filmov
tv
Mantenimiento Predictivo | Inteligencia Artificial | Intralogística | SSI SCHAEFER
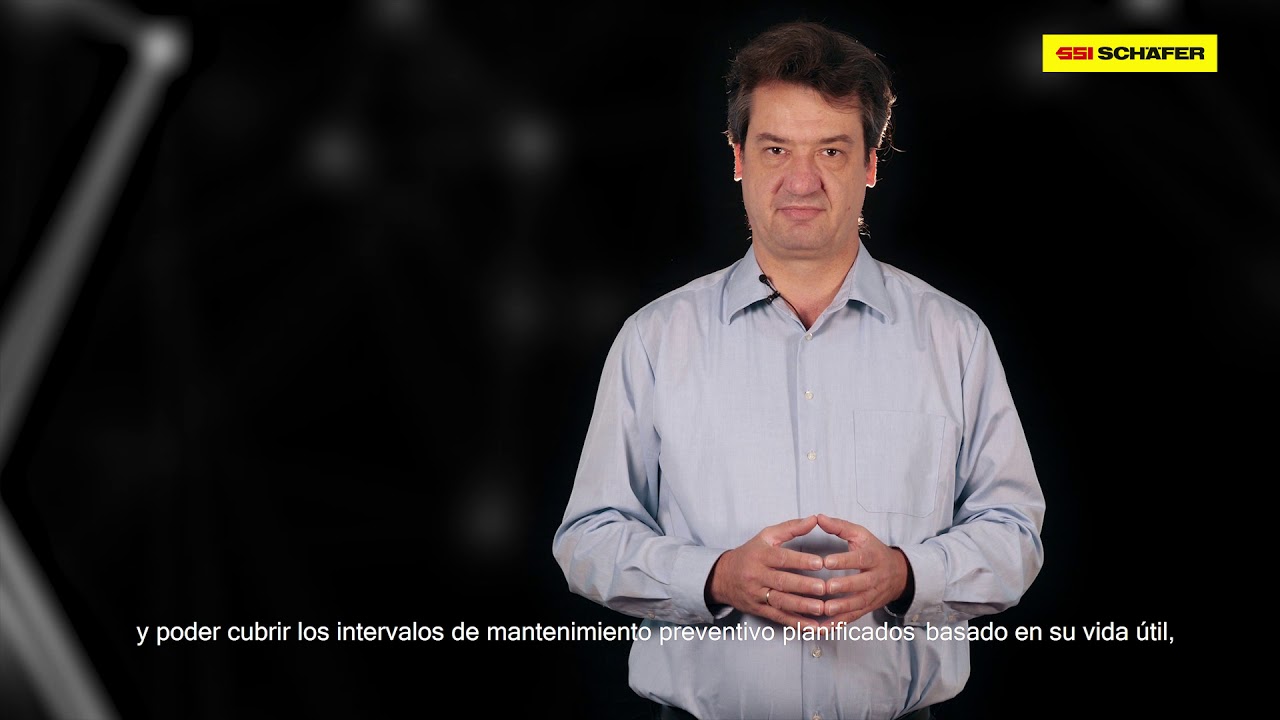
Показать описание
Intralogística y Mantenimiento Predictivo con Inteligencia Artificial.
El mantenimiento predictivo se utiliza para detectar el fallo inminente de un elemento del equipo operativo y para iniciar las medidas preventivas a fin de evitarlo, especialmente en almacenes automáticos. Hay cuatro pilares del mantenimiento predictivo:
- recopilación de datos
- transferencia de datos
- evaluación de datos
- medidas para mantener la funcionalidad
Para acercarse más al requisito de hardware de ser fiables (casi) al 100% en operativas de almacén de alto rendimiento, y para evitar el tiempo de inactividad de la producción, las tecnologías de IA también se utilizan para predecir la vida útil (restante) de las máquinas y los sistemas.
Por razones de coste, en la mayoría de las instalaciones industriales, la recopilación de datos todavía se lleva a cabo mediante pruebas y trabajos de mantenimiento. Sin embargo, debido a la caída de los costes de los sensores y los equipos de transferencia de datos, se puede establecer el seguimiento digital en tiempo real.
Los datos recopilados se guardan de forma centralizada y se pueden evaluar teniendo en cuenta diversos aspectos. Cuando existe la posibilidad de que surjan problemas, entonces es posible iniciar las medidas necesarias a tiempo, para evitar un mal funcionamiento o un largo período de inactividad del sistema.Los sistemas de IA adecuadamente capacitados ya pueden brindar asistencia aquí, sobre todo cuando se trata de analizar los grandes volúmenes de datos.
Para que el mantenimiento predictivo funcione correctamente, todos los movimientos relevantes de los componentes bajo consideración deben registrarse y guardarse, incluidos los parámetros asociados. Los factores que influyen en la fiabilidad operativa varían según el dispositivo que se esté considerando. Con un muelle, por ejemplo, estos factores son cada evento de apertura y cierre, junto con las acciones de todos los componentes involucrados, desde el sistema de control hasta el cilindro de presión y el desgaste del rodillo.
A partir de esto, el siguiente paso es el mantenimiento prescriptivo. Basado en una predicción del siguiente mal funcionamiento, se programa de forma proactiva y fuera de las horas pico el siguiente mantenimiento, la fecha y hora de servicio, el personal afectado, las piezas de recambios que se suministrarán.
Esta planificación puede ir tan lejos como para influir en los parámetros para el equipo en cuestión, de modo que se hace un uso medido de los recursos dañados para no provocar un mal funcionamiento antes de la fecha de mantenimiento programada.Además, sería incorrecto suponer que se trata de confiar únicamente en los sensores. Los sensores modernos y el enlace de los sensores hacen posible detectar valores incorrectos y la IA puede interpolarlos en combinación con otros valores de medición. Sin embargo, el problema no es siempre la máquina: el propio sensor puede tener un fallo que no necesariamente tiene que llevar a un tiempo de inactividad programado.
Desde 2017, ha habido una gran expectación alrededor de la inteligencia artificial (IA), como una las principales ramas que más evolucionarán dentro de las tecnologías de la información. Además de proporcionar una definición clara de conceptos y métodos en el tema de la IA, iremos publicando vídeos que muestren las perspectivas de uso que tienen las tecnologías de IA en la logística y en la gestión de almacenes.
• Aprendizaje automático (Machine Learning)
• Aprendizaje supervisado (Supervised Learning)
• Aprendizaje no supervisado (Unsupervised Learning)
• Aprendizaje semisupervisado (Semi-supervised Learning)
• Aprendizaje de refuerzo (Reinforcement Learning)
• Aprendizaje profundo (Deep Learning)
• Redes neuronales (Neuronal Networks)
• Computación cognitiva (Cognitive Computing)
Acabaremos la serie con casos prácticos de aplicación de la IA a la logística, la intralogística y la gestión de almacenes.
#thenextleveloflogistics
#ssischaefer #intralogística #thinktomorrow
El mantenimiento predictivo se utiliza para detectar el fallo inminente de un elemento del equipo operativo y para iniciar las medidas preventivas a fin de evitarlo, especialmente en almacenes automáticos. Hay cuatro pilares del mantenimiento predictivo:
- recopilación de datos
- transferencia de datos
- evaluación de datos
- medidas para mantener la funcionalidad
Para acercarse más al requisito de hardware de ser fiables (casi) al 100% en operativas de almacén de alto rendimiento, y para evitar el tiempo de inactividad de la producción, las tecnologías de IA también se utilizan para predecir la vida útil (restante) de las máquinas y los sistemas.
Por razones de coste, en la mayoría de las instalaciones industriales, la recopilación de datos todavía se lleva a cabo mediante pruebas y trabajos de mantenimiento. Sin embargo, debido a la caída de los costes de los sensores y los equipos de transferencia de datos, se puede establecer el seguimiento digital en tiempo real.
Los datos recopilados se guardan de forma centralizada y se pueden evaluar teniendo en cuenta diversos aspectos. Cuando existe la posibilidad de que surjan problemas, entonces es posible iniciar las medidas necesarias a tiempo, para evitar un mal funcionamiento o un largo período de inactividad del sistema.Los sistemas de IA adecuadamente capacitados ya pueden brindar asistencia aquí, sobre todo cuando se trata de analizar los grandes volúmenes de datos.
Para que el mantenimiento predictivo funcione correctamente, todos los movimientos relevantes de los componentes bajo consideración deben registrarse y guardarse, incluidos los parámetros asociados. Los factores que influyen en la fiabilidad operativa varían según el dispositivo que se esté considerando. Con un muelle, por ejemplo, estos factores son cada evento de apertura y cierre, junto con las acciones de todos los componentes involucrados, desde el sistema de control hasta el cilindro de presión y el desgaste del rodillo.
A partir de esto, el siguiente paso es el mantenimiento prescriptivo. Basado en una predicción del siguiente mal funcionamiento, se programa de forma proactiva y fuera de las horas pico el siguiente mantenimiento, la fecha y hora de servicio, el personal afectado, las piezas de recambios que se suministrarán.
Esta planificación puede ir tan lejos como para influir en los parámetros para el equipo en cuestión, de modo que se hace un uso medido de los recursos dañados para no provocar un mal funcionamiento antes de la fecha de mantenimiento programada.Además, sería incorrecto suponer que se trata de confiar únicamente en los sensores. Los sensores modernos y el enlace de los sensores hacen posible detectar valores incorrectos y la IA puede interpolarlos en combinación con otros valores de medición. Sin embargo, el problema no es siempre la máquina: el propio sensor puede tener un fallo que no necesariamente tiene que llevar a un tiempo de inactividad programado.
Desde 2017, ha habido una gran expectación alrededor de la inteligencia artificial (IA), como una las principales ramas que más evolucionarán dentro de las tecnologías de la información. Además de proporcionar una definición clara de conceptos y métodos en el tema de la IA, iremos publicando vídeos que muestren las perspectivas de uso que tienen las tecnologías de IA en la logística y en la gestión de almacenes.
• Aprendizaje automático (Machine Learning)
• Aprendizaje supervisado (Supervised Learning)
• Aprendizaje no supervisado (Unsupervised Learning)
• Aprendizaje semisupervisado (Semi-supervised Learning)
• Aprendizaje de refuerzo (Reinforcement Learning)
• Aprendizaje profundo (Deep Learning)
• Redes neuronales (Neuronal Networks)
• Computación cognitiva (Cognitive Computing)
Acabaremos la serie con casos prácticos de aplicación de la IA a la logística, la intralogística y la gestión de almacenes.
#thenextleveloflogistics
#ssischaefer #intralogística #thinktomorrow