filmov
tv
EBManPower - Case study for thick section electron beam welding
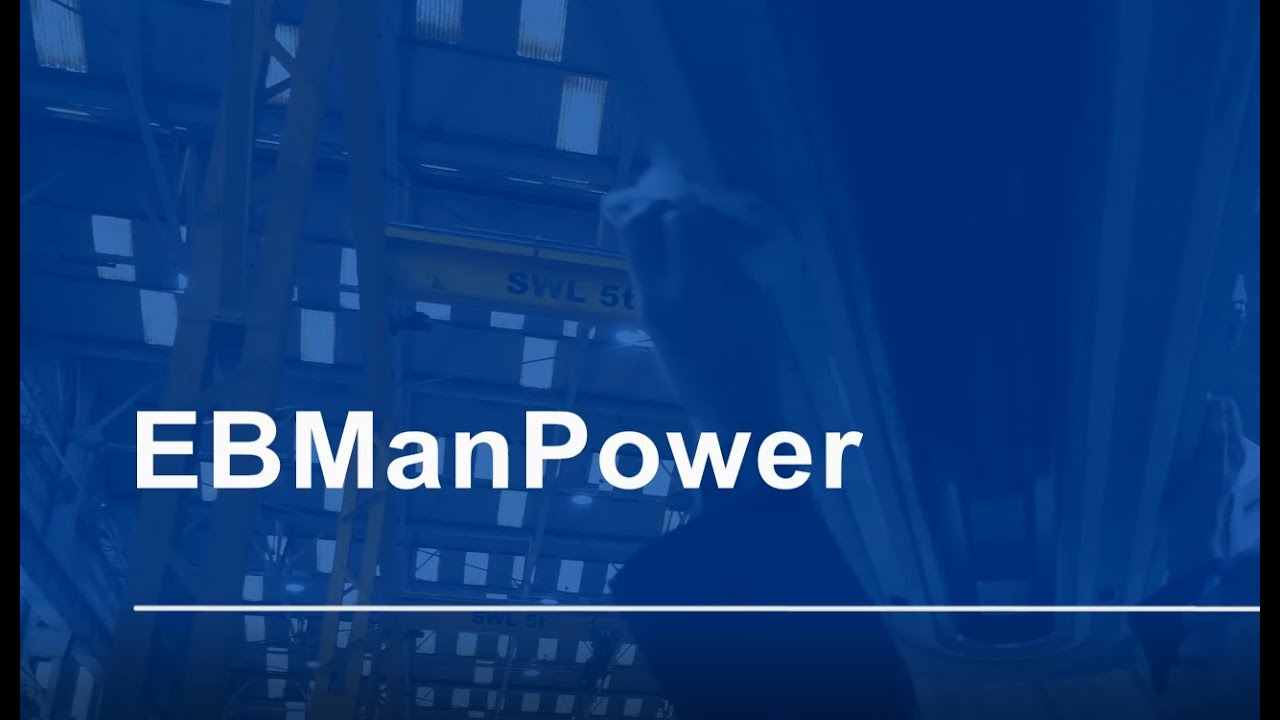
Показать описание
The aim of the EBManpower Project is to provide a solution for the rapid serial manufacture of thick section vessels for the nuclear and other industries.
EBMan power项目,针对核工业中使用厚板材料制造的压力容器,开发了快速连续制造工艺解决方案。该解决方案也可以在多个其他工业应用中使用。
To achieve this, a consortium led by Cammell Laird and including CVE and TWI are investigating low cost, single pass electron beam welding of 60mm thick stainless steel. This will be performed in a local vacuum as opposed to a vacuum chamber using the consortium’s existing logistical and manufacturing capabilities here in the UK.
项目团队由TWI、Cammell Laird公司以及CVE公司组成,致力于针对60毫米厚不锈钢的低成本单道电子束焊接工艺的开发。与传统的真空腔内焊接不同,项目团队使用了局部真空的工艺方案,在英国的实验室与生产基地进行技术研发。
By using existing equipment and the current manufacturing chain, the project will minimise labour and associated costs, and also removes the need for construction of a bespoke EB welding facility.
项目的开发的新技术,可以直接通过改装与升级现有的设备来实现,无需专门购置整套新设备,因此整体投资较小。
Overall, this means less capital outlay, less maintenance and with a commercially available electron beam-welding machine with no chamber restriction on the size of pieces to be joined.
总体来说,新工艺的主要优势,包括较低的设备投资以及维护成本,也没有像传统工艺因为真空腔尺寸而带来的工件大小限制。
Testing the technology in an industrial fabrication facility makes it possible to assess the influence of the working environment in full scale production.
通过在工业生产环境里对新工艺的测试,项目团队深入地评估了新工艺在全面生产应用中的可行性。
Local vacuum electron beam welding can be used to provide near net shape manufacturing at close to the required thickness. There are also no expensive consumables required, therefore the final weld composition and properties are similar to the base materials.
局部真空电子束焊接技术生产的接头厚度与母材厚度十分接近,是一种近净成形技术,焊后仅需少量加工或不再加工。。该工艺不需要任何昂贵的焊接耗材,形成的焊缝金属的化学成分与性能都与母材相似。
The joining rate can be up to 90% faster than other welding methods, cutting down on labour and inspection costs as well as offering much higher productivity. With less post-weld machining and a high level of integrity, the overall performance is superior to other joining methods.
与其他焊接工艺相比,新工艺可将焊接速度提高90%,在提升生产效率同时,也明显降低了人工与检测成本。焊后仅需少量加工或者不再加工,,焊接接头的完整性优秀、整体性能优于其他焊接工艺。
EBManpower achieves this by simplifying the manufacturing and qualification processes, firstly by cold bending ordinary hot rolled stainless plates to form a cylindrical canister. This canister sections are then longitudinally EB welded. Therefore logistically more efficient and less costly than alternative manufacturing routes.
EBManpower项目,简化了制造加工工艺和检测评定。首先通过冷弯将普通热轧不锈钢板弯成圆柱罐状,然后使用电子束沿着纵向接缝进行焊接形成管环。与其他制造方法相比,该方法效率更高、成本更低。
Multiple canister sections can then be circumferentially EB welded together to form a complete vessel. With the welding development and qualification being done in a small chamber machine. There is no need to qualify the weld on a full scale test piece. The final welding machine and operators can then be qualified through non-destructive testing of the demonstration assembly , to eliminate the need to extract and destructively test samples from the vessel. EB welding is a code-compliant process, it has been used for the nuclear and aerospace industries for decades. It is highly repeatable and only needs a single trained operator rather than a coded welders to conduct the welding process. The welding parameters can be developed off-site by a specialist and transferred to site for production.
通过电子束环焊缝, 将多个管环组合连接在一起,从而形成完整的容器结构件。焊接工艺的开发与评定,可以仅使用小型焊接腔设备,无需使用全尺寸试样。实际焊接生产设备和操作人员的评定,可以通过对演示组件的无损检测来进行,避免了在容器件上取样进行破坏性测试。电子束焊接是标准合规的制造工艺,数十年来在核电以及航空工业广为应用。该工艺具有高度可重复性,相比需要专业资格认证焊工的传统工艺,电子束焊接仅需受过培训的设备操作人员即可完成。焊接工程师无需在生产现场开发工艺参数,可以在远程开发后再发送到现场。。
The challenges addressed, included an increased tolerance for EB welding to joint fit-up, leading to further reductions in cost through being able to accept a gap of up to 0.6mm.
电子束焊接技术目前面临的主要挑战之一,是如何降低对接头破口装配精度的要求。在项目中,技术团队成功将工艺可接受的最大装配间隙增加到0.6毫米,步大幅降低了生产成本
Local vacuum electron beam welding can be used for a wide range of applications, such as non-nuclear pressure vessels, monopiles for wind turbine foundations, and underwater data centres.
局部真空电子束焊接可以应用在很多领域,比如核电之外的压力容器、风力发电单桩基座以及水下数据中心等领域。
Funded by Innovate UK, this project is being led by Cammell Laird in collaboration with Cambridge Vacuum Engineering and TWI.
该项目由英国创新基金资助,由TWI、Cammell Laird公司以及CVE公司联合完成。
EBMan power项目,针对核工业中使用厚板材料制造的压力容器,开发了快速连续制造工艺解决方案。该解决方案也可以在多个其他工业应用中使用。
To achieve this, a consortium led by Cammell Laird and including CVE and TWI are investigating low cost, single pass electron beam welding of 60mm thick stainless steel. This will be performed in a local vacuum as opposed to a vacuum chamber using the consortium’s existing logistical and manufacturing capabilities here in the UK.
项目团队由TWI、Cammell Laird公司以及CVE公司组成,致力于针对60毫米厚不锈钢的低成本单道电子束焊接工艺的开发。与传统的真空腔内焊接不同,项目团队使用了局部真空的工艺方案,在英国的实验室与生产基地进行技术研发。
By using existing equipment and the current manufacturing chain, the project will minimise labour and associated costs, and also removes the need for construction of a bespoke EB welding facility.
项目的开发的新技术,可以直接通过改装与升级现有的设备来实现,无需专门购置整套新设备,因此整体投资较小。
Overall, this means less capital outlay, less maintenance and with a commercially available electron beam-welding machine with no chamber restriction on the size of pieces to be joined.
总体来说,新工艺的主要优势,包括较低的设备投资以及维护成本,也没有像传统工艺因为真空腔尺寸而带来的工件大小限制。
Testing the technology in an industrial fabrication facility makes it possible to assess the influence of the working environment in full scale production.
通过在工业生产环境里对新工艺的测试,项目团队深入地评估了新工艺在全面生产应用中的可行性。
Local vacuum electron beam welding can be used to provide near net shape manufacturing at close to the required thickness. There are also no expensive consumables required, therefore the final weld composition and properties are similar to the base materials.
局部真空电子束焊接技术生产的接头厚度与母材厚度十分接近,是一种近净成形技术,焊后仅需少量加工或不再加工。。该工艺不需要任何昂贵的焊接耗材,形成的焊缝金属的化学成分与性能都与母材相似。
The joining rate can be up to 90% faster than other welding methods, cutting down on labour and inspection costs as well as offering much higher productivity. With less post-weld machining and a high level of integrity, the overall performance is superior to other joining methods.
与其他焊接工艺相比,新工艺可将焊接速度提高90%,在提升生产效率同时,也明显降低了人工与检测成本。焊后仅需少量加工或者不再加工,,焊接接头的完整性优秀、整体性能优于其他焊接工艺。
EBManpower achieves this by simplifying the manufacturing and qualification processes, firstly by cold bending ordinary hot rolled stainless plates to form a cylindrical canister. This canister sections are then longitudinally EB welded. Therefore logistically more efficient and less costly than alternative manufacturing routes.
EBManpower项目,简化了制造加工工艺和检测评定。首先通过冷弯将普通热轧不锈钢板弯成圆柱罐状,然后使用电子束沿着纵向接缝进行焊接形成管环。与其他制造方法相比,该方法效率更高、成本更低。
Multiple canister sections can then be circumferentially EB welded together to form a complete vessel. With the welding development and qualification being done in a small chamber machine. There is no need to qualify the weld on a full scale test piece. The final welding machine and operators can then be qualified through non-destructive testing of the demonstration assembly , to eliminate the need to extract and destructively test samples from the vessel. EB welding is a code-compliant process, it has been used for the nuclear and aerospace industries for decades. It is highly repeatable and only needs a single trained operator rather than a coded welders to conduct the welding process. The welding parameters can be developed off-site by a specialist and transferred to site for production.
通过电子束环焊缝, 将多个管环组合连接在一起,从而形成完整的容器结构件。焊接工艺的开发与评定,可以仅使用小型焊接腔设备,无需使用全尺寸试样。实际焊接生产设备和操作人员的评定,可以通过对演示组件的无损检测来进行,避免了在容器件上取样进行破坏性测试。电子束焊接是标准合规的制造工艺,数十年来在核电以及航空工业广为应用。该工艺具有高度可重复性,相比需要专业资格认证焊工的传统工艺,电子束焊接仅需受过培训的设备操作人员即可完成。焊接工程师无需在生产现场开发工艺参数,可以在远程开发后再发送到现场。。
The challenges addressed, included an increased tolerance for EB welding to joint fit-up, leading to further reductions in cost through being able to accept a gap of up to 0.6mm.
电子束焊接技术目前面临的主要挑战之一,是如何降低对接头破口装配精度的要求。在项目中,技术团队成功将工艺可接受的最大装配间隙增加到0.6毫米,步大幅降低了生产成本
Local vacuum electron beam welding can be used for a wide range of applications, such as non-nuclear pressure vessels, monopiles for wind turbine foundations, and underwater data centres.
局部真空电子束焊接可以应用在很多领域,比如核电之外的压力容器、风力发电单桩基座以及水下数据中心等领域。
Funded by Innovate UK, this project is being led by Cammell Laird in collaboration with Cambridge Vacuum Engineering and TWI.
该项目由英国创新基金资助,由TWI、Cammell Laird公司以及CVE公司联合完成。