filmov
tv
Why Don't I Just Make A Few Pedals?
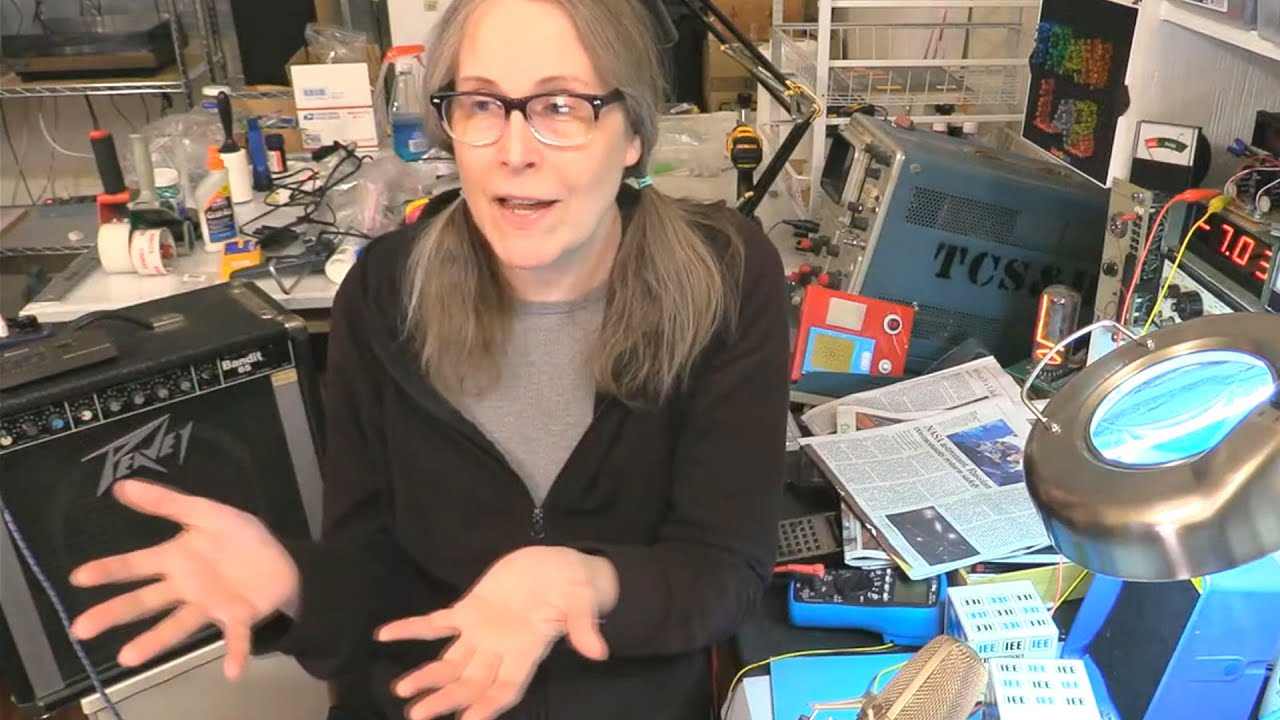
Показать описание
Answering questions streamed live on April 2, 2022 - this one is about why I don't just crank out some more pedals. Easy peasy!
#Frantone #FranLab #stream
- Intro Music by Fran Blanche -
#Frantone #FranLab #stream
- Intro Music by Fran Blanche -
The procrastination cure you don't want to hear
Why don't they just make a bridge here
Why Don't They Make BIGGER CPUs?
Jordan Peterson - What To Do If I Don't Have Any Goals?
What Hyperrealistic Cake Should I Make Next?!
Gotye - Somebody That I Used To Know (feat. Kimbra) [Official Music Video]
3 Things in Japan that Just Make Sense but Don't Have Elsewhere😲
You got it, dude #shorts
'Bananas Don't Just Melt, They Make You Smart!' #cartoon #art #aiart
Want To Be Happy? Don't Make This Mistake | Dr Julie
Why There Is No 'E' Grade 🤔 (EXPLAINED)
Bebe Rexha - Meant to Be (feat. Florida Georgia Line) [Official Music Video]
Don't Just Learn To Code, Learn To Create | Justin Richards | TEDxYouth@ColumbiaSC
Why Don’t Slower F1 Teams Copy The Fastest Car?
5 Sneaky ways people are disrespecting you | Mel Robbins #Shorts
Rubik’s Cube solved with 2 Moves???? 😅
'Don't Learn to Code, But Study This Instead...' says NVIDIA CEO Jensen Huang
you don't ACTUALLY have 'nothing to wear.' you're just shopping wrong.
3 Things in Japan that just make sense but don't have elsewhere 🇯🇵 #japan #japanthings #japanto...
Why hasn't Apple invented this yet?!
How To Make Custom Trigger Stops For *FREE*... #Shorts
Wait they don’t love you - Dancechallenge 🔥 #foryou #dance #tutorial
Most People Don't Know How Bikes Work
do NOT age-shame Erica #StrangerThings #Netflix
Комментарии