filmov
tv
Why Flowcharts Are Essential for Process Improvement
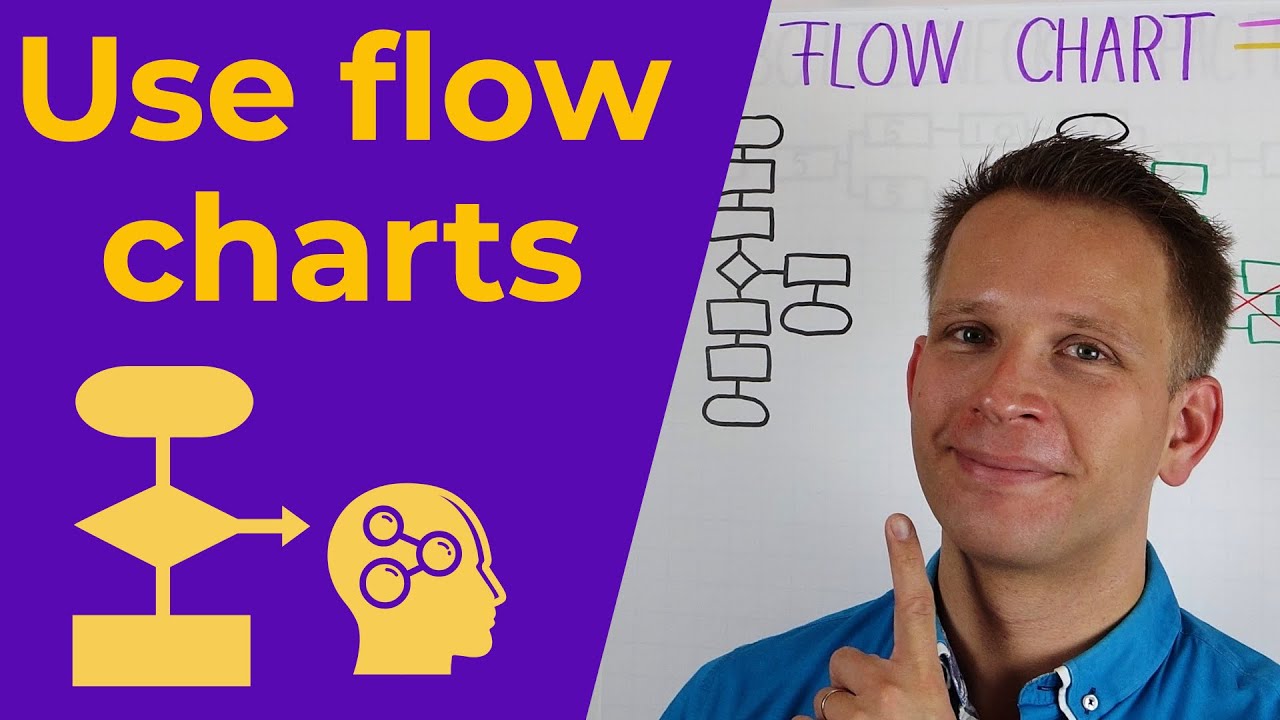
Показать описание
Flowcharts are powerful tools for understanding and improving any process, making them essential in Continuous Improvement. They are one of the seven Quality tools and incredibly effective for grasping and communicating the flow of production, business, and even service processes. Flowcharts break down complex processes into simple, visual steps, showing everything from start and end points to decision points and process stages. By putting the process in this visual form, you can better identify inefficiencies and highlight where improvements are most needed.
Many processes don’t operate precisely as documented in manuals. Flowcharting a process as it’s actually done versus as it’s documented often reveals extra steps or even skipped actions that impact efficiency and quality. This clarity can be crucial—especially when needing to correct discrepancies, prepare for audits, or even ensure consistent quality and training standards. Such process mapping makes visible where deviations or “hidden” steps occur, allowing everyone, from management to operators, to align on the real flow and address any gaps.
Beyond quality checks, flowcharts make it easier to see where resources are needed, identify bottlenecks, and decide on the scope of work for improvement initiatives. They simplify the way people talk about and understand processes, making flowcharting not just a step for audits but a practical tool for daily management. When processes are visualised, you’ll have a better grasp of sequential steps, interconnections, and potential improvements that benefit both productivity and the bottom line.
#ContinuousImprovement #ProcessMapping #QualityTools
00:00 Introduction to Flowcharts
03:06 Documenting Real vs. Documented Processes
06:48 Identifying Hidden Steps and Gaps
08:37 Using Flowcharts for Audits and Daily Management
10:36 Value of Visualisation in Process Improvement
Many processes don’t operate precisely as documented in manuals. Flowcharting a process as it’s actually done versus as it’s documented often reveals extra steps or even skipped actions that impact efficiency and quality. This clarity can be crucial—especially when needing to correct discrepancies, prepare for audits, or even ensure consistent quality and training standards. Such process mapping makes visible where deviations or “hidden” steps occur, allowing everyone, from management to operators, to align on the real flow and address any gaps.
Beyond quality checks, flowcharts make it easier to see where resources are needed, identify bottlenecks, and decide on the scope of work for improvement initiatives. They simplify the way people talk about and understand processes, making flowcharting not just a step for audits but a practical tool for daily management. When processes are visualised, you’ll have a better grasp of sequential steps, interconnections, and potential improvements that benefit both productivity and the bottom line.
#ContinuousImprovement #ProcessMapping #QualityTools
00:00 Introduction to Flowcharts
03:06 Documenting Real vs. Documented Processes
06:48 Identifying Hidden Steps and Gaps
08:37 Using Flowcharts for Audits and Daily Management
10:36 Value of Visualisation in Process Improvement
Комментарии