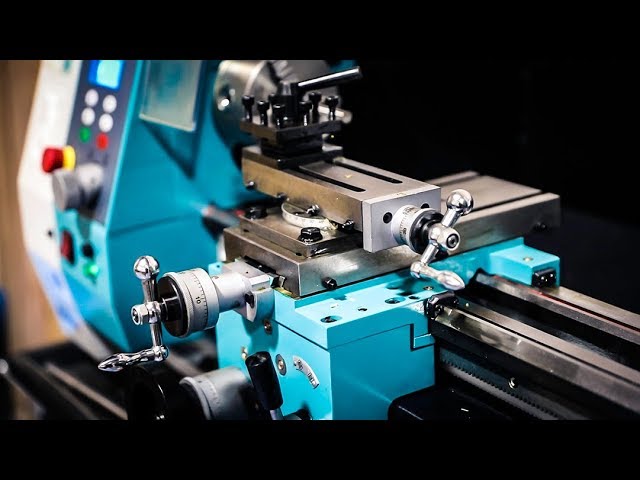
Показать описание
In this video, I have a go at using the metal lathe to make a prototype for a future.... thing I will be making.... possibly?
______
MY FREE ONLINE COURSES:
🚀 Purchasing and Using Tools Correctly
🎁 How To Make a Dovetailed Box:
🛠 How To Make a Cabinet:
🧰 How To Make a Toolbox:
✏️ How To Design Furniture
______
HOW TO SUPPORT THE CHANNEL:
💪 Become a Patron - Donate a Regular Amount of Your Choice
👕 Purchase Merchandise - Premium Materials, Quality Design.
🎁 Wishlist - Help us Purchase New Equipment & Resources!
🍺 Send a Tip - Quick, Easy, and Massively Appreciated!
______
WOODWORKING BOOKS I RECOMMEND:
📘 Collins Complete Woodworkers Manual
📖 Workbenches: Design & Theory to Construction & Use
📚 The Overstory - My Favourite Fiction Books about Trees
______
MY FAVOURITE TOOLS:
🛠️ Knew Concepts Fret Saw
⬜️ Faithfull Engineers Squares
⚙️ Veritas Wheel Marking Gauge
🗡 Precision Marking Knife
🎥 Lumix S1H Mirrorless Camera
🔍 See EVERYTHING I Recommend HERE:
______
KEEP UP TO DATE WITH ME:
______
🕵️♂️ WHO AM I?:
My name is Matt Estlea and I’m a Woodworker from Basingstoke, England. My aim is to make your woodworking less s***.
I come from 5 years of TRAINING at Rycotewood Furniture Centre in Oxford, 5 years of experience WORKING at Axminster Tools and Machinery in Basingstoke, and 3 years TEACHING both day classes and evening classes at Rycotewood Furniture Centre. All while trying to get this YouTube thing off the ground.
By September 2021, I packed it all in to focus on YouTube and my business full-time.
Want to know more about how I crammed all this experience into such a short period of time? See my experience and qualifications here:
______
GET IN TOUCH:
While I take time to read every single message I receive whether it's emailed, DMed or asked publicly on social media, sadly I do not have time to reply to everything. If you have a short message you’d like to send, it’s best to send me a message on Twitter.
For longer messages, please drop me a message via the contact page on my website.
______
PS: Some of the links in this description are affiliate links that I get a lil’ commission from recommending at no extra cost to you. If you’d like to know more about how this works, and what businesses I work with, please read my affiliate disclaimer here:
______
MY FREE ONLINE COURSES:
🚀 Purchasing and Using Tools Correctly
🎁 How To Make a Dovetailed Box:
🛠 How To Make a Cabinet:
🧰 How To Make a Toolbox:
✏️ How To Design Furniture
______
HOW TO SUPPORT THE CHANNEL:
💪 Become a Patron - Donate a Regular Amount of Your Choice
👕 Purchase Merchandise - Premium Materials, Quality Design.
🎁 Wishlist - Help us Purchase New Equipment & Resources!
🍺 Send a Tip - Quick, Easy, and Massively Appreciated!
______
WOODWORKING BOOKS I RECOMMEND:
📘 Collins Complete Woodworkers Manual
📖 Workbenches: Design & Theory to Construction & Use
📚 The Overstory - My Favourite Fiction Books about Trees
______
MY FAVOURITE TOOLS:
🛠️ Knew Concepts Fret Saw
⬜️ Faithfull Engineers Squares
⚙️ Veritas Wheel Marking Gauge
🗡 Precision Marking Knife
🎥 Lumix S1H Mirrorless Camera
🔍 See EVERYTHING I Recommend HERE:
______
KEEP UP TO DATE WITH ME:
______
🕵️♂️ WHO AM I?:
My name is Matt Estlea and I’m a Woodworker from Basingstoke, England. My aim is to make your woodworking less s***.
I come from 5 years of TRAINING at Rycotewood Furniture Centre in Oxford, 5 years of experience WORKING at Axminster Tools and Machinery in Basingstoke, and 3 years TEACHING both day classes and evening classes at Rycotewood Furniture Centre. All while trying to get this YouTube thing off the ground.
By September 2021, I packed it all in to focus on YouTube and my business full-time.
Want to know more about how I crammed all this experience into such a short period of time? See my experience and qualifications here:
______
GET IN TOUCH:
While I take time to read every single message I receive whether it's emailed, DMed or asked publicly on social media, sadly I do not have time to reply to everything. If you have a short message you’d like to send, it’s best to send me a message on Twitter.
For longer messages, please drop me a message via the contact page on my website.
______
PS: Some of the links in this description are affiliate links that I get a lil’ commission from recommending at no extra cost to you. If you’d like to know more about how this works, and what businesses I work with, please read my affiliate disclaimer here:
Комментарии