filmov
tv
Calibrating your XYZ steps using a dial gauge for maximum accuracy
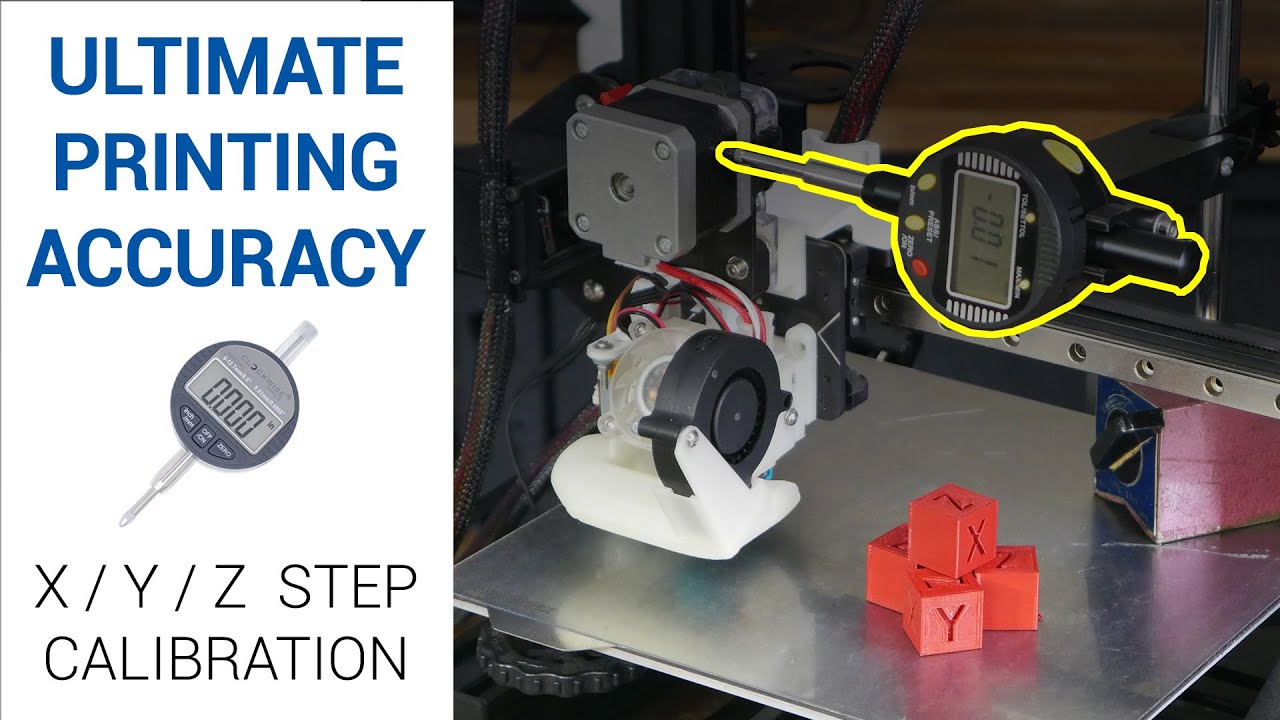
Показать описание
If the dimensions of your printed objects are out, this video will show how to use a dial gauge to measure and adjust your steps per mm for the X, Y and Z axes. It also covers the wrong way to tune this parameter so you don’t make the same mistake.
Thanks to the viewers and my patrons for requesting this guide and video.
Get Quality Resins from 3D Printers Online. 5% off storewide for Teaching Tech subscribers [Code: tech5]
Take a look around and if you like what you see, please subscribe.
Thanks to the viewers and my patrons for requesting this guide and video.
Get Quality Resins from 3D Printers Online. 5% off storewide for Teaching Tech subscribers [Code: tech5]
Take a look around and if you like what you see, please subscribe.
Calibrating your XYZ steps using a dial gauge for maximum accuracy
How to Calibrate a 3D Printer when the Holes come out Too Small
How I tune 3D Printers
3D printer calibration revolutionised - Step by step to better print quality
The Ultimate Guide to Perfect 3D Prints
Calibration : XYZ Calibration
XYZ Calibrator for 3D printing
SET YOUR STEPS - Fixing dimensional accuracy on your 3D printer (Cartesian only)
Rhino User Webinar: Electrical Appliances in Rhino & Grasshopper
XYZ calibration
How To Calibrate Your 3D Printers Extruder Esteps (Ender 3)
How To Calibrate Your 3d Printer Stepper Motors
Tuning 3D Printers - My Filament Secrets Revealed!
A Better Way To Calibrate Your 3D Printer. Importance of Dimensionally Accurate 3D Printed Products
Ender 3v2 - How to Calibrate E-Steps (Quick & Easy)
Part 2 Calibrate X Y Z axis made easy Wanhao D9 and other 3d printer
Calibrate ESteps on Ender 3 Pro Without a Computer
STOP Printing Calibration Cubes!
Calibrating your CNC axis and steps - Beginners guide
To Calibrate XYZ? Or Not....
Easiest Way to Calibrate E-Steps on 3D Printer with a Bowden Tube | Extruder Calibration Ender 3 Pro
Calibration des axes XYZ Avec pronterface - Imprimante 3D
Calibrating 3d Printer Flow Rate with Cura - The Quick Fix for Under Extrusion
3D printer calibration site V2 - Still free and better than ever!
Комментарии