filmov
tv
Sprinter Van Mercedes-Benz production at the Germany factory Part's 2.
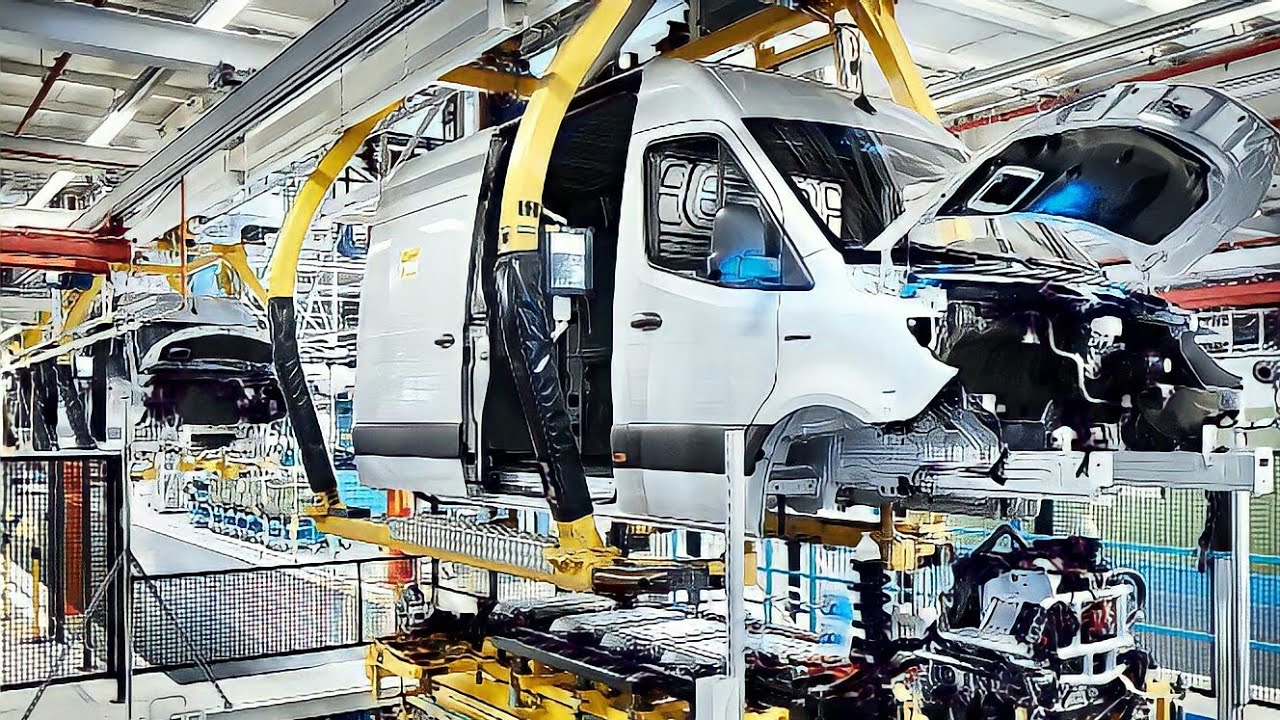
Показать описание
Mercedes-Benz Sprinter production at the Germany factory: Precision to a fraction of a millimeter - quality workmanship at the main van factory
With a workforce of some 6600 and an annual output of around 150,000 vans, Düsseldorf is Daimler AG's main factory for vans. All the closed variants of the Mercedes-Benz Sprinter – i.e. panel vans and crew buses – roll off the production line here. The factory has a shop floor covering almost 700,000 square meters and produces almost 700 vans per working day by way of a three-shift system. Daimler invested almost 36 million euros in the factory in 2012. A new combined heat and power station which cuts primary energy consumption at the factory by around 20 percent accounted for over a third of this investment volume. A particularly notable asset from the employees' point of view is the new factory restaurant which sets a benchmark throughout the group. The Sprinter is also produced in Ludwigsfelde (Germany), Argentina, the USA, China, and Russia.
Paintwork: emu feathers and ultra-fine coats of paint
Ten pretreatment stations and an extremely complex painting process provide the body of every van from Düsseldorf with perfect protection against corrosion. The pretreatment process is preceded by a so-called body-washer: at this station, the entire body is cleaned on the outside by rotating spray wheels and on the inside by other spraying equipment.
The actual painting process comprises zinc phosphating, cathodic dip priming, filler coat, and top coat. All the coats are ultra-fine, with a total thickness of 80 thousandths of a millimeter. On average, the paintwork on every Sprinter weighs in at 17.4 kg, and the painted surface area totals around 95 square meters.
Prior to top-coating, each body is cleaned with emu feathers on rotating rollers to remove the finest dust. Robots and employees share the task of sealing the body seams averaging a total length of 138 m with PVC. The water-based topcoat is applied to four lines. Several hundred different colors are possible. The top coat is applied using electrostatic systems – the fine paint particles are attracted to the body by electrostatic means.
Cavity sealing involves the same high degree of precision as the painting process: a large number of nozzles specified for each individual model automatically spray a precisely defined quantity of the protective coating into every cavity on the body. Together with the galvanized body panels, the sum total of all corrosion prevention measures provides permanent protection in all areas at risk of corrosion – rust has no chance.
Assembly: 197 stations, choice of up to 14,000 parts
Assembly is the most labor-intensive area of the production process. For reasons of space, assembly operations are also spread over three stories at the Düsseldorf factory. A workforce of 2400 is employed here. They complete the vehicle in a total of 197 steps. There are around 14,000 possible parts for every van. Keeping the required components available and supplying them in accordance with the production sequence is a feat of logistics.
The main focuses of the production process on the first and second floors are the interior and the exterior of the vehicle. One of the most impressive stations is the window fitting center – the largest of its type in the world. Robots precision-fit all of the vehicle's windows here.
The drive train is pre-assembled at the same time in an adjoining shop. It comprises the front and rear axle, engine, propeller shaft, and exhaust system. On the ground floor of the assembly, the shop is the "marriage station", where drivetrain and body are joined together.
Shortly after the marriage, the engines are started up for the first time as each van undergoes testing according to a specified programme on a roller dynamometer. In the finishing stage which then follows, the vans are fitted with their model plates, and they are cleaned and their doors undergo fine adjustment. The new vans are then scrutinized once more in the light tunnel.
Only then do the vans from the Düsseldorf factory move to their dispatch stations to await collection. Dispatch takes place by truck and rail. Around 310 trucks and eleven rail wagons laden with new vans leave the Düsseldorf factory every day. Some 80 of these trucks head for ports, from where one or two inland vessels set off with vans each week.
Materials and components are contributed by some 600 suppliers. The flow of materials amounts to around 280 trucks carrying 2850 t of material every day. Key assemblies for the Sprinter come from factories within the Daimler group: engines from Berlin, Mannheim, Stuttgart and Kölleda, rear axles from Kassel, transmissions from Gaggenau.
#howtomake#sprinter#Benz #mercedes #van#factory #plant#machine #plant#manufacturing
Credit: Mercedes-Benz
👍👍Thank you for watching 👍👍
With a workforce of some 6600 and an annual output of around 150,000 vans, Düsseldorf is Daimler AG's main factory for vans. All the closed variants of the Mercedes-Benz Sprinter – i.e. panel vans and crew buses – roll off the production line here. The factory has a shop floor covering almost 700,000 square meters and produces almost 700 vans per working day by way of a three-shift system. Daimler invested almost 36 million euros in the factory in 2012. A new combined heat and power station which cuts primary energy consumption at the factory by around 20 percent accounted for over a third of this investment volume. A particularly notable asset from the employees' point of view is the new factory restaurant which sets a benchmark throughout the group. The Sprinter is also produced in Ludwigsfelde (Germany), Argentina, the USA, China, and Russia.
Paintwork: emu feathers and ultra-fine coats of paint
Ten pretreatment stations and an extremely complex painting process provide the body of every van from Düsseldorf with perfect protection against corrosion. The pretreatment process is preceded by a so-called body-washer: at this station, the entire body is cleaned on the outside by rotating spray wheels and on the inside by other spraying equipment.
The actual painting process comprises zinc phosphating, cathodic dip priming, filler coat, and top coat. All the coats are ultra-fine, with a total thickness of 80 thousandths of a millimeter. On average, the paintwork on every Sprinter weighs in at 17.4 kg, and the painted surface area totals around 95 square meters.
Prior to top-coating, each body is cleaned with emu feathers on rotating rollers to remove the finest dust. Robots and employees share the task of sealing the body seams averaging a total length of 138 m with PVC. The water-based topcoat is applied to four lines. Several hundred different colors are possible. The top coat is applied using electrostatic systems – the fine paint particles are attracted to the body by electrostatic means.
Cavity sealing involves the same high degree of precision as the painting process: a large number of nozzles specified for each individual model automatically spray a precisely defined quantity of the protective coating into every cavity on the body. Together with the galvanized body panels, the sum total of all corrosion prevention measures provides permanent protection in all areas at risk of corrosion – rust has no chance.
Assembly: 197 stations, choice of up to 14,000 parts
Assembly is the most labor-intensive area of the production process. For reasons of space, assembly operations are also spread over three stories at the Düsseldorf factory. A workforce of 2400 is employed here. They complete the vehicle in a total of 197 steps. There are around 14,000 possible parts for every van. Keeping the required components available and supplying them in accordance with the production sequence is a feat of logistics.
The main focuses of the production process on the first and second floors are the interior and the exterior of the vehicle. One of the most impressive stations is the window fitting center – the largest of its type in the world. Robots precision-fit all of the vehicle's windows here.
The drive train is pre-assembled at the same time in an adjoining shop. It comprises the front and rear axle, engine, propeller shaft, and exhaust system. On the ground floor of the assembly, the shop is the "marriage station", where drivetrain and body are joined together.
Shortly after the marriage, the engines are started up for the first time as each van undergoes testing according to a specified programme on a roller dynamometer. In the finishing stage which then follows, the vans are fitted with their model plates, and they are cleaned and their doors undergo fine adjustment. The new vans are then scrutinized once more in the light tunnel.
Only then do the vans from the Düsseldorf factory move to their dispatch stations to await collection. Dispatch takes place by truck and rail. Around 310 trucks and eleven rail wagons laden with new vans leave the Düsseldorf factory every day. Some 80 of these trucks head for ports, from where one or two inland vessels set off with vans each week.
Materials and components are contributed by some 600 suppliers. The flow of materials amounts to around 280 trucks carrying 2850 t of material every day. Key assemblies for the Sprinter come from factories within the Daimler group: engines from Berlin, Mannheim, Stuttgart and Kölleda, rear axles from Kassel, transmissions from Gaggenau.
#howtomake#sprinter#Benz #mercedes #van#factory #plant#machine #plant#manufacturing
Credit: Mercedes-Benz
👍👍Thank you for watching 👍👍