filmov
tv
How SLS 3D Printing Technology Works
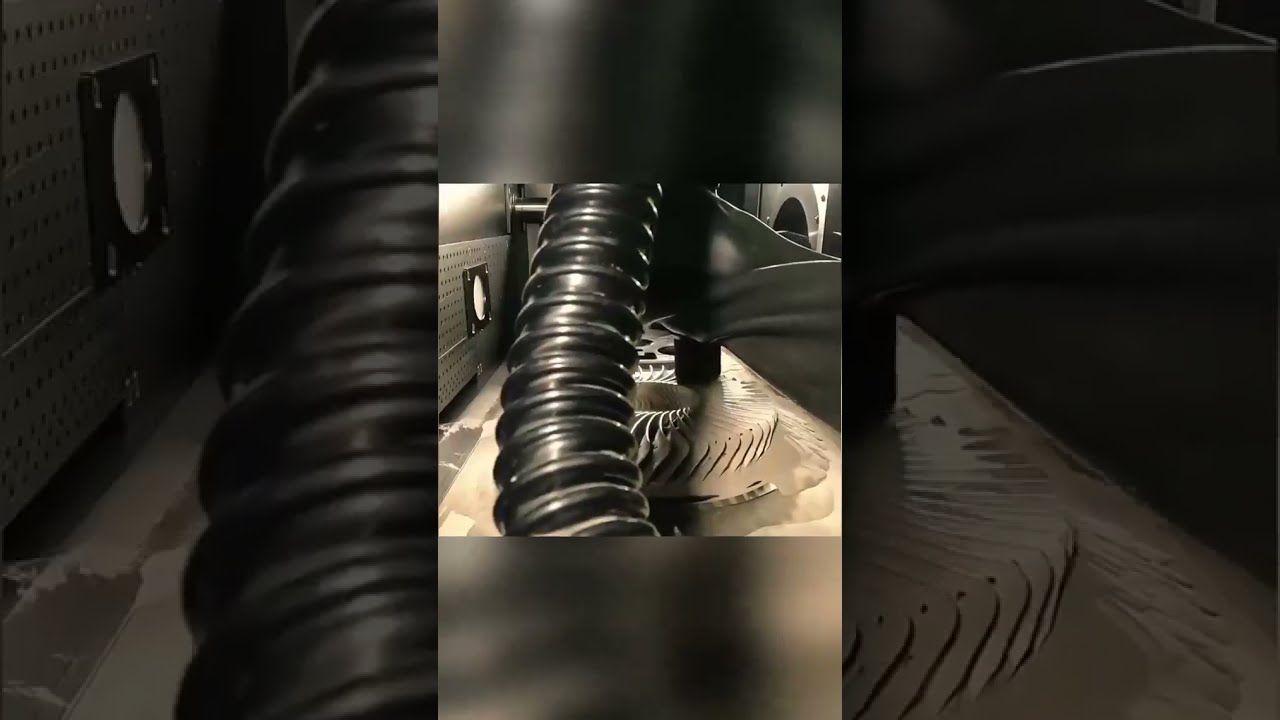
Показать описание
SLS (Selective Laser Sintering) is an additive manufacturing process that involves spreading powdered materials, such as nylon or metal, layer by layer and sintering it with a laser. The laser selectively fuses the powdered material by scanning it according to a 3D model. This process continues layer by layer until the desired part is built.
Here is a detailed breakdown of the advantages and disadvantages of SLS 3D printing technology.
🌟 Advantages of SLS 3D Printing Technology:
Material Variety:
SLS can use a wide range of materials, such as polymers, metals, ceramics, and nylon powders. Nylon is especially popular, making up around 90% of SLS printing applications. This versatility allows for diverse applications in industries such as automotive, aerospace, and healthcare.
High Accuracy:
SLS printing offers a high degree of accuracy, with a typical tolerance range of ±0.2 mm. This precision is highly advantageous for creating complex parts that require tight tolerances, making SLS an ideal choice for engineering applications that demand intricate designs and fine detail.
No Need for Support Structures:
One of the biggest advantages of SLS technology is that it doesn’t require support structures. The unsintered powder that remains during the printing process acts as a natural support for overhangs and suspended features, unlike other technologies (e.g., FDM and SLA) which require physical supports.
High Material Utilization:
The lack of support structures results in excellent material utilization rates. Since there is minimal material waste, SLS is one of the most efficient 3D printing methods. Additionally, sintered powder can be reused for future builds, further minimizing waste and material costs.
Durability and Strength:
Parts produced using SLS have superior mechanical properties compared to parts produced using other 3D printing technologies. The sintered layers fuse together well, resulting in strong, durable, and functional parts that can withstand mechanical stress and strain, making SLS suitable for end-use applications.
🔧 Disadvantages of SLS 3D Printing Technology:
Shrinkage and Warping:
A key challenge in SLS printing is the shrinkage that occurs when nylon or other powder materials cool after sintering. Uneven shrinkage can lead to dimensional inaccuracies or warping. While advanced software can help calculate and mitigate this issue, it is still a limitation that needs to be carefully managed.
Post-Processing is Labor-Intensive:
After printing, parts must be extracted from the powder bed, and excess powder needs to be removed, which is a manual and time-consuming process. Further post-processing steps, such as heat treatments or surface finishing, are often required to improve surface quality and mechanical performance.
Color Change and Moisture Absorption:
SLS-printed parts are often porous, meaning they can easily absorb moisture, dust, and oils from the environment. This can lead to changes in color, texture, or even degradation in part strength over time. Proper post-processing, such as sealing or coating, may be required to prevent moisture absorption.
High Equipment and Material Costs:
SLS 3D printers are generally more expensive than other types of 3D printers, such as FDM or SLA printers. Moreover, the materials used in SLS, particularly high-quality powders, are also costly. These factors make the overall investment in SLS technology relatively high, limiting accessibility to larger organizations with substantial budgets.
Material Loss and Damage:
While unsintered powder can be reused, the preheating process involved in sintering can degrade the material, rendering it unusable. As a result, fresh powder needs to be used with every print, contributing to material waste. Furthermore, material handling and preparation also require caution to avoid contamination or degradation.
Surface Finish:
Although SLS parts have excellent mechanical properties, the surface finish can be rough compared to SLA or PolyJet technologies. Post-processing steps such as polishing or tumbling are often needed to achieve a smoother surface, which can add additional time and cost to the production process.
Conclusion:
While SLS 3D printing is a powerful and versatile technology, especially for producing strong, functional parts without support structures, it also has its set of challenges, particularly in terms of post-processing, material handling, and cost. However, for many industries, the benefits of high accuracy, material variety, and part durability outweigh these drawbacks, making SLS an excellent choice for applications that require high-performance parts.
For industries like aerospace, automotive, healthcare, and engineering, where the quality of the final part is paramount, SLS remains a go-to technology for both prototyping and end-use production.
Here is a detailed breakdown of the advantages and disadvantages of SLS 3D printing technology.
🌟 Advantages of SLS 3D Printing Technology:
Material Variety:
SLS can use a wide range of materials, such as polymers, metals, ceramics, and nylon powders. Nylon is especially popular, making up around 90% of SLS printing applications. This versatility allows for diverse applications in industries such as automotive, aerospace, and healthcare.
High Accuracy:
SLS printing offers a high degree of accuracy, with a typical tolerance range of ±0.2 mm. This precision is highly advantageous for creating complex parts that require tight tolerances, making SLS an ideal choice for engineering applications that demand intricate designs and fine detail.
No Need for Support Structures:
One of the biggest advantages of SLS technology is that it doesn’t require support structures. The unsintered powder that remains during the printing process acts as a natural support for overhangs and suspended features, unlike other technologies (e.g., FDM and SLA) which require physical supports.
High Material Utilization:
The lack of support structures results in excellent material utilization rates. Since there is minimal material waste, SLS is one of the most efficient 3D printing methods. Additionally, sintered powder can be reused for future builds, further minimizing waste and material costs.
Durability and Strength:
Parts produced using SLS have superior mechanical properties compared to parts produced using other 3D printing technologies. The sintered layers fuse together well, resulting in strong, durable, and functional parts that can withstand mechanical stress and strain, making SLS suitable for end-use applications.
🔧 Disadvantages of SLS 3D Printing Technology:
Shrinkage and Warping:
A key challenge in SLS printing is the shrinkage that occurs when nylon or other powder materials cool after sintering. Uneven shrinkage can lead to dimensional inaccuracies or warping. While advanced software can help calculate and mitigate this issue, it is still a limitation that needs to be carefully managed.
Post-Processing is Labor-Intensive:
After printing, parts must be extracted from the powder bed, and excess powder needs to be removed, which is a manual and time-consuming process. Further post-processing steps, such as heat treatments or surface finishing, are often required to improve surface quality and mechanical performance.
Color Change and Moisture Absorption:
SLS-printed parts are often porous, meaning they can easily absorb moisture, dust, and oils from the environment. This can lead to changes in color, texture, or even degradation in part strength over time. Proper post-processing, such as sealing or coating, may be required to prevent moisture absorption.
High Equipment and Material Costs:
SLS 3D printers are generally more expensive than other types of 3D printers, such as FDM or SLA printers. Moreover, the materials used in SLS, particularly high-quality powders, are also costly. These factors make the overall investment in SLS technology relatively high, limiting accessibility to larger organizations with substantial budgets.
Material Loss and Damage:
While unsintered powder can be reused, the preheating process involved in sintering can degrade the material, rendering it unusable. As a result, fresh powder needs to be used with every print, contributing to material waste. Furthermore, material handling and preparation also require caution to avoid contamination or degradation.
Surface Finish:
Although SLS parts have excellent mechanical properties, the surface finish can be rough compared to SLA or PolyJet technologies. Post-processing steps such as polishing or tumbling are often needed to achieve a smoother surface, which can add additional time and cost to the production process.
Conclusion:
While SLS 3D printing is a powerful and versatile technology, especially for producing strong, functional parts without support structures, it also has its set of challenges, particularly in terms of post-processing, material handling, and cost. However, for many industries, the benefits of high accuracy, material variety, and part durability outweigh these drawbacks, making SLS an excellent choice for applications that require high-performance parts.
For industries like aerospace, automotive, healthcare, and engineering, where the quality of the final part is paramount, SLS remains a go-to technology for both prototyping and end-use production.