filmov
tv
Finite element modelling of the Incremental Cold Flow Forming in MoFEM UKACM2021
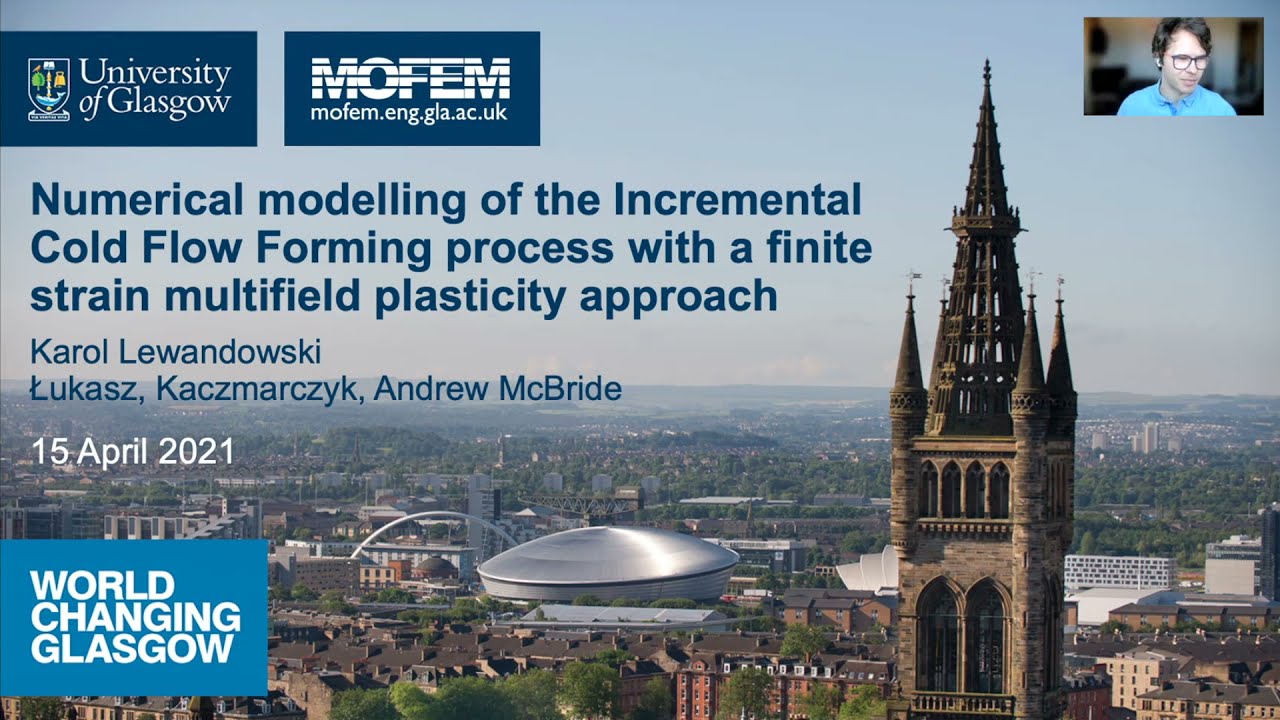
Показать описание
A short presentation about recent developments in numerical modelling of the Incremental Cold Flow Forming process with a finite strain multifield plasticity approach.
UKACM 2021 Conference
The incremental cold flow forming process manufactures axisymmetric components with remarkable geometrical accuracy and improved material properties in comparison with traditional methods. Due to nature of the process, including extreme plastic deformations, contact with series
of rollers, and heat dissipation, it has been exceptionally difficult to simulate, thus, not allowing
industry to take full advantage of this technique. A robust, reliable predictive numerical modelling
is crucial to improve understanding and optimise flow forming process.
To tackle the challenges associated with simulating such manufacturing processes, we utilise a multifield plasticity approach. Unlike classical internal variable methods for plasticity, the measures of plastic deformation are directly approximated via the finite element basis functions in L2 space.
This approach is highly flexible, allowing for straightforward coupling with other physical phenomena like e.g. rolling contact and heat transfer. In this contribution, we extend the small strain multifield plasticity formulation with additive kinematic approach proposed by Miehe, et. al.
The framework allows for expressing classical constitutive small strain models in a finite-strain
setting by introducing a logarithmic strain measure. Performance of the proposed implementation
is demonstrated by the classical benchmark examples of the Cook’s membrane problem and the
necking of a rod. In the final example, the current progress of the framework is tested against full
simulation of flow forming process with simplified boundary conditions, allowing for the identification of the future challenges. The proposed approach is implemented in the open-source finite element library MoFEM.
UKACM 2021 Conference
The incremental cold flow forming process manufactures axisymmetric components with remarkable geometrical accuracy and improved material properties in comparison with traditional methods. Due to nature of the process, including extreme plastic deformations, contact with series
of rollers, and heat dissipation, it has been exceptionally difficult to simulate, thus, not allowing
industry to take full advantage of this technique. A robust, reliable predictive numerical modelling
is crucial to improve understanding and optimise flow forming process.
To tackle the challenges associated with simulating such manufacturing processes, we utilise a multifield plasticity approach. Unlike classical internal variable methods for plasticity, the measures of plastic deformation are directly approximated via the finite element basis functions in L2 space.
This approach is highly flexible, allowing for straightforward coupling with other physical phenomena like e.g. rolling contact and heat transfer. In this contribution, we extend the small strain multifield plasticity formulation with additive kinematic approach proposed by Miehe, et. al.
The framework allows for expressing classical constitutive small strain models in a finite-strain
setting by introducing a logarithmic strain measure. Performance of the proposed implementation
is demonstrated by the classical benchmark examples of the Cook’s membrane problem and the
necking of a rod. In the final example, the current progress of the framework is tested against full
simulation of flow forming process with simplified boundary conditions, allowing for the identification of the future challenges. The proposed approach is implemented in the open-source finite element library MoFEM.
Комментарии