filmov
tv
Industrial IoT (SCADA & M2M) Solutions over TETRA™
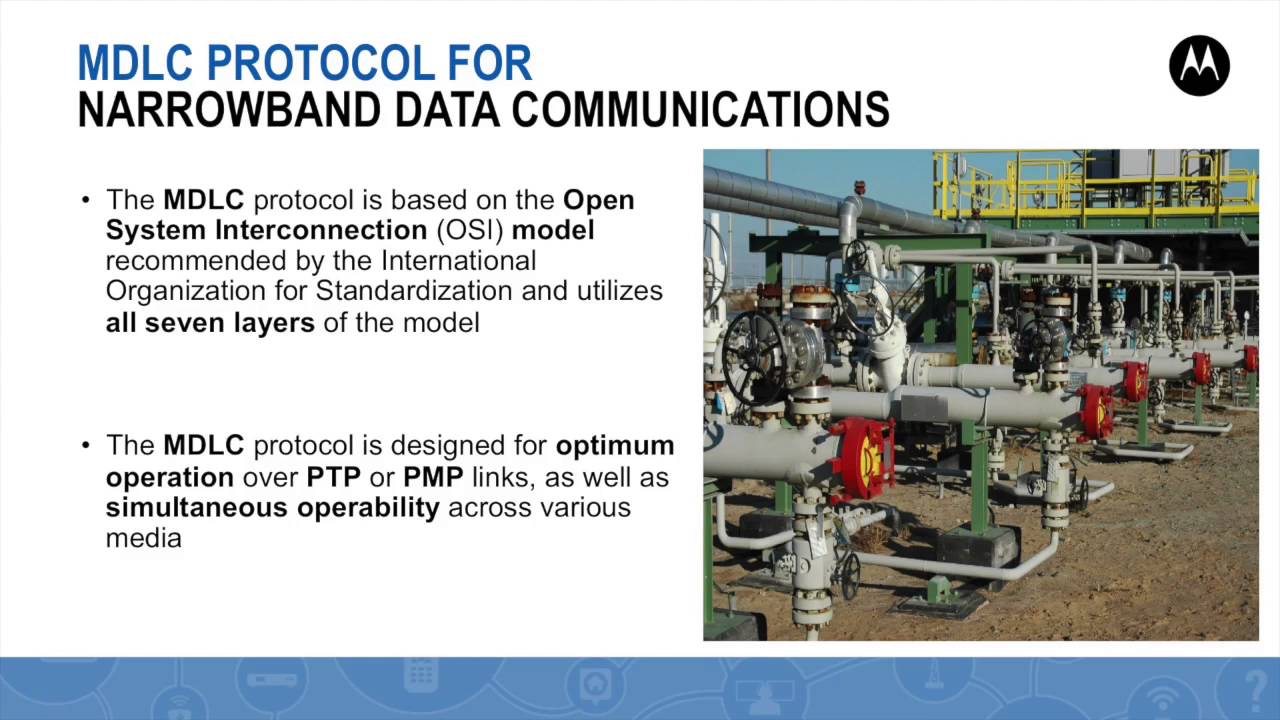
Показать описание
In this webinar you will get an overview of the Industrial Internet of Things (IIoT) portfolio and learn how you can utilize your IIoT solution over your existing TETRA infrastructure.
00:01
Hello My name is Eitan and I am a member of the Industrial IoT Support team which is part of the IIOT development group in MIL.
00:11
This webinar deals with MOTOROLA Industrial IoT system over TETRA infrastructure.
The objectives of this webinar are to understand: What is an Industrial IoT Solution? And how can a Motorola TETRA system, be utilized for an Industrial IoT Solution.
00:32 – 02:54
First let us clarify the terminology used when dealing with INDUSTRIAL IoT also known as SCADA and M2M. SUPERVISORY CONTROL AND DATA ACQUISITION which in acronym is SCADA, refer to real-time process control systems used to centrally monitor and control remote or local equipment such as motors, valves, pumps, relays, sensors, etc. So SCADA is a combination of telemetry and data acquisition.
MACHINE-TO-MACHINE which in acronym is M2M, refers to intelligent electronic devices which are used for data connectivity and communication to expand the user’s operational view and control. INTERNET OF THINGS which in acronym is IOT, refers to a network of physical objects that feature an IP address for data connectivity and communication, across a combination of communication networks which was referred here as network of networks. This network allows the capability of working together to collect and communicate data across operations.
INDUSTRIAL IoT stands for connecting operational and information technology across industrial and critical infrastructure environments to leverage data for the process automation and monitoring necessity for increasing productivity. The figure in front of us displays the key entities in Motorola IIoT solution. At the right side of the slide, our SCADA RTU and M2M modem serves as an IOT gateway to various IOT sensors and operational technologies. The collected data is transported to an HMI via the Front-End-Processor gateway over an LMR or other communication networks, partially mentioned here under the network of networks list, The FEP provides a two-way path to the communication system between the RTUs and the IIoT Manager Host entity. The HMI could be a manned control center or mobile applications devices such as smart phones or tablets.
02:54
The multiple Industrial IoT RTUs, gateways and FEPs in the system may communicate over a highly sophisticated hybrid data communication network by utilizing a variety of radio and/or line communication links. Radio links may include conventional systems, analog trunked systems, digital trunked systems, and both analog and digital microwave radio technologies. Line links may include point-to-point, multi-drop, cellular packet data modems, and Local Area Networks (LAN).
The various Industrial IoT RTUs may communicate with:
• Other RTUs,
• With one or more computerized control centers
• And with third party PLCs or other devices.
The RTUs network, allows each RTU the ability to communicate with the control center via other RTUs which can serve as a store & forward or network communication node in the overall network, hence extending the communication coverage and lower its costs. The RTUs communicate upward with control centers and downward with third party intelligent devices and PLC using a variety of standard protocols such as MODBUS, DNP3, and other specialized drivers.
04:20
The MDLC which stands for Motorola Data Link Communication is our propriety protocol which incorporates all the seven layers of the OSI standard and was adapted for the Industrial IoT. This protocol is optimal for narrow-band communication channels. The MDLC supports multiple logical channels per RTU’s physical communication port, enabling simultaneous central-to-RTU and RTU-to-RTU sessions. It also enables each RTU to simultaneously run several kinds of communications such as reporting alarms by contention, performing on-line monitoring and extensive diagnostics checks, etc. The Point to point and point to multi point links, which are in acronym PTP and PMP, could be two-way radio, leased line, LAN/WAN, or multi drop wire line.
05:25
Now that we have established some background as to what the Industrial IOT solution is, I would like to go over how it can be utilized over the TERTA infrastructure.
05:40
In the TETRA system, much like the ASTRO P25 system, the connection to the infrastructure can be made via LAN on the front end unit and via radio on the RTU. The LAN port of the ACE1100 FEP or ACE4600 IP GW has to be connected to the TETRA CEN which stands for Customer Enterprise Network.
00:01
Hello My name is Eitan and I am a member of the Industrial IoT Support team which is part of the IIOT development group in MIL.
00:11
This webinar deals with MOTOROLA Industrial IoT system over TETRA infrastructure.
The objectives of this webinar are to understand: What is an Industrial IoT Solution? And how can a Motorola TETRA system, be utilized for an Industrial IoT Solution.
00:32 – 02:54
First let us clarify the terminology used when dealing with INDUSTRIAL IoT also known as SCADA and M2M. SUPERVISORY CONTROL AND DATA ACQUISITION which in acronym is SCADA, refer to real-time process control systems used to centrally monitor and control remote or local equipment such as motors, valves, pumps, relays, sensors, etc. So SCADA is a combination of telemetry and data acquisition.
MACHINE-TO-MACHINE which in acronym is M2M, refers to intelligent electronic devices which are used for data connectivity and communication to expand the user’s operational view and control. INTERNET OF THINGS which in acronym is IOT, refers to a network of physical objects that feature an IP address for data connectivity and communication, across a combination of communication networks which was referred here as network of networks. This network allows the capability of working together to collect and communicate data across operations.
INDUSTRIAL IoT stands for connecting operational and information technology across industrial and critical infrastructure environments to leverage data for the process automation and monitoring necessity for increasing productivity. The figure in front of us displays the key entities in Motorola IIoT solution. At the right side of the slide, our SCADA RTU and M2M modem serves as an IOT gateway to various IOT sensors and operational technologies. The collected data is transported to an HMI via the Front-End-Processor gateway over an LMR or other communication networks, partially mentioned here under the network of networks list, The FEP provides a two-way path to the communication system between the RTUs and the IIoT Manager Host entity. The HMI could be a manned control center or mobile applications devices such as smart phones or tablets.
02:54
The multiple Industrial IoT RTUs, gateways and FEPs in the system may communicate over a highly sophisticated hybrid data communication network by utilizing a variety of radio and/or line communication links. Radio links may include conventional systems, analog trunked systems, digital trunked systems, and both analog and digital microwave radio technologies. Line links may include point-to-point, multi-drop, cellular packet data modems, and Local Area Networks (LAN).
The various Industrial IoT RTUs may communicate with:
• Other RTUs,
• With one or more computerized control centers
• And with third party PLCs or other devices.
The RTUs network, allows each RTU the ability to communicate with the control center via other RTUs which can serve as a store & forward or network communication node in the overall network, hence extending the communication coverage and lower its costs. The RTUs communicate upward with control centers and downward with third party intelligent devices and PLC using a variety of standard protocols such as MODBUS, DNP3, and other specialized drivers.
04:20
The MDLC which stands for Motorola Data Link Communication is our propriety protocol which incorporates all the seven layers of the OSI standard and was adapted for the Industrial IoT. This protocol is optimal for narrow-band communication channels. The MDLC supports multiple logical channels per RTU’s physical communication port, enabling simultaneous central-to-RTU and RTU-to-RTU sessions. It also enables each RTU to simultaneously run several kinds of communications such as reporting alarms by contention, performing on-line monitoring and extensive diagnostics checks, etc. The Point to point and point to multi point links, which are in acronym PTP and PMP, could be two-way radio, leased line, LAN/WAN, or multi drop wire line.
05:25
Now that we have established some background as to what the Industrial IOT solution is, I would like to go over how it can be utilized over the TERTA infrastructure.
05:40
In the TETRA system, much like the ASTRO P25 system, the connection to the infrastructure can be made via LAN on the front end unit and via radio on the RTU. The LAN port of the ACE1100 FEP or ACE4600 IP GW has to be connected to the TETRA CEN which stands for Customer Enterprise Network.