filmov
tv
Experimental Jet Parts in Carbon Fiber
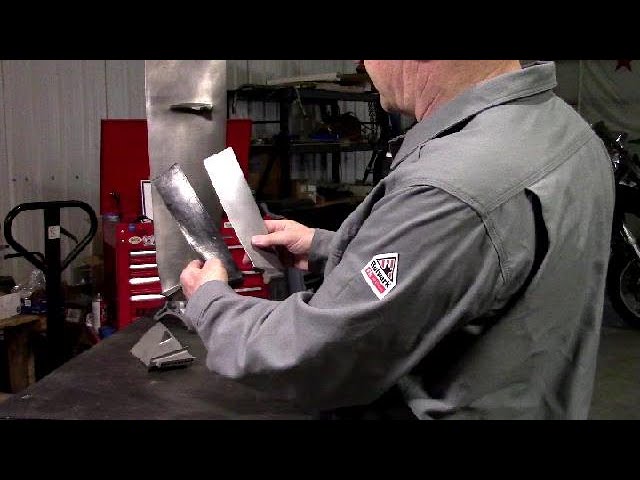
Показать описание
We have some compressor blades that we will be testing in one of our LM1500s. It's the industrial version of the J79 turbojet, which powers the F-104 Starfighter, the F-4 Phantom II, and many other aircraft.
These blades are made from highly compressed carbon fiber and resin composite, with some finish machining to alter their shape.
Let's hear your comments and ideas...
Videos of the running test are coming up.
These blades are made from highly compressed carbon fiber and resin composite, with some finish machining to alter their shape.
Let's hear your comments and ideas...
Videos of the running test are coming up.
Experimental Jet Parts in Carbon Fiber
How to make a carbon fiber part in under 1 minute.
Carbon Fiber Parts from 3D Printed Mold Patterns. RC Airplane Rudder. #carbonfiber #aviation
Difference between WET carbon (1) and DRY carbon fiber (2)
CARBON FIBER JET ENGINE UPDATE #1
Rocket Engineering: How to Remove a Carbon Fiber Tube from its Mold
Exoskeleton wing design - how carbon fiber makes it possible
Rudder with solid SS stock versus carbon fibre stock
The carbon fibre spinner blade experiment
Carbon Composite Turbojet Parts 2
HYDRAULIC PRESS VS TITANIUM AND CARBON FIBER PIPE
How carbon fiber varies in quality
Our carbon fiber parts strive for zero defects and 100% fitment. #qualitycontrol #carbonfiber
Carbon fiber breakdown implosion THE TITAN
🤯 Waterjet vs Carbon fiber🤯#waterjet #engineering #carbonfiber
See Thru Jet Engine
Most complicated CARBON FIBER part in the DarkAero 1!
CARBON FIBER + Honeycomb Sandwich Panels in the DarkAero 1 EXPLAINED!
Forged Carbon Fiber - Chopped Fibers (PART2 Result & New experiment)
High strength Carbon Rod Custom length 5mm 6mm 8mm Carbon Fibre Solid Rod #carbonfibre #solidrod
DIY Prepreg Forged Carbon Fiber Test
The Truth About Carbon Fiber: Myths vs. Reality
Make Carbon Fiber Car Parts By Autoclave
Carbon fiber tube display: the only guide you'll ever need #carbon fiber
Комментарии