filmov
tv
MILESTONE: Launcher's 3D printed Copper Alloy E-1 🚀engine test was a success.
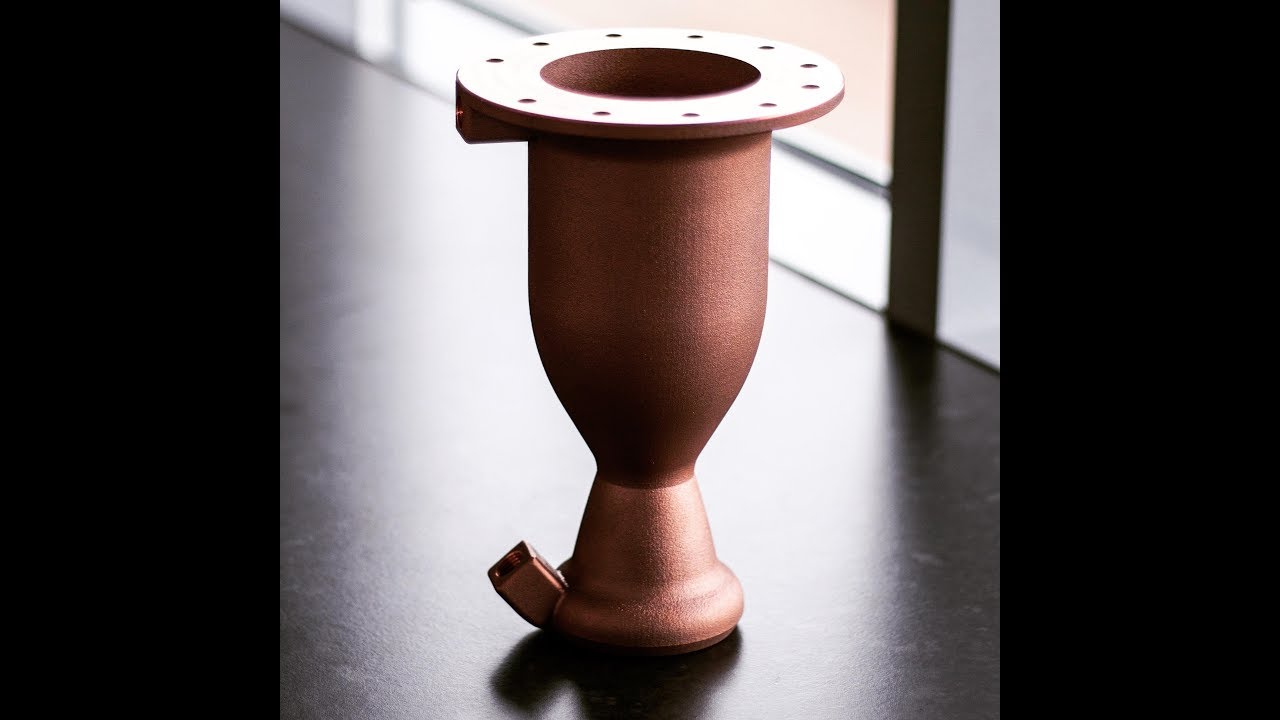
Показать описание
MILESTONE: Launcher's 3D printed Copper Alloy E-1 🚀engine test was a success. Reaching for 30-seconds the highest temperature for LOX/RP-1 (mix ratio 2.8) without any damage to the chamber. The highest performance rocket engines are made of copper alloy - but we only recently had access to 3D print copper alloy (CuCrZr) thanks to our partner EOS and their M290 machine. Most 3D printed rocket engines are produced today in Inconel alloy - which is a compromise in terms of cooling capability usually requiring a lower combustion temperature and as a result a lower performance engine. 3D printed copper alloy is the solution when performance matters.
Next step - Increasing in steps the combustion pressure to reach our E-2 flight engine goal of 1,400psi. #3dprinted #propulsion #copper #cucrzr
Next step - Increasing in steps the combustion pressure to reach our E-2 flight engine goal of 1,400psi. #3dprinted #propulsion #copper #cucrzr
Launcher E-2 - 3D printed combustion chamber automatic de-powdering
Launcher E-2 - 3D printed combustion chamber automatic de-powdering #2
Launcher x EOS - A partnership for 3D printed rocket engines.
Launcher E-2 liquid 🚀 engine LOX turbopump reaches all performance goals.
FDM 3D printed rocket engine
Parts of a rocket engine being Metal 3D Printed | Rapid DMLS
Successful Launcher E-2 test #2 (2s burp)
Launcher Live Stream
Launcher E1 | 25s Duration Blue test fire | Launcher - KSP
3D printed Rocket
3D printing of a small rocket in the lab of OHB
Introducing Launcher Orbiter
3Din30: What's Fueling Launcher's Race to Space?
3D Printed Rocket - Medusa I Test Launch - Aerotech G79W
Rutherford engine
These Engineers Want to 3D Print an Entire Rocket in 60 Days
Sirius Space Services: A French Launch Provider for Small to Medium Size Satellites
Which Motorola phone is Stronger? 😱 Break Test #android #moto #break #bend #motorola #test
Show Newcomers ARC Discuss their 3D Printed Engine Components
Building a rocket — one failure at a time
World's Largest Crowdfunded Rocket Engine - BPM100 Animation
In-Depth View of Relativity Space's Terran 1
Half Cat Launch 2 | Onboard Video
Launcher Logo Origin (2017-2021 Launcher Logo Version)
Комментарии