filmov
tv
Injection Molding Machine
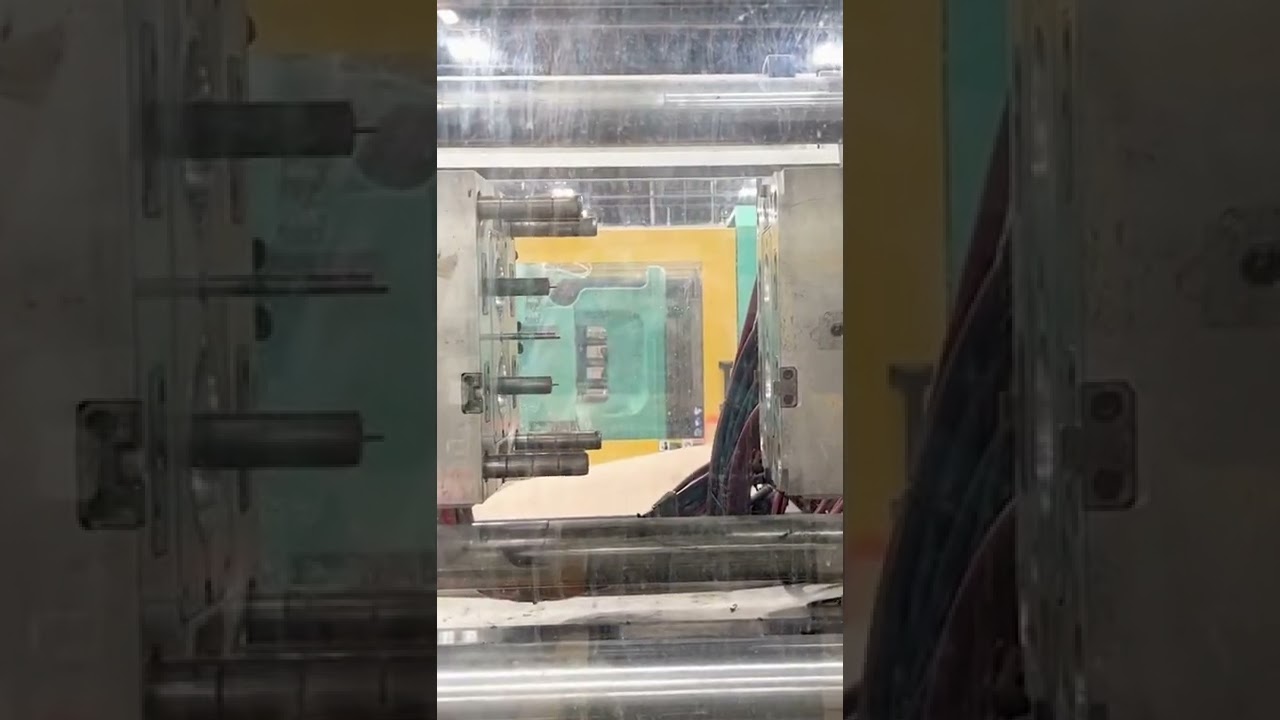
Показать описание
2014 Cincinnati Milacron MTS310 Injection Molding Machine 8071691
This machine is for sale! Visit the link below for more info on pricing and purchasing…
2014 Cincinnati Milacron MTS310, Capacity 310 Ton, Shot Size 36.2 oz, Tie Bar Spacing 26" x 26", Platen Size 37" x 37", Max Daylight 53.5", Min /Max Mold Height 7.9"/29.5", Clamp Stroke 45.6", Ejector Stroke 6.3", Screw Size 70 mm, Control B&R Control, Power Requirement 460V, Hours 15,800, FEATURES: Triple Core Pull, Robot Interface
What is Injection Molding?
Injection Molding is a manufacturing process for producing parts in large volume. It is most typically used in mass-production processes where the same part is being created thousands or even millions of times in succession.
Injection Molding Machine
Why You Might Want to Use Injection Molding
The principal advantage of injection molding is the ability to scale production en masse. Once the initial costs have been paid the price per unit during injection molded manufacturing is extremely low. The price also tends to drop drastically as more parts are produced. Other advantages include the following:
Low Scrap Rates with Injection Molding
Injection molding produces low scrap rates relative to traditional manufacturing processes like CNC machining which cut away substantial percentages of an original plastic block or sheet. This however can be a negative relative to additive manufacturing processes like 3D printing that have even lower scrap rates.
Waste plastic from injection molding manufacturing typically comes consistently from four areas:
The sprue
The runners
The gate locations
Any overflow material that leaks out of the part cavity itself (a condition called “flash”)
Thermoset material, such as an epoxy resin that cures once exposed to air, is a material that cures and would burn after curing if one attempt is made to melt it. Thermoplastic material, by contrast, is a plastic material that can be melted, cool and solidify, and then be melted again without burning.
With thermoplastic materials, they can be recycled and are used again. Sometimes this happens right on the factory floor. They grind up the sprues/runners and any reject parts. Then they add that material back into the raw material that goes into the injection molding press. This material is referred to as "re-grind".
Typically, quality control departments will limit the amount of regrind that is allowed to be placed back into the press. (Some performance properties of the plastic can degrade as it is molded over and over).
Or, if they have a lot of it, a factory can sell this re-grind to some other factory who can use it. Typically regrind material is used for low-quality parts that don't need high performance properties.
Injection Molding Leverages Repetition & Consistency
Injection molding is very repeatable. That is, the second part you produce is going to be practically identical to the first one etc. This is a wonderful characteristic when trying to produce brand consistency and part reliability in high volume production.
Injection_molding_plastic prototypes design and engineering firm
So… What Is The Downside To Injection Molding?
Because of the massive manufacturing scale usually involved in injection molding, small mistakes can have massive consequences - financially and logistically. While the margin of error is small, the implications are substantial.
Small Design Errors Have BIG Costs with Injection Molding
Upfront costs tend to be very high due to design, testing, and tooling requirements. If you are going to produce parts in high volumes you want to make sure you get the design right the first time. That is more complicated than you might think.
Getting the design right includes:
Designing and then prototyping the part itself to specification, usually on a 3D printer and prototyped in a different material
Designing an injection mold tool for an initial production round, to generate 300-1,000 prototypes
Refining every detail in the injection molded prototypes before mass production
If you have the right veteran voices at the table, this is still a fantastic option for the right projects.
Be Ready for High Tooling Costs for Injection Molding
Tooling is almost a project in and of itself and only one phase of the entire injection molding process.
Before you can produce an injection molded part you first have to design and prototype a part (probably via CNC or 3D printing).
Then you have to design and prototype a mold tool that can produce replicas of the part in volume.
Lastly, and typically after extensive testing in both of the aforementioned stages, you get to injection mold a part.
#engineering #cncmachine #injectionmolding
This machine is for sale! Visit the link below for more info on pricing and purchasing…
2014 Cincinnati Milacron MTS310, Capacity 310 Ton, Shot Size 36.2 oz, Tie Bar Spacing 26" x 26", Platen Size 37" x 37", Max Daylight 53.5", Min /Max Mold Height 7.9"/29.5", Clamp Stroke 45.6", Ejector Stroke 6.3", Screw Size 70 mm, Control B&R Control, Power Requirement 460V, Hours 15,800, FEATURES: Triple Core Pull, Robot Interface
What is Injection Molding?
Injection Molding is a manufacturing process for producing parts in large volume. It is most typically used in mass-production processes where the same part is being created thousands or even millions of times in succession.
Injection Molding Machine
Why You Might Want to Use Injection Molding
The principal advantage of injection molding is the ability to scale production en masse. Once the initial costs have been paid the price per unit during injection molded manufacturing is extremely low. The price also tends to drop drastically as more parts are produced. Other advantages include the following:
Low Scrap Rates with Injection Molding
Injection molding produces low scrap rates relative to traditional manufacturing processes like CNC machining which cut away substantial percentages of an original plastic block or sheet. This however can be a negative relative to additive manufacturing processes like 3D printing that have even lower scrap rates.
Waste plastic from injection molding manufacturing typically comes consistently from four areas:
The sprue
The runners
The gate locations
Any overflow material that leaks out of the part cavity itself (a condition called “flash”)
Thermoset material, such as an epoxy resin that cures once exposed to air, is a material that cures and would burn after curing if one attempt is made to melt it. Thermoplastic material, by contrast, is a plastic material that can be melted, cool and solidify, and then be melted again without burning.
With thermoplastic materials, they can be recycled and are used again. Sometimes this happens right on the factory floor. They grind up the sprues/runners and any reject parts. Then they add that material back into the raw material that goes into the injection molding press. This material is referred to as "re-grind".
Typically, quality control departments will limit the amount of regrind that is allowed to be placed back into the press. (Some performance properties of the plastic can degrade as it is molded over and over).
Or, if they have a lot of it, a factory can sell this re-grind to some other factory who can use it. Typically regrind material is used for low-quality parts that don't need high performance properties.
Injection Molding Leverages Repetition & Consistency
Injection molding is very repeatable. That is, the second part you produce is going to be practically identical to the first one etc. This is a wonderful characteristic when trying to produce brand consistency and part reliability in high volume production.
Injection_molding_plastic prototypes design and engineering firm
So… What Is The Downside To Injection Molding?
Because of the massive manufacturing scale usually involved in injection molding, small mistakes can have massive consequences - financially and logistically. While the margin of error is small, the implications are substantial.
Small Design Errors Have BIG Costs with Injection Molding
Upfront costs tend to be very high due to design, testing, and tooling requirements. If you are going to produce parts in high volumes you want to make sure you get the design right the first time. That is more complicated than you might think.
Getting the design right includes:
Designing and then prototyping the part itself to specification, usually on a 3D printer and prototyped in a different material
Designing an injection mold tool for an initial production round, to generate 300-1,000 prototypes
Refining every detail in the injection molded prototypes before mass production
If you have the right veteran voices at the table, this is still a fantastic option for the right projects.
Be Ready for High Tooling Costs for Injection Molding
Tooling is almost a project in and of itself and only one phase of the entire injection molding process.
Before you can produce an injection molded part you first have to design and prototype a part (probably via CNC or 3D printing).
Then you have to design and prototype a mold tool that can produce replicas of the part in volume.
Lastly, and typically after extensive testing in both of the aforementioned stages, you get to injection mold a part.
#engineering #cncmachine #injectionmolding