filmov
tv
Testing the TAS on the Tormach 770
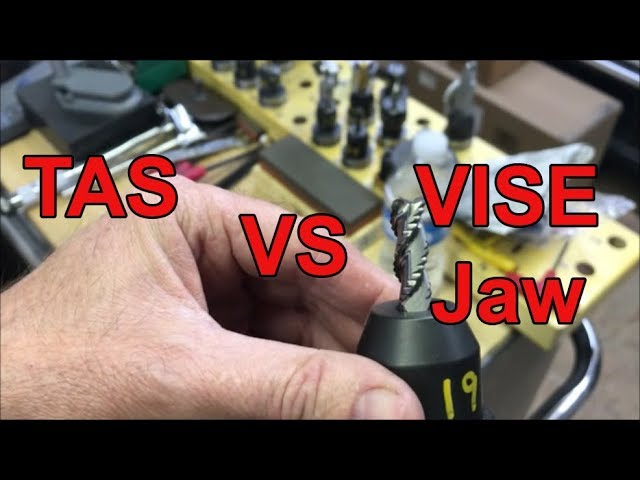
Показать описание
In this video I test the TAS from Lakeshore Carbide on my Tormach 770.
Please direct all correspondence to:
Craig's Machine Shop
2753 E. Broadway Rd Ste. 101-PMB416
Mesa, Az 85204-1570
Please direct all correspondence to:
Craig's Machine Shop
2753 E. Broadway Rd Ste. 101-PMB416
Mesa, Az 85204-1570
ISTQB Test Automation Engineer | 5.3 Logging of the TAS and the SUT | ISTQB Tutorials
😱 MAÏS XXL 2024 : TEST NOUVEAU FENDT 620 SANS VOLANT ! 1050 sur le TAS + SURPRISE à la FIN🌽
Fastest goal ever - 100,000 kph ground pinch [TAS]
Getting Over It's HARDEST Map Done in 90 SECONDS TAS (Tool-Assisted Speedrun)
TAS | THE AIR DRIBBLE TEST (BOOMER)
How to prepare for TAS| #MRCPCH |Theory and science|@MRCPCHforbeginners #mrcpch
ISTQB Test Automation Engineer | 5.1 Selecting the TAS Metrics (Part-3) | ISTQB Tutorials
ISTQB Test Automation Engineer | 3.3.3 Synchronization between TAS and SUT (Part-1) | ISTQB Tutorial
Starlink V4 Gen 3 Kit: Unboxing, Performance Testing, And Gen 2 Comparison In The Philippines!
ISTQB Test Automation Engineer | 3.3.1 Introduction to TAS Development | ISTQB Tutorials
(TAS) Mensa Norway Online IQ Test Max Score Speedrun (00:09.042)
ISTQB Test Automation Engineer | 3.3.2 Compatibility Between TAS and SUT | ISTQB Tutorials
[TAS] Fox Does Every Target Test Stage (SSBM)
ISTQB Test Automation Engineer | 5.1 Selecting the TAS Metrics (Part-2) | ISTQB Tutorials
Testing Minecraft TAS
ISTQB Test Automation Engineer | 3.3.3 Synchronization between TAS and SUT (Part-2) | ISTQB Tutorial
Osmos Demo - TAS test
Tech Talk Live #104: Test Automation System (TAS)
ISTQB Test Automation Engineer | 3.3.4 Building Reuse into the TAS | ISTQB Tutorials
Tasmania Police Tests (TAS) - How to Pass
TAS Telly Bridging Test
Portal - Chamber 13 - TAS Test Run
Reacting to the PERFECT Mario Odyssey Speedrun (55:28 - Human TAS)
Ocarina of Time ~ Testing Analog Slide. (TAS)
Комментарии