filmov
tv
Why I bought this train rail.
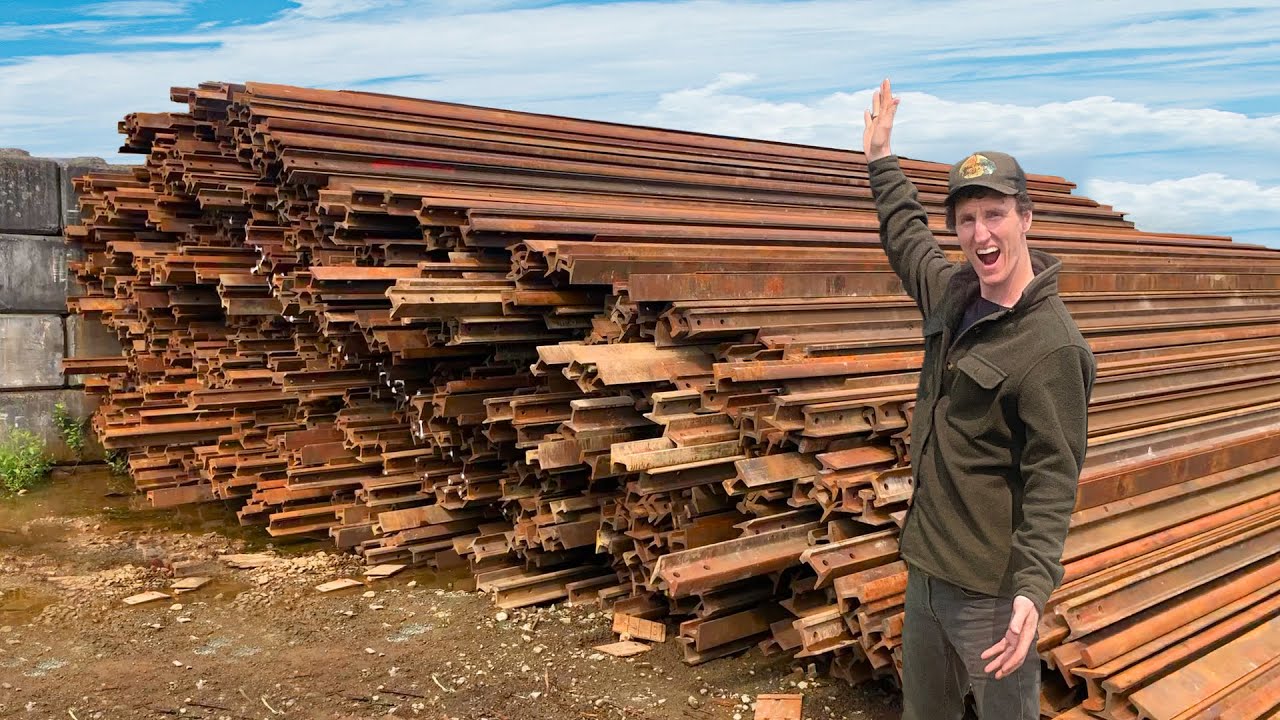
Показать описание
Meet the 89-Year Old Who Built a Train in His Backyard | WIRED
Electric Callboy - TEKKNO TRAIN (OFFICIAL VIDEO)
Intentional Train Derailment #shorts
Train Song | CoComelon Nursery Rhymes & Kids Songs
Trump Train Getting Stronger! Look Who Just Got On Board!
when the Freight Train got lost
This old lady got stuck between train doors and she got in the train #nycsubway
Strangers On The Train Chat #Shorts
Evolving a Train to MAX SPEED
Phonics Song | Bob The Train | The ABC Song by Bob The Train
Could You Live in a Train?
I Bought A Train & It Was A MISTAKE!... BRUTAL Transport Fever 2 #3
What Happened to the Crew of This Train? | Last Moments
Workers Break Windows to Rescue Passengers From Train #shorts
Train Song /Train Song
Building a Train to FASTEST!
Turkey Got Hit by a Train
Little Panda's Leg Got Injured | Super Train Rescue Team | Nursery Rhymes | Kids Songs | BabyBu...
Just Another Awami Journey | Lahore Jn to Rawalpindi With Weather's Hide & Seek
Bro got robbed by the train 💀 #fortnite #funny #gaming #fortniteshorts #fortniteclipz
How I Got to Train With the Shaolin Warrior Monks
I Bought a Bachmann Train Set - And Kinda Like It...
Billy Paul - Me and Mrs. Jones (Official Soul Train Video)
I Hitchhiked the World's Deadliest Train (20hrs across the Sahara)
Комментарии