filmov
tv
I 3D Printed 'Viral' Tools So You Don't Have To...
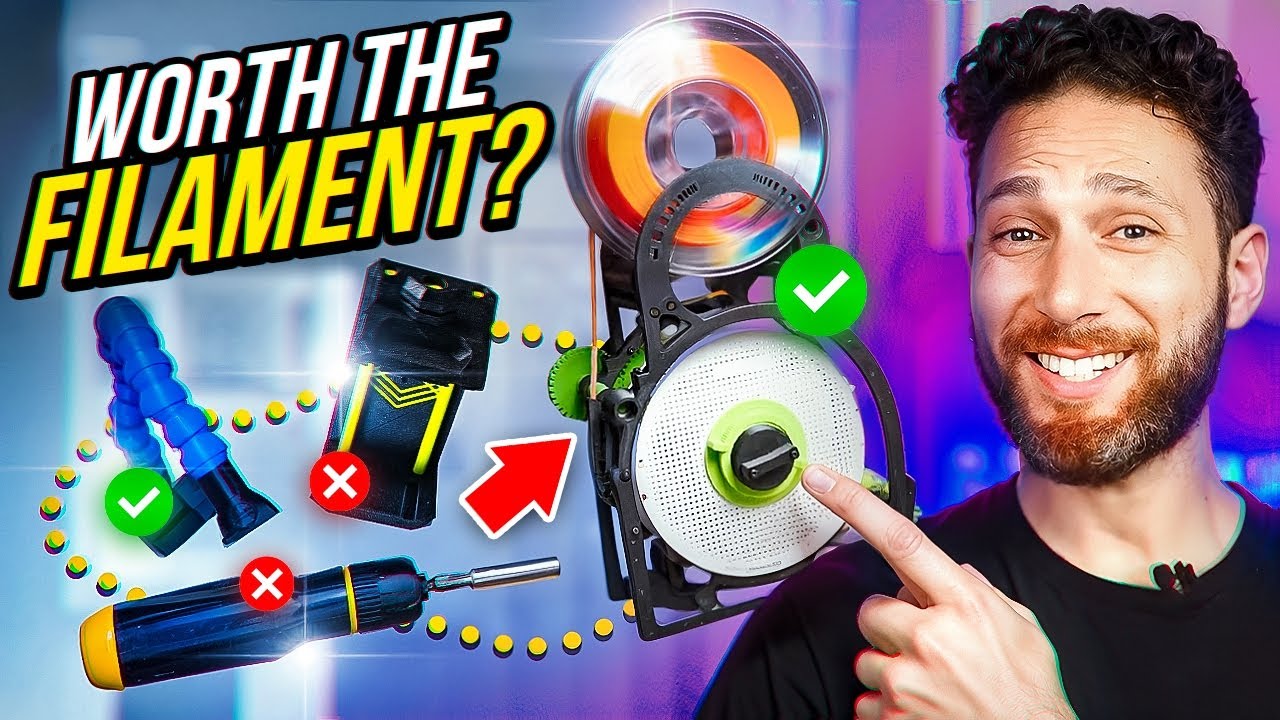
Показать описание
I love a good 3D Printed Tool - and functional 3d prints as a whole. The idea of being able to save money, time, and a trip to the hardware store, while getting EXACTLY the tool I want, in the color I want, with 3D Printable replacement parts when I inevitably break it? That, to me, is what 3D Printing is all about..
But in the last couple of years, as printers have gotten significantly better (and design competitions have gotten significantly more rewarding), I've noticed a certain trend... functional 3D Print designs are getting more and more complicated, with many more parts, much more assembly, and much more filament required...
In this video, we're going to take a look at some of the most popular, "advanced" 3D Printed Tools, and ask the question: are they worth your time, money, and most importantly... your filament?
🎥 IN THIS VIDEO: 🎥
00:00 Introduction
02:04 Flexible Hose for Dust Extraction
04:25 Table Saw FeatherBoard
05:46 Solder Scroll
07:42 Solder Flux Extruder
09:54 LTT Screwdriver
13:05 Mechanical Pencil
15:13 Table Vise
18:04 V-Roller Filament Spooler
23:26 Summary & Conclusion
🔗 LINKS MENTIONED IN THE VIDEO: 🔗
🗳 STL FILES OF FEATURED 3D PRINTING MODELS: 🗳
🛒 RECOMMENDED GEAR: 🛒
❤️ LOVED THIS VIDEO? ❤️
▶️ Subscribe to the channel
🔔 Turn on Notifications
🎁 Send a “Super Thanks” (Tip)
✍️ Write a comment below!
👍🏿 Like this video
#3dprinting #3dprinted #3dprinter
Комментарии