filmov
tv
Thinking PLM4 0 What's wrong with Digital Continuity?
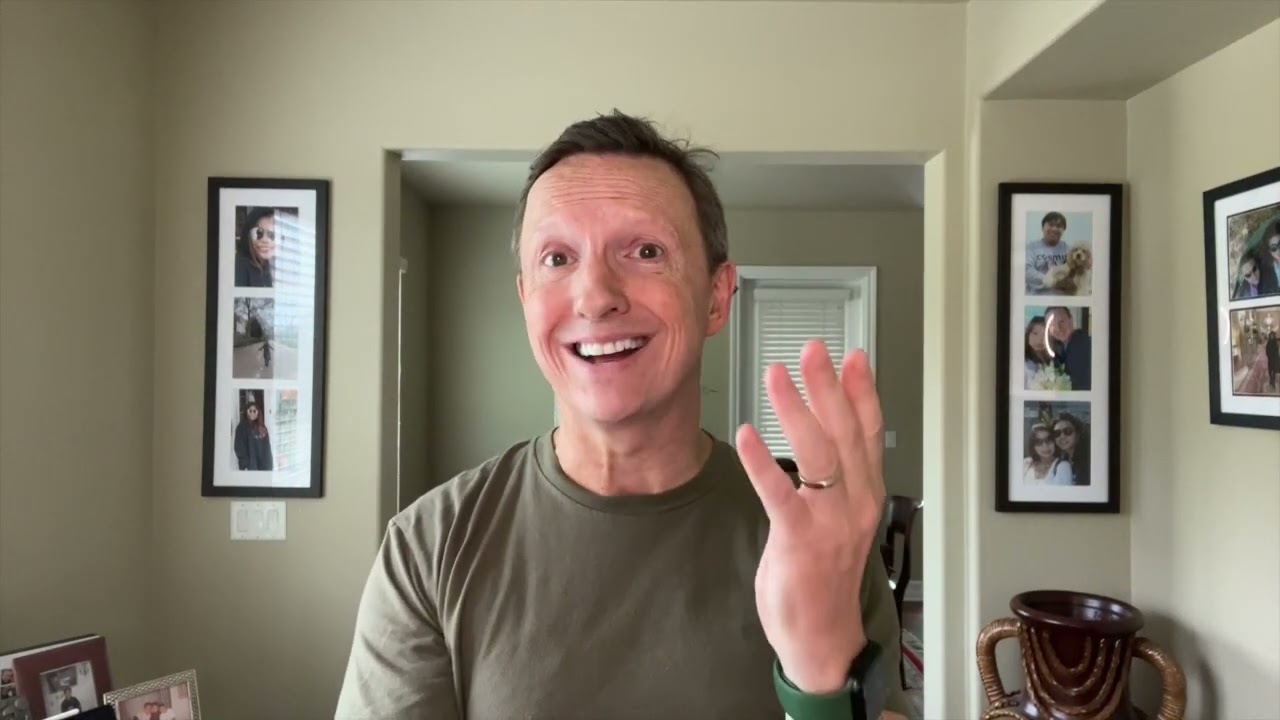
Показать описание
Each day I look on with an ever increasing enthusiasm and passion for Digital Continuity.
Over the last few years I've consistently shared my love of working with some of the great innovators, and tried to provide solutions that help accelerate the creation and delivery of these new smarter and more personalized products that we all want
Today, it's great to be part of some of THE progressive and innovative products created and to see how organizations and supply chains have responded to dramatically new market conditions and shifts in supply and demand
Everywhere, I am seeing a revitalized appreciation of the importance of maintaining digital continuity.
In your digital innovative product lifecycle journey, changes can be adopted relatively quickly at the detail level,
often through new software functions or applications,
however at a higher level, the changes to your general strategic processes or overall business approach, often happen ecosystem-wide
and it does take more time.
The COVID era exposed so many weaknesses across our “modern organizations”, but the one area that’s stood out for me, was a lack of seamless integration and therefore
true digital continuity
Today it’s broken! silos remain throughout too many enterprises:
Design thinking is disconnected from CAD, from engineering and from the whole product lifecycle approach and that’s before we even talk about manufacturing and ERP or CRM
It’s led to a move away from manufacturer-based supply chain ecosystems.
Companies have been essentially working with disconnected supply data that makes digital continuity almost impossible
What I'm seeing and hearing each day:
1. Marketing teams struggling to understand customers’ expectations and opinions =
Which means They can’t give meaningful customer feedback to product design teams.
2. Engineering and design teams are unable to harness IoT data
When they want to improve product performance, they must rely on product testing alone.
The data flowing between design, engineering, production and after-sales is often incomplete or incorrect.
This creates inefficiencies, and impairs the quality of products and services.
And #3.
Production planning isn’t closely tied to demand
Teams lack insight into inventory levels, because there’s no smooth flow of information between planning, execution and warehouse management.
and 4. Lastly Customer service and satisfaction levels are low, and this has a knock-on effect on company reputations.
& The root cause of this?
Product lifecycle management is too often limited to fixing items that are under warranty.
Obsolete and disconnected processes, mean many companies aren’t ready for the new and ongoing 4IR,
and they’re getting left behind.
So, Why are businesses struggling to achieve Digital Continuity?
For me, There are three main blockers:
1. An inability to synchronize different functions’ activities early in the design and development stage.
2. Another blocker is Creating, accessing and reusing information on how a product was designed, manufactured and serviced.
3. It's Difficulties accessing data from products and customers to drive innovation –
in fact only 25% of manufacturers, are using data to deliver actionable insights for product innovation, and 60% of those say they don’t have the analytics capabilities to mine the data generated from connected ecosystems.
Tracking and managing all of this “digital” data requires new capabilities and mindsets.
Stop the silos and build teams
The move is to where organizations collaborate in real time within the same digital environment
and
on the same virtual product data set industry derived plm processes
that are built into a single platform,
It's where all your stakeholders can simplify their operations by using these more generic or out of the box industry processes that are specifically designed to support a data driven and model based approach.
See you next week
Over the last few years I've consistently shared my love of working with some of the great innovators, and tried to provide solutions that help accelerate the creation and delivery of these new smarter and more personalized products that we all want
Today, it's great to be part of some of THE progressive and innovative products created and to see how organizations and supply chains have responded to dramatically new market conditions and shifts in supply and demand
Everywhere, I am seeing a revitalized appreciation of the importance of maintaining digital continuity.
In your digital innovative product lifecycle journey, changes can be adopted relatively quickly at the detail level,
often through new software functions or applications,
however at a higher level, the changes to your general strategic processes or overall business approach, often happen ecosystem-wide
and it does take more time.
The COVID era exposed so many weaknesses across our “modern organizations”, but the one area that’s stood out for me, was a lack of seamless integration and therefore
true digital continuity
Today it’s broken! silos remain throughout too many enterprises:
Design thinking is disconnected from CAD, from engineering and from the whole product lifecycle approach and that’s before we even talk about manufacturing and ERP or CRM
It’s led to a move away from manufacturer-based supply chain ecosystems.
Companies have been essentially working with disconnected supply data that makes digital continuity almost impossible
What I'm seeing and hearing each day:
1. Marketing teams struggling to understand customers’ expectations and opinions =
Which means They can’t give meaningful customer feedback to product design teams.
2. Engineering and design teams are unable to harness IoT data
When they want to improve product performance, they must rely on product testing alone.
The data flowing between design, engineering, production and after-sales is often incomplete or incorrect.
This creates inefficiencies, and impairs the quality of products and services.
And #3.
Production planning isn’t closely tied to demand
Teams lack insight into inventory levels, because there’s no smooth flow of information between planning, execution and warehouse management.
and 4. Lastly Customer service and satisfaction levels are low, and this has a knock-on effect on company reputations.
& The root cause of this?
Product lifecycle management is too often limited to fixing items that are under warranty.
Obsolete and disconnected processes, mean many companies aren’t ready for the new and ongoing 4IR,
and they’re getting left behind.
So, Why are businesses struggling to achieve Digital Continuity?
For me, There are three main blockers:
1. An inability to synchronize different functions’ activities early in the design and development stage.
2. Another blocker is Creating, accessing and reusing information on how a product was designed, manufactured and serviced.
3. It's Difficulties accessing data from products and customers to drive innovation –
in fact only 25% of manufacturers, are using data to deliver actionable insights for product innovation, and 60% of those say they don’t have the analytics capabilities to mine the data generated from connected ecosystems.
Tracking and managing all of this “digital” data requires new capabilities and mindsets.
Stop the silos and build teams
The move is to where organizations collaborate in real time within the same digital environment
and
on the same virtual product data set industry derived plm processes
that are built into a single platform,
It's where all your stakeholders can simplify their operations by using these more generic or out of the box industry processes that are specifically designed to support a data driven and model based approach.
See you next week