filmov
tv
stardelta starter indicator lights|panel light|ELECTRECA
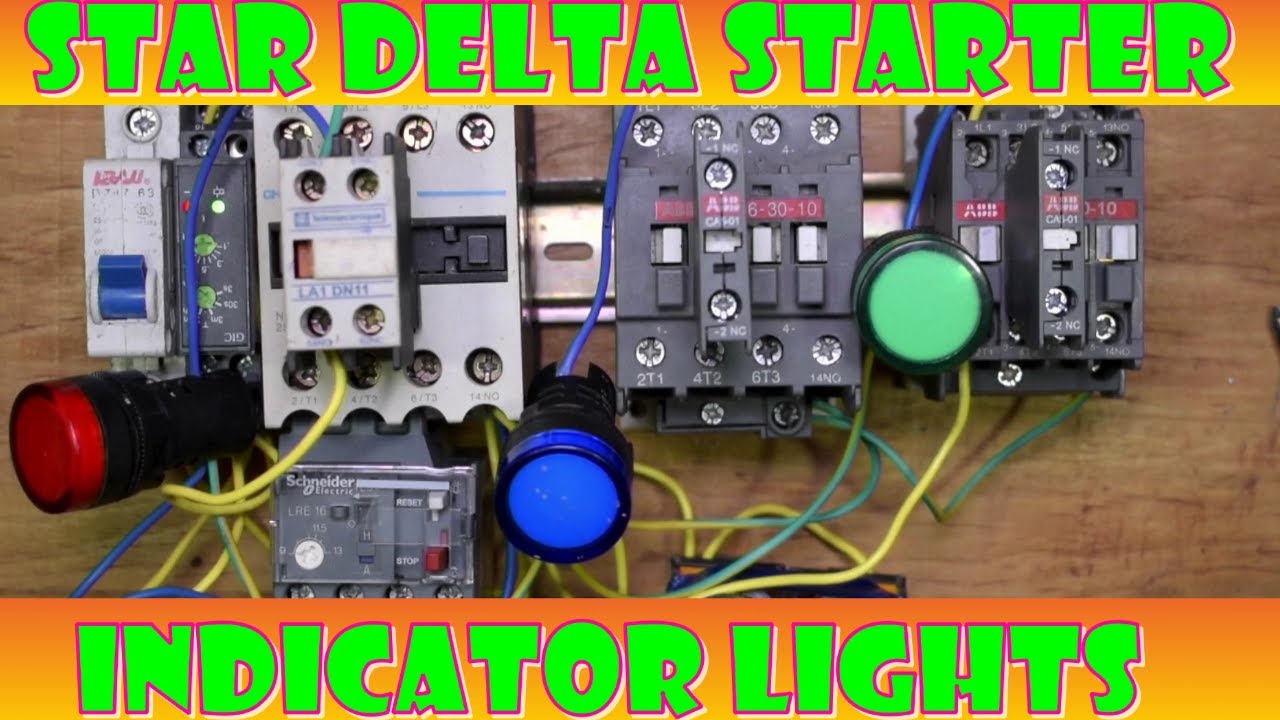
Показать описание
To wire the indicator lights you must, you must understand the CIRCUIT well... Since the lights are single-phase, you will connect each light to the A1 of the respective contactor.
The ON push button starts the circuit by initially energizing STAR CONTACTOR Coil of star circuit and Timer Coil (TIMER) circuit. When Star Contactor Coil (KM1) energized, Star Main and Auxiliary contactor change its position from NO to NC.
When Star Auxiliary Contact becomes NO to NC it’s complete The Circuit of Main contactor Coil ... so Main Contactor Coil energized and Main and Auxiliary Contact Change its Position from NO to NC. This sequence happens in a fraction of time.
After pushing the ON push button switch, the auxiliary contact of the main contactor coil which is connected in parallel across the ON push button will become NO to NC, thereby providing a latch to hold the main contactor coil activated which eventually maintains the control circuit active even after releasing the ON push button switch.
When Star Main Contactor closes its contacts, Motor runs and stay connected in STAR until the timer changes its contacts from NC to NO.
Once the time delay is reached its specified time delay, the timer changes its contacts from CLOSE TO OPEN.......meaning the star contactor will energies and delta contactor energises.
A normally close auxiliary contact from both star and delta contactors are also placed opposite of both star and delta contactor coils, these interlock contacts serve as safety switches to prevent simultaneous activation of both star and delta contactor coils so that one cannot be activated without the other deactivated first. Thus, the delta contactor coil cannot be active when the star contactor coil is active, and similarly, the star contactor coil cannot also be active while the delta contactor coil is active.
The control circuit above also provides two interrupting contacts to shut down the motor. The OFF push button switch break the control circuit and the motor when necessary. The thermal overload contact is a protective device which automatically opens the STOP Control circuit in the case when motor overload current is detected by the thermal overload relay, this is to prevent burning of the motor in case of excessive load beyond the rated capacity of the motor is detected by the thermal overload relay.
At some point during starting it is necessary to change from a star connected winding to a delta connected winding. Power and control circuits can be arranged to this in one of two ways – open transition or closed transition.
WATCH MORE VIDEOS HERE
The ON push button starts the circuit by initially energizing STAR CONTACTOR Coil of star circuit and Timer Coil (TIMER) circuit. When Star Contactor Coil (KM1) energized, Star Main and Auxiliary contactor change its position from NO to NC.
When Star Auxiliary Contact becomes NO to NC it’s complete The Circuit of Main contactor Coil ... so Main Contactor Coil energized and Main and Auxiliary Contact Change its Position from NO to NC. This sequence happens in a fraction of time.
After pushing the ON push button switch, the auxiliary contact of the main contactor coil which is connected in parallel across the ON push button will become NO to NC, thereby providing a latch to hold the main contactor coil activated which eventually maintains the control circuit active even after releasing the ON push button switch.
When Star Main Contactor closes its contacts, Motor runs and stay connected in STAR until the timer changes its contacts from NC to NO.
Once the time delay is reached its specified time delay, the timer changes its contacts from CLOSE TO OPEN.......meaning the star contactor will energies and delta contactor energises.
A normally close auxiliary contact from both star and delta contactors are also placed opposite of both star and delta contactor coils, these interlock contacts serve as safety switches to prevent simultaneous activation of both star and delta contactor coils so that one cannot be activated without the other deactivated first. Thus, the delta contactor coil cannot be active when the star contactor coil is active, and similarly, the star contactor coil cannot also be active while the delta contactor coil is active.
The control circuit above also provides two interrupting contacts to shut down the motor. The OFF push button switch break the control circuit and the motor when necessary. The thermal overload contact is a protective device which automatically opens the STOP Control circuit in the case when motor overload current is detected by the thermal overload relay, this is to prevent burning of the motor in case of excessive load beyond the rated capacity of the motor is detected by the thermal overload relay.
At some point during starting it is necessary to change from a star connected winding to a delta connected winding. Power and control circuits can be arranged to this in one of two ways – open transition or closed transition.
WATCH MORE VIDEOS HERE
Комментарии